When you’re looking to buy something new or want to make a major investment, do you ever wonder what’s behind the price of what you’re buying? It’s not easy. We often consider only the purely economic value, which can sometimes act as the first significant obstacle to making a purchase. But if you slightly expand the aspects to consider you’ll see that behind the price label lies something that’s far more important to take into account: time.
Assessing the total long-term cost of the good or service you’re buying is an essential step in making informed, strategic purchasing choices, an assessment that’s not limited to the initial cost but rather incorporates all associated costs over the entire life of the asset, providing a clear, complete view of all economic implications of the investment.
This approach, known as Total Cost of Ownership (TCO), offers a complete perspective of the real costs over time and should be your main focus when making informed purchasing decisions, especially when contemplating the choice of converting your industrial vehicles from endothermic to electric, or if already electric, from lead to lithium.
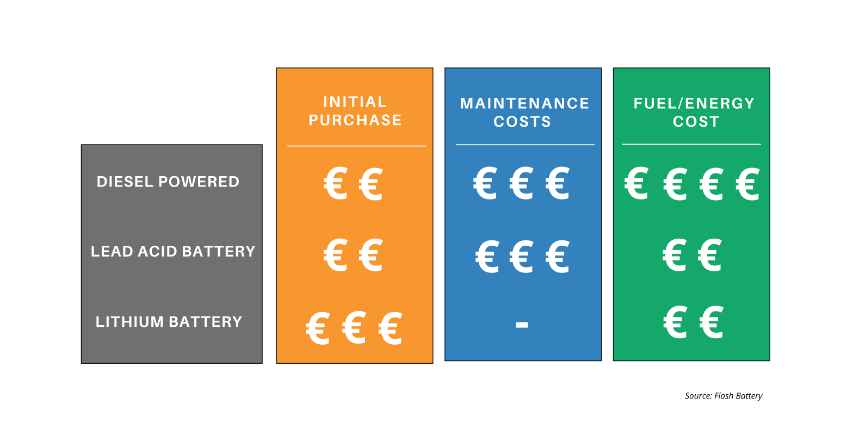
The adoption of lithium batteries is an integral part of the transition to more sustainable technologies, which is necessary not only to comply with the new environmental regulations imposed by the European Green Deal, but also to reduce your own environmental footprint by increasing the performance and lifetime of your vehicles.
At present, however, the purchase cost of an electrified vehicle with a lithium battery represents the main price differential compared to a vehicle with an internal combustion engine or lead-acid battery. OEMs and manufacturers interested in going down the road of lithium electrification will therefore have to keep in mind the strategic importance of TCO, which will help them avoid solutions that are only apparently advantageous, by carefully evaluating various fixed and variable costs such as maintenance costs, energy and refuelling costs, and the impact of tax benefits related to electric conversion, all of which can have a profound effect on the overall price of this investment.
Flash Battery, an Italian company specialising for over 12 years in the design and production of customised lithium batteries for the machinery and industrial vehicle sector, carried out a comparative study on the total cost of ownership of an industrial tractor powered by diesel, lead-acid batteries and lithium batteries. The analysis was performed over ten years of use, taking into account three essential factors for comparing the overall TCO of a vehicle, namely the purchase cost, maintenance costs and the energy balance or fuel price. What did we learn?
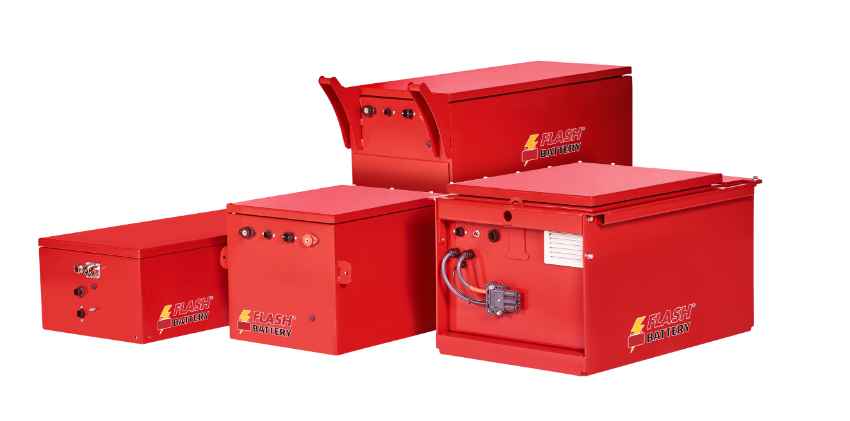
The result clearly demonstrates how high the overall long-term savings are for those who opt for lithium batteries in their vehicles. In fact, the ten-year TCO for a diesel industrial tractor entails a total expenditure of more than 130,000 euros. The same type of vehicle with a lead-acid battery would save more than half that amount, dropping to 47,680 euros if the battery chosen is lithium.
Indeed, while it’s true that the initial investment for a vehicle with a lithium battery is higher, this is clearly recouped over ten years.
For example, when considering maintenance costs the absence of an endothermic engine results in significantly lower running costs compared to combustion vehicles, with the result that components and moving parts subject to wear and tear need to be replaced less frequently. Moreover, there’s a significant difference between the routine maintenance costs of lead-acid batteries and those of their lithium counterparts. With the former, water refilling and maintenance of the filling circuit must be carried out periodically, not to mention cleaning oxidation off of elements and terminals. And that’s not all. Other costs to be borne by the manufacturer include those required for the facilities dedicated to recharging lead-acid batteries if they’re used indoors, those for the extraction of the gases emitted, which must be removed from the charging area and disposed of with aspiration and ventilation systems, and also those for the water demineralisation system, which is essential for topping up the batteries. According to the analysis conducted by Flash Battery, over ten years the maintenance cost of an electric industrial tractor with lithium batteries is practically zero (around 100 euros), while that of an electrified lead-acid vehicle exceeds 20,000 euros.
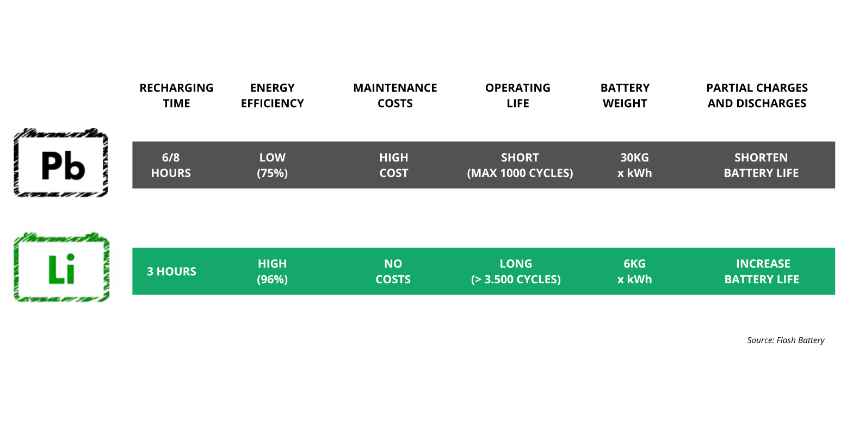
But it’s not just a question of maintenance! Today, lead-acid batteries are considered to be an obsolete technology with several limitations: they have a service life about four times shorter than lithium batteries (1,000 recharge cycles compared to more than 3,500, or even more than 4,000 if managed by Flash Battery’s advanced electronics), resulting in a diminishing capacity to deliver energy over time, requiring more frequent replacement. Moreover, the energy efficiency is significantly lower: about 75% compared to 96% for lithium batteries. Charging times are also slower and can take six to eight hours, while lithium batteries accept partial and quick charges, making it possible to recharge several times during the day. Another major disadvantage of lead-acid batteries is that they have to be replaced and charged after about eight hours of operation, which means that a second battery has to be installed in the vehicle. If you also consider the fact that lead-acid batteries are heavier and bulkier, with their replacement being time-consuming and involving safety risks for operators, it’s clear that electrifying your vehicle with lithium batteries is a financially smart choice.
Furthermore, when used with an intelligent management system such as Flash Battery’s proprietary BMS, the Flash Balancing System, lithium batteries are able to improve the overall efficiency of the vehicle, guaranteeing short, predictable charge times, with a balancing time of less than 30 minutes and full charge in just 2 hours, real-time monitoring of all battery parameters, efficient thermal management and a long service life.
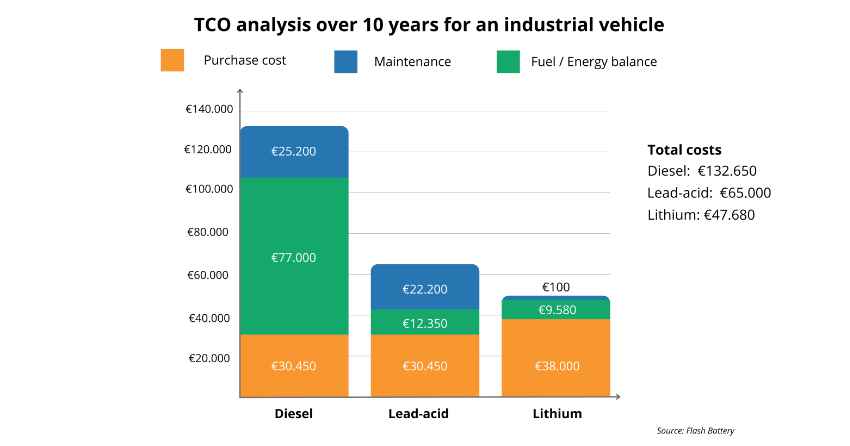
The TCO analysis performed by the Italian battery manufacturer also took into account the energy balance parameter, or fuel costs, in the case of a diesel-powered industrial tractor. It became very clear that electricity is now considered cheaper than diesel for more than one reason. First of all, the energy efficiency of electric vehicles is higher than that of internal combustion vehicles. The “price” factor must also be taken into account: the price of electricity tends to be more stable and less volatile than that of oil and oil derivatives, as well as being less subject to fluctuations in raw material prices than fossil fuels. While this specific TCO indicator shows a cost of around 77,000 euros for a diesel-powered industrial tractor, to power a lead-acid battery it drops to 12,350 euros, decreasing even further to 9,580 euros if the battery is lithium.
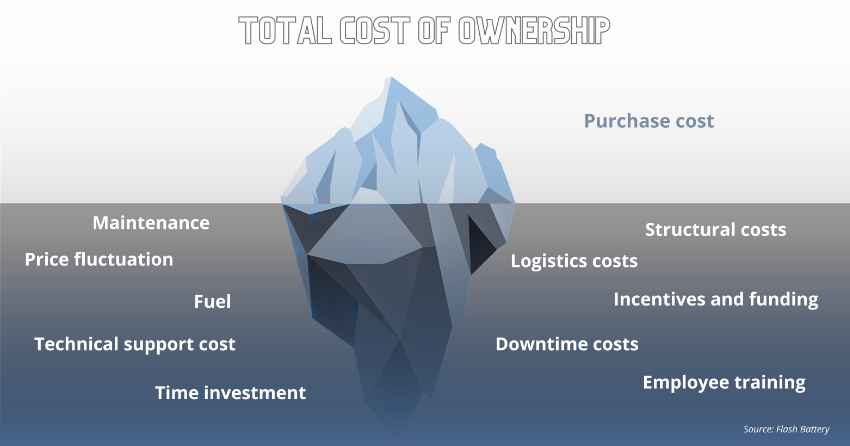
The Total Cost of Ownership calculation must therefore be a key lever for vehicle manufacturers to fully understand the benefits of switching to electric in the long run. The initial purchase price alone does not offer a true understanding of the overall investment. Choosing to electrify your fleets with lithium batteries not only makes sense financially, but also meets new European regulations that require a drastic reduction of polluting emissions, moving towards a lower environmental impact and greater sustainability.