KLN Ultraschall is one of the world’s leading manufacturers of machines, systems and tools for welding and joining plastic parts as well as industrial cleaning technology. The complex technologies of plastic joining technology and ultrasonic and spray cleaning technology are the main activities of our company. Here on two plants in Heppenheim our team of experts with 180 employees are working on different projects.
Since January 2000, the KLN Ultraschall AG has been a company of the Crest Ultrasonics Corp, Trenton, New Jersey/USA. The CREST Group employs more than 1.000 people at 20 locations in 12 countries.
Interview with Sophie Dolata, Sales Engineer and Project Manager at KLN Ultraschall AG.
Easy Engineering: What are the main areas of activity of the company?
Sophie Dolata: Joining and welding technology: We offer solutions for thermal and friction processes. Thermal processes include hot plate and infrared welding as well as hot riveting and hot air riveting. The friction processes are vibration welding, rotation welding and ultrasonic welding. KLN offers a selection of standard systems as well as complex special solutions with various levels of automatization.
Industrial cleaning: We offer the right cleaning solution for customer-specific applications. Both standard solutions as well as customized machines are part of our portfolio. Starting with stand-alone units like benchtops up to fully automated inline solutions integrated into production lines are possible. We are capable to handle aqueous and solvent-based processes and systems.
E.E: What’s the news about new products/services?
S.D: Joining and welding technology: In the last years, we have focused on the development of machines for the production of hydrogen tanks. We have developed a machine and tool concept that makes it possible to weld plastic tanks that are later used as tanks for hydrogen. The technology enables the welding of pipe halves as well as the welding of mounting adapters to the tank. The welding machine works on the principle of hot plate or infrared welding. The modular design of the welding system allows the adaptation to the size of the components to be welded. Tanks up to a length of 6 meters and a maximum diameter of 700 mm can be processed. Different tank sizes are also possible with appropriate design adjustments. Optionally, the system can be equipped with a planing unit, which creates a flat joining surface before welding. A flaming station for surface treatment can also be integrated. The integrated exhaust system removes welding fumes and planing waste. The machine concept allows a modular design for variable number of welding positions.
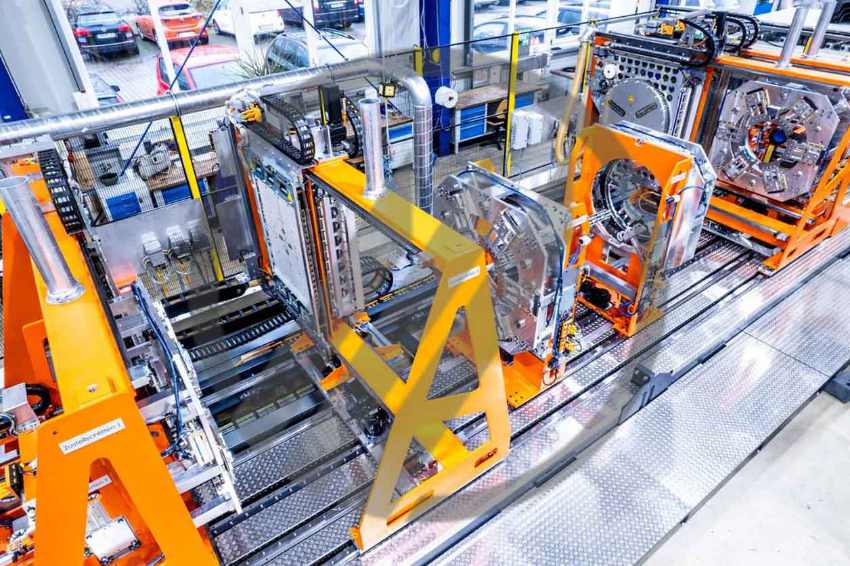
Industrial cleaning: KLN as part of the Crest Ultrasonics Europe Group is excited to announce the launch of our new Solvac MA dual ultrasonic precision cleaning system. This process is the direct result of an extensive three-year research and development program, focused on understanding the characteristics and molecular properties of modified alcohols when combined with ultrasonic energy.
The Solvac MA is equipped with the latest patented dual-frequency ultrasonic technology, generating higher levels of in-process power through multi-frequency streaming. This innovative and highly efficient breakthrough in cleaning technology ensures that the highest levels of cleanliness are consistently achieved.
Equipped with a temperature control probe and alarm system, the Solvac MA ensures protection from overheating, maintaining the integrity of both your components and the solvent. This precise temperature management contributes to consistent cleaning results and solvent longevity.
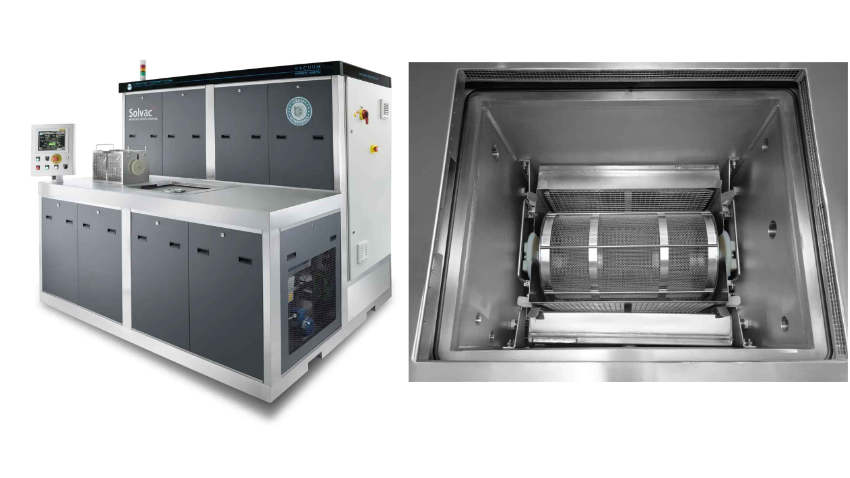
E.E: What are the ranges of products/services?
S.D: We offer the customer complete support, starting with the initial contact and comprehensive advice, through the development of a reliable concept to the finished system of your choice, including various levels of automation. After sales is a top priority for us. Colleagues who are excellently trained in their respective fields, short response times and availability even outside normal business hours form the basis of our satisfied customers.
E.E: What is the state of the market where you are currently active?
S.D: The market in which KLN operates includes several areas. We are mainly active in the automotive and electronics sector, but we also operate in the white goods, consumer goods and medical technology markets. Particularly in the field of precision cleaning, we are often part of the value chain in the optics, pharmaceutical and aerospace industries.
E.E: What can you tell us about market trends?
S.D: As the market and customer requirements are constantly changing, we are always interested in new technologies and developments. Alternative drive technologies are currently a major topic on the market, which also has an impact on the field of plastic welding and parts cleaning. For this reason, KLN continues to hold on to the concept of special machine construction to meet the changing requirements. The demand for high-purity parts is increasing all the time. With our systems, we support companies in achieving their quality targets and increasing the proportion of good parts
E.E: What estimations do you have for the beginning of 2024?
S.D: For 2024, we continue to see developments and requests in the area of alternative drive technologies but also the use of recycled materials, which will increasingly be part of the welding requests.
Industrial cleaning technology is increasingly becoming an indispensable part of the production chain and guarantees functionality, longer service life and less maintenance of components and assemblies.