Companies in the automotive and general industrial sectors are currently under massive cost pressures: In a challenging environment, they must increase the efficiency of their production operations, reduce costs, and simultaneously adhere to high quality standards. Schreiner ProTech (SPT), a business unit of Schreiner Group, supports its customers with smart marking solutions, functional films, and RFID technology in optimizing workflows and tapping into hidden savings potential.
A conversation based on field experience with Markus Loris, Product Manager at Schreiner Group.
What typical, cost-related challenges are your customers facing?
Markus Loris: One of the greatest challenges, no doubt, is material costs. In times of rising raw material prices, companies are obviously intensifying their efforts of identifying opportunities for optimizing material consumption and reducing waste. Another central issue is operating costs that are driven up by high energy costs. Companies in the automotive and general industrial sectors are frequently faced with the decision of either choosing a low-cost solution or investing in a higher-quality alternative that perfectly fits into their value creation processes. Short-term savings can be enticing in that regard but a look at Total Cost of Ownership (TCO) shows that the purchasing price accounts for only part of the costs that a component causes across the entire process chain. These challenges are nothing new but we consistently consider them in our customized solutions.
Can you name a specific example of how you’ve enhanced a customer’s efficiency with a product or solution?
M.L: Our so-called Film-Based Cover (FBC) is a case in point. With the FBC, we’ve developed a film-based housing closure. Currently, most plastic component housings are closed by means of injection-molded covers. But those covers entail high tooling costs—you see, that takes us back to costs!—and simply require a certain space during transportation, warehousing, and in installed condition. The trend–especially in the automotive industry—is clearly pointing in the direction of ‘smaller, lighter, more efficient.’ That’s exactly where our solution engages. In our solution, a robust film is precision-cut to size, delivered on rolls, and subsequently connected with the housing by means of laser welding permanently and reliably. This unique film-based closure is light-weight, flat, and resists chemical, mechanical, and thermal loads. Actually, though, savings potential was the focus.
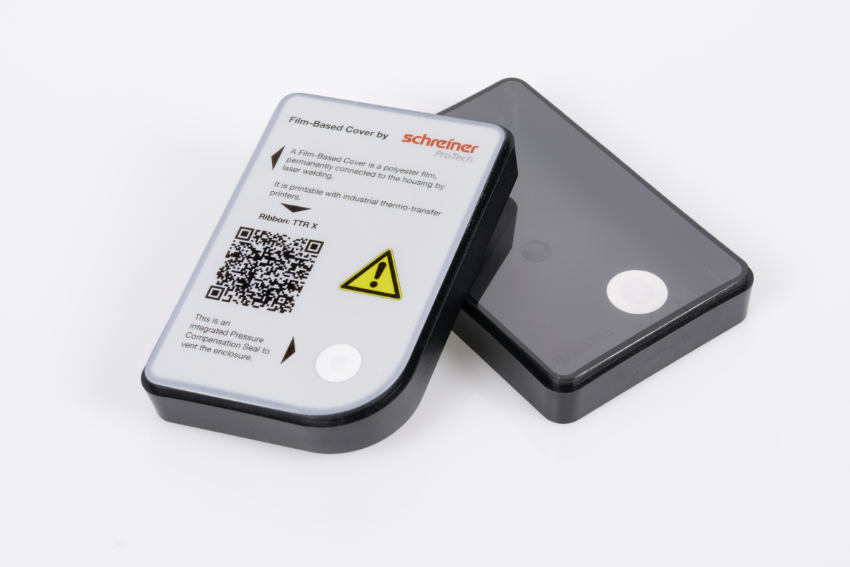
Exactly, so could you please briefly explain what added value the product offers in terms of cost savings?
M.L: Sure, it starts as early as in the development. The production of an injection-molded cover requires relatively expensive tools causing high costs not just initially but that need to be modified or newly made in case of design changes. The FBC eliminates these tooling costs almost completely. Here, the costs can be reduced by at least a factor of 10!
Production costs are another factor: Thin-walled injection-molded covers can lead to manufacturing or leakage issues. By contrast, the Film-Based Cover—cut to the right size—is delivered on rolls and processed semi- or fully automatically, resulting in simpler parts handling and more efficient production.
Now, let’s talk about weight: Film-based solutions are lighter and flatter than injection-molded parts, which significantly simplifies transportation and storage. In addition, the material savings reduce the carbon footprint—an aspect that’s becoming increasingly important for many companies.
Particularly in the automotive industry weight is a crucial factor—especially for electrification, where every gram counts. And every gram less helps increase the range of electric vehicles or reduce the fuel consumption of conventional vehicles. What does that mean in this case in terms of specific numbers? The Film-Based Cover is up to 90 percent lighter than a conventional injection-molded cover. In vehicle engineering, it’s exactly these optimizations in many minor areas that, in total, achieve major effects. Consequently, the FBC is an attractive alternative especially for OEMs that examine every component for light-weight potential.
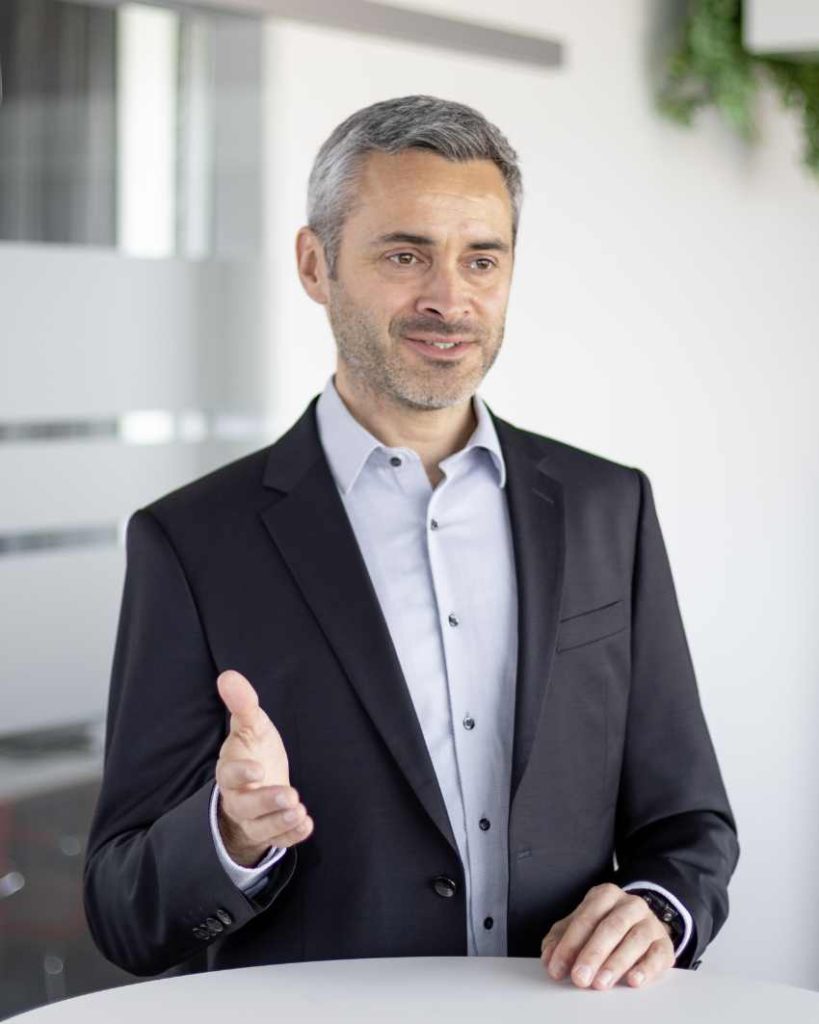
However, the film plays a crucial role in another regard: Modern vehicles contain a lot of sensors—be it for advanced driver assistance systems, autonomous driving, comfort functions, or vehicle communications. Conventional injection-molded covers often impair the transmission of radar, ultrasonic, or radio signals. The Film-Based Cover consists of a thin, highly transparent film enabling unobstructed sensor signal transmission. That leads to greater precision of readings resulting in better performance of the systems. Especially for manufacturers that are in the process of developing new sensor platforms that can be a decisive advantage.
But in my view one of the greatest strengths of the film-based solution is its multi-functionality. For instance, the FBC can include an integrated pressure compensation seal (PCS) that equalizes pressure fluctuations while protecting the interior of the housing against dust and liquids. This means that no separate PCS needs to be installed, which saves space as well as installation effort. Thermal transfer printing (TTR) of the FBC is possible too. That’s particularly interesting for components that must be provided with an individual serial number or a QR code because it eliminates the need for a separate process step to attach a nameplate which, in turn, further simplifies production processes.
I’ll briefly summarize again what switching to this housing solution specifically means for customers: They receive one flat component where they previously needed to use and install up to four individual components: a housing cover, nameplate, informational plate, and pressure compensation seal. That reduces the space required in production and capital expenditures for machines, shortens through-put time, and minimizes administrative requirements. That’s a clear reduction of complexity with truly added value.
You’ve already addressed the subject of “hidden costs”: How do you ensure that your products offer long-term benefits and won’t turn into cost traps?
M.L: Schreiner Group is a value-oriented family-owned company in which quality plays a central role. That’s our basic mindset reflected exactly in our products as well. On the one hand, we often develop our products and solutions in very close coordination with our customers and their specific requirements, which ensures that tailored products prevent wrong uses or unnecessary costs that might, for instance, be incurred due to unsuitable standard solutions.
On the other hand, we emphasize the utilization of high-grade materials, precise manufacturing processes, and field-focused tests. We have our own Research and Development Department and in-house testing facilities in which we can check the customer’s requirements to ensure the product’s desired lifetime and stability of use. Using that approach, we avoid hidden costs and ensure that our customers are going to benefit from our solutions in the long run.
The good thing is that with us you get everything from a one-stop shop—from the initial idea to mass production, so you have full transparency right from the beginning. And in case that something should come up for a change you won’t end up in some external call center but are going to be dealing with real contact persons that are there to support you, and our customers appreciate that.
What advice would you provide to companies seeking to maximize their efficiency while minimizing their operating costs?
M.L: I think that can’t be tied to a single aspect but must always be a combination of several approaches. Take automation for example: A high level of automation reduces manual mistakes and increases productivity. Digital workflows and systematic use of Industry 4.0 technologies such as smart RFID solutions enable efficient logistics control that optimizes inventories and reduces shipping routes.
Then take the subject of material optimization: By using innovative marking and protection solutions companies can not only simplify their processes but also reduce their production costs. The utilization of smart pressure compensation seals, for instance, can prolong the lifecycle of components and if we add the aspect of sustainability then the systematic use of durable materials and recyclable components can minimize resource consumption and positively affect the carbon footprint. So, there are many levers that can be used without sacrificing quality or competitiveness. The most important thing in my view is that companies invest in products and solutions that aren’t focused on short-term cost savings but on long-term and sustainable efficiency gains.
German version:
In der Automobil- und Technischen Industrie stehen Unternehmen aktuell unter einem enormen Kostendruck: Sie müssen in einem herausfordernden Umfeld gleichzeitig die Effizienz ihrer Produktion steigern, Kosten reduzieren und dabei hohe Qualitätsstandards einhalten. Schreiner ProTech (SPT), ein Geschäftsbereich der Schreiner Group, unterstützt seine Kunden mit intelligenten Kennzeichnungs-lösungen, funktionalen Folien und RFID-Technologie dabei, Abläufe zu optimieren und versteckte Einsparpotenziale zu heben.
Ein Gespräch aus der Praxis mit Produktmanager Markus Loris.
Herr Loris, vor welchen typischen, kostenbezogenen Herausforderungen stehen Ihre Kunden?
Eine der größten Herausforderungen sind sicherlich die Materialkosten. In Zeiten steigender Rohstoffpreise suchen Unternehmen natürlich verstärkt nach Möglichkeiten, den Materialeinsatz zu optimieren und Abfälle zu reduzieren. Ein weiteres zentrales Problem bilden die Betriebskosten, die durch hohe Energiekosten in die Höhe getrieben werden. In der Automobil- und Technischen Industrie stehen Unternehmen ja häufig vor der Entscheidung, ob die preisgünstige Lösung wählen oder in eine hochwertigere Alternative investieren, die sich bestens in die Wertschöpfungsprozesse einfügt. Kurzfristige Einsparungen können dabei verlockend sein, doch eine Betrachtung der Total Cost of Ownership (TCO) zeigt, dass der Anschaffungspreis nur einen Teil der Kosten darstellt, die eine Komponente über die gesamte Prozesskette hinweg verursacht. Diese Herausforderungen sind nicht neu, aber wir berücksichtigen sie konsequent bei unseren kundenindividuellen Lösungen.
Können Sie denn ein konkretes Beispiel nennen, wie Sie mit einem Produkt oder einer Lösung die Effizienz eines Kunden verbessert haben?
Ein gutes Beispiel ist das sogenannte Film-Based Cover, kurz FBC. Wir haben mit dem FBC eine folienbasierten Gehäuseverschluss entwickelt. Aktuell werden die meisten Bauteilgehäuse aus Kunststoff mit Spritzgussdeckeln verschlossen. Diese sind jedoch mit hohen Werkzeugkosten vebunden – sehen Sie: das sind wir wieder bei den Kosten! – und benötigen schlicht und ergreifend einen gewissen Platz beim Transport, in der Lagerung und im verbauten Zustand. Der Trend – insbesondere in der Automobilindustrie – geht klar in Richtung ‚kleiner, leichter, effizienter‘. Genau hier setzt unsere Lösung an. Bei unserer Lösung wird eine stabile Folie passgenau gestanzt, auf Rolle geliefert und dann per Laserschweißen dauerhaft und sicher mit dem Gehäuse verbunden. Dieser einzigartige Folienverschluss ist leicht, flach und hält chemischer, mechanischer und thermischer Belastung stand. Aber es ging ja eigentlich ums Einsparpotenzial.
Genau, können Sie daher bitte einmal kurz erklären, welchen Mehrwert das Produkt hinsichtlich der Kosteneinsparungen bietet?
Gerne. Das beginnt bereits in der Entwicklung. Die Herstellung eines Spritzgussdeckels erfordert recht teure Werkzeuge, die nicht nur initial hohe Kosten verursachen, sondern bei Designänderungen immer wieder angepasst oder neu gefertigt werden müssen. Beim FBC entfallen diese Werkzeugkosten fast vollständig. Hier lassen sich die Kosten um mindestens den Faktor 10 reduzieren!
Ein weiterer Faktor sind die Produktionskosten: Dünnwandige Spritzgussdeckel können zu Fertigungs- oder Dichtigkeitsproblemen führen. Das Film-Based Cover hingegen wird – im passenden Formt gestanzt – auf Rolle geliefert und in einem halb- oder vollautomatischen Prozess verarbeitet. Das Ergebnis: einfacheres Teilehandling und eine effizientere Produktion.
Kommen wir dann zum Gewicht: Folienlösungen sind leichter und flacher als Spritzgussteile, was den Transport und die Lagerung erheblich vereinfacht. Die Materialeinsparung reduziert zudem den CO₂-Fußabdruck – ein Aspekt, der für viele Unternehmen zunehmend an Bedeutung gewinnt.
Gerade in der Automobilindustrie ist das Gewicht ein entscheidender Faktor – insbesondere für die Elektrifizierung. Hier zählt jedes Gramm. Und jedes Gramm weniger trägt dazu bei, die Reichweite von E-Fahrzeugen zu erhöhen oder den Kraftstoffverbrauch konventioneller Fahrzeuge zu senken. Was bedeutet das in diesem Fall konkret in Zahlen? Das Film-Based Cover ist bis zu 90 Prozent leichter als ein herkömmlicher Spritzgussdeckel. Im Fahrzeugbau sind es genau diese Optimierungen an vielen kleinen Stellen, die in Summe große Effekte erzielen. Gerade für OEMs, die jedes Bauteil auf Leichtbaupotenziale prüfen, ist das FBC daher eine attraktive Alternative.
Die Folie spielt aber auch noch an anderer Stelle eine entscheidende Rolle: moderne Fahrzeuge beinhalten viel Sensorik – sei es für Fahrerassistenzsysteme, autonomes Fahren, Komfortfunktionen oder Fahrzeugkommunikation. Herkömmliche Spritzgussdeckel beeinträchtigen oft die Übertragung von Radar-, Ultraschall- oder Funksignalen. Das Film-Based Cover besteht aus einer dünnen, hochtransparenten Folie, die Sensoren eine ungehinderte Signalübertragung ermöglicht. Das führt zu präziseren Messwerten und damit zu einer besseren Funktion der Systeme. Gerade für Hersteller, die in der Entwicklung neuer Sensorplattformen stehen, kann das ein entscheidender Vorteil sein.
Eine der größten Stärken der Folienlösung ist aber meiner Meinung nach ihre Multifunktionalität. So kann das FBC beispielsweise ein integriertes Druckausgleichselement (DAE) enthalten, das Druckschwankungen ausgleicht und dennoch das Gehäuseinnere vor Staub und Flüssigkeiten schützt. Das bedeutet, dass kein separates DAE verbaut werden muss, was sowohl Platz als auch Montageaufwand spart. Auch eine Thermotransfer-Beschriftung (TTR) des FBC ist möglich. Das ist besonders für Bauteile interessant, die mit einer individuellen Seriennummer oder einem QR-Code versehen werden müssen, denn dadurch entfällt der separate Arbeitsschritt zur Anbringung eines Typenschilds, was die Produktionsprozesse weiter vereinfacht.
Ich fasse noch einmal kurz zusammen, was der Umstieg auf diese Gehäuselösung für den Kunden konkret bedeutet: Er bekommt ein flaches Bauteil, wo er früher bis zu vier einzelne Komponenten – Gehäusedeckel, Typenschild, Hinweisschild und Druckausgleichselement – einsetzen und montieren musste. Das reduziert den Platzbedarf in der Produktion, senkt Investitionen in Maschinen, verkürzt die Durchlaufzeit und minimiert den Verwaltungsaufwand. Eine deutliche Komplexitätsreduzierung mit echtem Mehrwert.
Jetzt hatten Sie schon das Thema „versteckte Kosten“ angesprochen: Wie stellen Sie denn sicher, dass Ihre Produkte einen langfristigen Nutzen bieten und damit nicht zur Kostenfalle werden?
Die Schreiner Group ist ein werteorientiertes Familienunternehmen, in dem Qualität eine zentrale Rolle spielt. Das ist eine Grundeinstellung bei uns und genau das spiegelt sich auch in unseren Produkten wider.
Zum einen entwickeln wir unsere Produkte und Lösungen oft in sehr enger Abstimmung mit den Kunden und deren spezifischen Anforderungen. Das sorgt dafür, dass maßgeschneiderte Produkte Fehlanwendungen oder unnötige Kosten verhindern, die beispielsweise durch unpassende Standardlösungen entstehen könnten.
Dann setzen wir auf hochwertige Materialien, präzise Fertigungsprozesse und praxisnahe Tests. Wir haben eine eigene Forschungs-und Entwicklungsabteilung und hauseigene Prüfmöglichkeiten, bei denen wir die Anforderungen des Kunden abprüfen können, um die gewünschte Lebensdauer des Produkts und einen stabilen Einsatz sicherzustellen. Durch diesen Ansatz vermeiden wir versteckte Kosten und stellen sicher, dass unsere Kunden langfristig von unseren Lösungen profitieren.
Das Gute ist, Sie erhalten bei uns alles aus einer Hand – von der ersten Idee bis zur Serienproduktion. Sie haben daher volle Transparenz, von Anfang an.
Und sollte wirklich einmal etwas sein, landen Sie nicht in irgendeinem auswärtigen Callcenter, sondern Sie haben echte Ansprechpartner, die für Sie da sind und das wissen unsere Kunden zu schätzen.
Welchen Rat würden Sie denn Unternehmen geben, die ihre Effizienz maximieren und gleichzeitig die Betriebskosten niedrig halten möchten?
Ich denke, das kann man nicht an einem eizelnen Aspekt festmachen, sondern es muss immer eine Kombination aus mehreren Ansatzpunkten sein. Nehmen wir die Automatisierung: Ein hoher Automatisierungsgrad reduziert manuelle Fehler und steigert die Produktivität. Digitale Workflows und der gezielte Einsatz von Industrie 4.0-Technologien wie smarte RFID-Lösungen ermöglichen eine effiziente Logistiksteuerung, die Bestände optimiert und Transportwege reduziert.
Dann das Thema Materialoptimierung: Durch den Einsatz innovativer Kennzeichnungs- und Schutzlösungen können Unternehmen nicht nur ihre Prozesse vereinfachen, sondern auch ihre Produktionskosten senken. Beispielsweise lässt sich durch intelligente Druckausgleichselemente die Lebensdauer von Bauteilen verlängern. Und wenn wir jetzt noch die Nachhaltigkeit ins Spiel bringen, kann der gezielte Einsatz langlebiger Materialien und recyclingfähiger Komponenten den Ressourceneinsatz minimieren und den CO2-Fußabdruck positiv beeinflussen. Es gibt also viele Hebel, die sie nutzen können, ohne Qualität oder Wettbewerbsfähigkeit einzubüßen. Das Wichtigste ist meines Erachtens, dass Unternehmen in Produkte und Lösungen investieren, bei denen es nicht um kurzfristige Kosteneinsparungen geht, sondern um langfristige und nachhaltige Effizienzgewinne.
Further info: