Legor specializes in manufacturing premium metal alloys, plating solutions, and powders tailored for additive manufacturing, catering specifically to their core industries: Jewelry & Luxury and Fashion & Decorative.
Interview with Fabio Di Falco, Marketing & Customer Support Manager at Legor.
Easy Engineering: What are the ranges of products and what types of services do you offer?
Fabio Di Falco: At Legor, we take a holistic approach to our offerings: rather than discussing products in isolation, we focus on delivering integrated solutions. This includes the provision of optimal alloy combinations paired with plating solutions, meticulously designed to meet the distinct requirements of the jewelry and fashion sectors.
While the quality of our products is undeniably crucial, what truly distinguishes us is our profound expertise and commitment to resolving any challenges that may arise during the application and processing of our products. Our dedication is exemplified through our comprehensive support service, ensuring proximity to our clients and guiding them through every phase of the process, thereby reinforcing our ethos of responsibility, sustainability, and customer care, combined with our specialization in the science of precious metals and innovation.
E.E: Which are the most innovative products / solutions and what special features do they have?
F.D.F: Legor’s products are at the forefront when it comes to sustainability: they are made exclusively with precious metals (Gold, Silver, Platinum, Palladium and Rhodium) from 100% recycled sources, with a fully documented Chain of Custody. In addition, Legor is able to guarantee that certain non-precious metals (Silicon, Tin, Indium, Cobalt, Gallium, Germanium, Ruthenium and Copper) come 100% from recycled sources for products pertaining to the UNI EN ISO 14021:2021 certification obtained in October 2022.
What is more, our drive for progress, innovation and sustainability meld to give life to the Legor 3D Metal Hub: an innovative center whose scope is to experiment and produce jewelry, fashion accessories and industrial parts, starting from metal powders, and employing revolutionary Binder Jet technology. Through collaborations with leading players in the sector and thanks also to a partnership deal with HP, Legor is the first company to introduce this new technology and to make the advantages of additive manufacturing available for developing new solutions in different industries, pairing flexibility and creativity with productivity optimization.
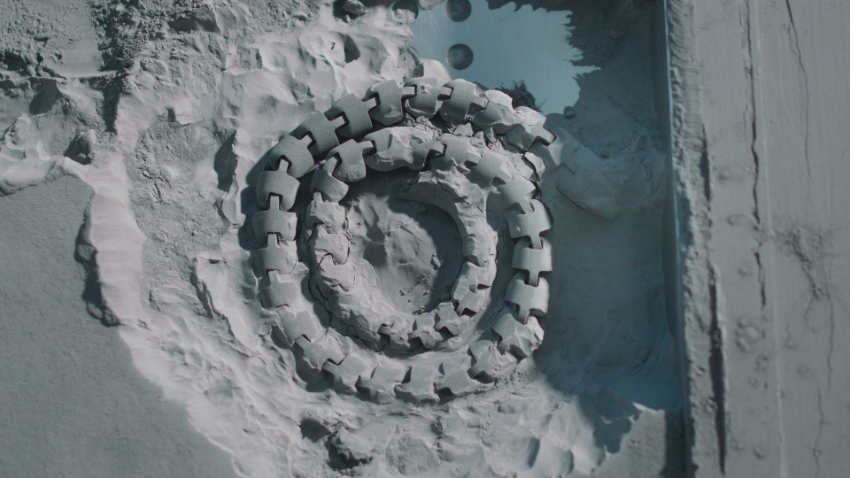
E.E: How do your best products / solutions work?
F.D.F: Focusing on the 3D Metal Binder Jet Technology, the ultra-fine metal powder (between 5μm and 25μm) is the starting point for creating components, both precious and non-precious. Currently, Legor is capable of printing in steel, bronze, silver, and platinum. Next step will be 18kt gold powder. Upon receiving the CAD model of the object to be produced, the dimensions are scaled, anticipating volumetric shrinkage due to the printing process. A dedicated software slices the pieces, obtaining 2D images from the 3D objects. The subsequent phases of the process are:
Printing: in the 3D printer, a roller spreads a layer of powder inside a build unit, with a predefined thickness. Subsequently, the print heads selectively apply a binder, according to the previously obtained 2D images. This step is repeated until the desired height of the objects is achieved.
Curing: the build unit is placed in a Curing Station, where a curing treatment occurs at around 150°C; in this way, the binder activates, and the objects are obtained still fragile, immersed in a powder bed. After a thorough Decaking and Depowdering process, the objects are placed in the sintering furnace.
Sintering: this phase consists of 3 stages more: debinding (the binder evaporates completely, leaving the pieces composed only of powder grains), sintering (the particles begin to coalesce, forming a metallurgical bond, and this is where most of the volumetric shrinkage of the process occurs), and cooling (the cooling of the pieces is controlled to avoid residual stresses and undesired cracks).
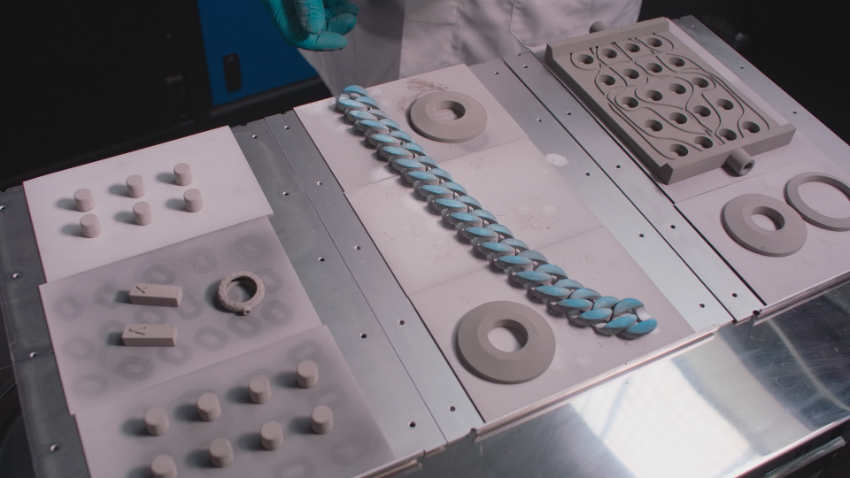
This technology represents an alternative to other additive manufacturing technologies, offering several benefits, such as:
- no need for mold
- rapid realization of sampling
- production of multiple parts, even different parts, during the same cycle
- zero waste – reusable powder at the end of the cycle
- production of concatenated or hollow objects without welding
- no support required in printing
- Mass customization
E.E: In what types of projects do clients use your products / solutions?
F.D.F: Through Legor 3D Metal Jet Printing Service, clients can use Binder Jet technology for a variety of projects across different industries. Some common types of projects include jewelry manufacturing, as well as fashion accessories manufacturing – designers and brands in the fashion industry, for example, leverage this technology to create objects that are difficult to create with the standard and most common technologies. But the 3D Metal Jet Printing Service can be useful also for industrial components production: manufacturers in various industries, such as automotive, aerospace, and electronics, use 3D Metal Jet Printing to produce complex and durable components.
E.E: How important is innovation / R&D in your field?
F.D.F: In Legor we take innovation as one of our strategic drivers: it leads us to always evolve and explore new horizons at the production level. We constantly look for cutting-edge ideas, thanks to our R&D laboratories, which are involved in developing new solutions in terms of alloys and galvanic solutions, as well as the 3D Metal Hub and its experiments in 3D printing technology and applications. In industries such as high-end jewelry and fashion accessories staying ahead of the competition is crucial and innovation is fundamental. These two industries, in fact, are highly competitive, with numerous brands vying for customers attention and many companies with different sizes and specializations. In this case innovation can help us differentiate from other players. In addition to this, we need to remember that consumers, and government regulations, are increasingly demanding sustainable business practices, which means there is growing pressure to introduce innovations in order to reduce the environmental impact of production processes. As Legor we have always an eye on these issues and work towards sustainable goals, for example through responsible sourcing for our metals or by pushing the innovation of 3D Metal Binder Jet Technology, which ensures zero waste and recycling of metal scraps in production.
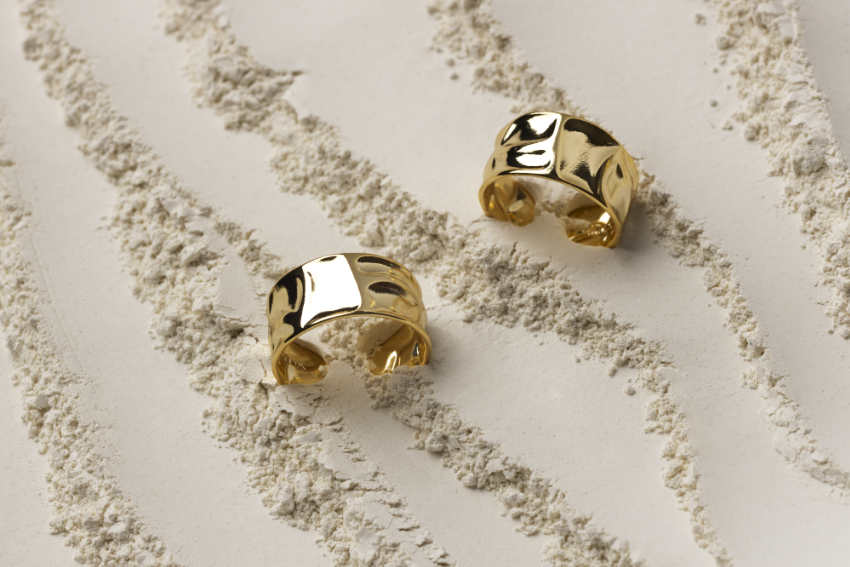
E.E: How do your products /solutions increase profitability for users?
F.D.F: By using Legor products, businesses can enhance the quality of their end products offered to their clients. However, what makes a big difference is the service we provide to our customers: we do not just sell the product; we are close to our customers and assist them with any doubts that may arise while using our products, thus limiting technical issues or quality problems in the final yield of products. With 40% of the world’s jewelry produced with our alloys, and about 14% of the fashion accessories treated with Legor’s plating solutions, it is essential to have technical and sales branches in different countries around the world to thus ensure proximity service where our products are most in demand. Furthermore, Legor understands the diverse needs of its customers and offers customizable solutions, so that customers can tailor products to meet specific requirements.
E.E: How can clients sustainably use your products / solutions?
F.D.F: Clients are encouraged to utilize Legor products efficiently, minimize waste, and optimize resources. Environmentally friendly formulations promote low-toxicity chemicals and water-based solutions, diminishing the footprint of clients’ operations. Sustainable sourcing ensures materials coming from ethical and recycled sources, backed by certifications and transparency. Collaboration and education with clients on sustainable practices are crucial, as well as continuous innovation that drives the development of greener alternatives and technologies.
E.E: How is AI affecting your field of activity?
F.D.F: As part of our strategic approach to innovation, we are embarking on the integration of AI technologies into our existing systems, starting with our Customer Relationship Management (CRM) system in order to better understand and interact with our customers’ needs and solve any problems more efficiently.
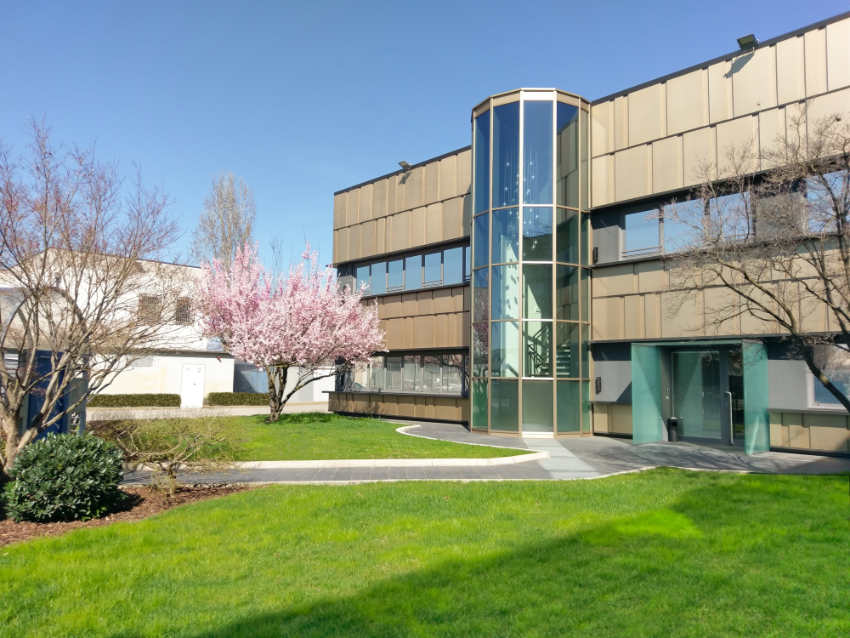
E.E: How do you see the future in your field?
F.D.F: The trend of tomorrow is linked to responsible supply, and we are already seriously working on it, primarly through the sourcing of recycled metals instead of raw metals for mining. Thinking about the Legor 3D Metal Hub, as mentioned above, we offer customers the opportunity to experiment and produce objects using the Binder Jet 3D Metal Printing technology, an alternative method to traditional casting. This is our way of promoting the sustainability of production processes even further.
E.E: What are the business plans for 2024?
F.D.F: One of our most significant challenges is the goal to become climate positive by 2030. We are actively working towards not just reducing, but completely neutralizing our environmental impact. This involves a steadfast commitment to introducing products and processes designed to safeguard both the health of operators/users and the environment. By prioritizing these initiatives, we are also championing innovation within our industry, aiming to set new standards for environmental stewardship and operational safety. Our approach is a testament to our core values of responsibility, sustainability, and care for our clients, underpinned by our expertise in precious metal science and a dedication to innovation.