Nitrex is a global leader in surface treatment, leveraging over 40 years of expertise and a vast portfolio of 4000+ processes. Their mission is to provide optimal solutions to their valued customers through the network of 15 sites worldwide.
Interview with Jason Orosz, President of Global Heat Treating Services at Nitrex
Easy Engineering: A brief description of the company and its activities.
Jason Orosz: We have three distinct lines of business where we integrate artificial intelligence and cutting-edge technologies to enhance our services and solutions.
The first line comprises our Advanced Heat Treating Centers, where we offer premium processes such as NITREG® gas nitriding, NITREG®-C ferritic nitrocarburizing, ONC® post-oxidation black finish, NITREG®-S nitriding of stainless steels, NANO-S™ surface hardening of stainless steels, as well as low-pressure carburizing, vacuum carburizing, and gas carburizing treatments.
The second line focuses on the manufacturing of nitriding and vacuum turnkey equipment, providing our customers with the cutting-edge equipment for their in-house surface treatment needs.
Lastly, our UPC-Marathon division specializes in the development of software and controls, leveraging the latest technologies to optimize and streamline surface treatment processes.
Through these three lines of business, we harness the power of artificial intelligence and cutting-edge technologies to deliver exceptional services and solutions to our valued customers.
With a strong presence in over 60 countries and production facilities in multiple locations including France, Germany, Poland, Canada, China, Mexico, and the United States, we bring unparalleled expertise and an innovative mindset to our customers. Our commitment is to help you achieve higher tolerances, exceed industry standards, and drive profitability. Supported by our dedicated R&D department and knowledgeable experts, we strive to establish long-term partnerships with our customers, supporting their journey towards excellence and success in surface treatment.
E.E: What are the main areas of activity of the company?
J.O: Nitrex has established itself as a renowned expert in the field of premium nitriding and nitrocarburizing for over four decades. With a strong focus on delivering turnkey solutions that consistently deliver high-quality results, Nitrex has become a trusted partner for customers with unique requirements. Our expertise in nitriding and nitrocaburizing allows us to customize our solutions, enhancing wear resistance, increasing surface hardness, and improving the fatigue life of engineered metal parts.
But our expertise doesn’t stop there. Over the years, Nitrex has expanded its capabilities to encompass vacuum turnkey furnaces, heat treat services centers, process control instrumentation and software solutions. This diversification has enabled us to address the evolving needs of industries such as aerospace, automotive, industrial, and renewable energy.
Our vacuum turnkey furnaces, backed by the recent acquisition of American furnace manufacturer G-M Enterprises, offer clean heat treatment technologies that enhance critical components for a wide range of industrial products. By leveraging vacuum technology, we improve the quality, durability, and reliability of the treated products. Our R&D efforts continue year-round, ensuring that we stay at the forefront of technological advancements in the field.
Operating Heat Treat Services (HTS) centers across the globe, Nitrex provides comprehensive heat treatment services. With a portfolio of over 30 heat treating processes, our dedicated team of metallurgists and technical advisors address the most challenging application requirements. Our HTS centers, located in Canada, the United States, Mexico, Poland, Italy, and China, allow us to serve customers globally, ensuring efficiency, reliability, and sustainability.
In addition to our heat treatment expertise, Nitrex’s instrumentation and software division, known as UPC-Marathon, provides high-end engineered instrumentation and control solutions for the surface treatment industry. We offer a range of cutting-edge products, including sensors, flow and process controls, gas generators, and turnkey furnace control upgrade solutions. These solutions enhance the capabilities and prolong the lifespan of surface treatment furnaces, ensuring optimal performance and efficiency.
At Nitrex, our commitment to continuous innovation and customer satisfaction drives us to develop advanced solutions that meet the ever-increasing demands of the industry. We pride ourselves on our ability to deliver consistent, high-quality results while remaining at the forefront of technological advancements. With our comprehensive range of services, global presence, and expertise, Nitrex is the preferred choice for companies seeking surface treatment solutions that enhance their products’ performance, durability, and cost-efficiency.
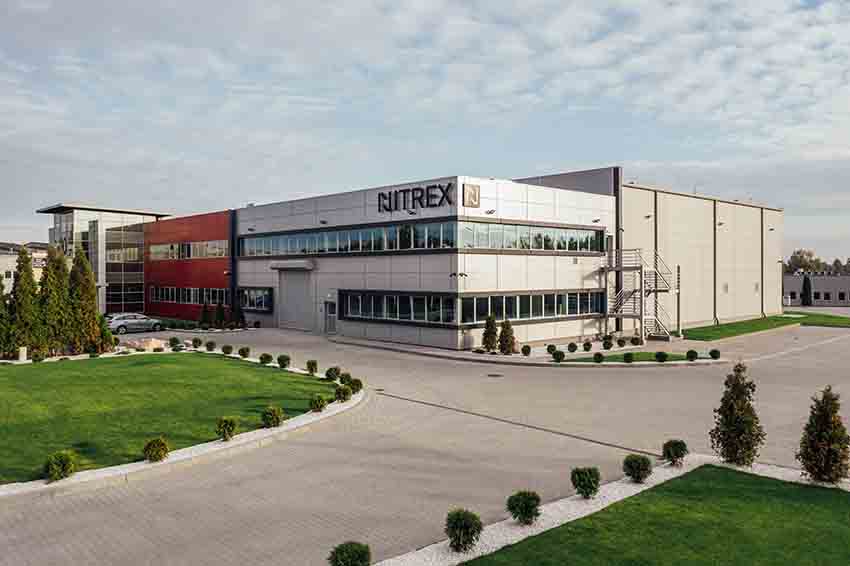
E.E: What’s the news about new products?
J.O: In 2023, Nitrex introduced several exciting new products that revolutionize the industry and offer enhanced solutions for their customers.
Nitrex launched QMULUS, a cutting-edge AI and machine learning software. QMULUS is a holistic Industrial Internet of Things (IIoT) solution designed to digitize the heat treat shop floor. It enables businesses to manage production sites remotely, providing real-time visibility and control over heat-treating operations. With its AI and machine learning capabilities, QMULUS offers unique insights and optimization of processes, enhancing efficiency like never before.
With new emission laws emphasizing the importance of brake wear particulate emissions, Nitrex developed enhanced nitrocarburizing technology for brake discs. This technology significantly reduces corrosion, resulting in lower brake dust particles. Nitrex’s Smart ONC® technology combines nitrocarburizing with in-process post-oxidation, improving the corrosion and wear properties of brake rotors in a cost-effective manner. Treated brake rotors minimize brake dust and particulate matter emissions, benefiting both the industry and the environment.
Nitrex expanded its manufacturing facility in Poland to better serve European and Asian customers. The facility now offers the highly sought-after HVF horizontal vacuum furnace. Nitrex plans to further expand its operations by introducing other furnace models such as the QuantumQuench™ with directional cooling, the 3Q™ with a movable hot-zone vertical furnace, and the SAR/VPA series for vapor-phase aluminide coating. As a result of this strategic expansion, Nitrex is now proud to announce that its furnaces have obtained CE certification, meeting the rigorous standards required for the EU market. This achievement ensures that Nitrex can cater to a broader range of customers while demonstrating compliance with EU regulations.
Nitrex introduced the innovative solution, EndoFlex S™, which provides customers with a competitive edge. This endothermic generator delivers on-demand endo gas without any waste, resulting in significant energy and gas feedstock savings. One customer, a manufacturer of industrial chains, experienced monthly savings of up to 20% in energy and resource costs by adopting EndoFlex S™.
E.E: What are the ranges of products?
J.O: NITREX’s Heat Treat Services (HTS) division offers a comprehensive portfolio of 30+ heat treating processes to cater to diverse needs. Our range of processes includes NITREG® Gas Nitriding, NITREG®-C Nitrocarburizing (FNC), Low-Pressure Carburizing, and Vacuum Heat Treatment, among others. With our dedicated team of metallurgists and technical advisors, we are well-equipped to address even the most challenging application requirements. We leverage our ever-stronger local market presence, supported by the expertise and resources of our global network, to deliver top-notch solutions.
In meeting the stringent demands of industries like aerospace and defense, automotive, medical, mining, oil and gas, and tooling, we offer an extensive lineup of vacuum furnaces. Our vacuum furnace options encompass horizontal front-loading and bottom-loading models, SAR/VPA series equipped with vapor phase aluminide technology, QuantumQuench®, and 3Q™ series horizontal single-chamber vacuum furnaces. These furnaces are designed to provide the precise and controlled environment necessary for optimal surface treatment processes.
Our Nitriding/Nitrocarburizing furnaces have established a proven track record of reliability and efficiency across various sectors, including aluminum extrusion, automotive, aerospace and defense, general manufacturing, and tooling. Whether your application requires complex processes or simple ones, our Nitriding/Nitrocarburizing furnaces can accommodate both small and large batch sizes. Furthermore, we have developed a continuous line capable of supporting high-volume, fully automated, 24/7 lights-out production.
Complementing our surface treatment solutions, our instrumentation and software division, UPC-Marathon, takes pride in manufacturing the highly regarded WAUKEE™ flow control instruments. These instruments ensure precise and reliable control of atmosphere gases and liquids throughout the treatment process. Additionally, we offer turnkey gas generators, flexible options for combustion process monitoring and control, custom flow control solutions, custom process control solutions, atmosphere analyzers, as well as carbon/oxygen probes for new and retrofit furnaces.
E.E: At what stage is the market where you are currently active?
J.O: The markets in which Nitrex is currently active are characterized by strong investments in advanced surface treatment services and products, as well as companies seeking more sustainable choices. With the increasing focus on enhancing product performance, durability, cost-efficiency, and sustainability, there is a growing market opportunity for Nitrex to provide its expertise in heat treatment services, furnaces, controls, and digitilization.
Specifically, the aerospace, automotive, industrial, and renewable energy markets show a particular openness to innovative technologies and approaches that optimize their manufacturing, production processes, and carbon footprint. These industries are continuously striving to improve their operational capabilities and the overall quality of products. More importantly, they aim to reduce emissions, minimize waste, and conserve resources to meet present and future sustainability goals.
Nitrex’s range of high-performance and greener solutions, coupled with its ability to tailor them to meet specific demands, positions the company favorably in these active markets. This not only creates new opportunities but also allows for greater market expansion.
E.E: What can you tell us about market trends?
J.O: The market trends indicate a shift towards digitalization, sustainability, and supply chain resilience in the manufacturing industry. Companies are leveraging technology, adopting greener practices, and reevaluating their supply chain strategies to stay competitive, reduce costs, and adapt to evolving customer expectations.
Digitalization: The industry is experiencing a notable trend towards digitalization, driven by the need for efficient tracking of parts, reducing costs, and managing the carbon footprint. As senior operators and managers retire, the new generation seeks more digital and social ways of conducting business to increase efficiency. Digital solutions, such as software systems for process optimization, remote monitoring, and real-time data analysis, are becoming increasingly prevalent.
Green Solutions: The industry is witnessing a growing emphasis on greener solutions, influenced by energy market price volatility and government regulations. Many companies are striving to reduce their carbon footprint and adopt environmentally friendly practices. This trend is driven by both economic and regulatory factors, as businesses recognize the benefits of sustainability in terms of cost savings, brand reputation, and meeting consumer expectations.
Supply Chain Resilience: The past few years, including the COVID-19 pandemic and geopolitical tensions, have disrupted global supply chains. As a result, many companies are reevaluating their supply chain strategies. Some are choosing to internalize their processes to have better control and reduce dependence on external suppliers, while others are focusing on localizing their supply chains. This trend aims to enhance resilience, reduce risks, and ensure a more reliable flow of materials and components.
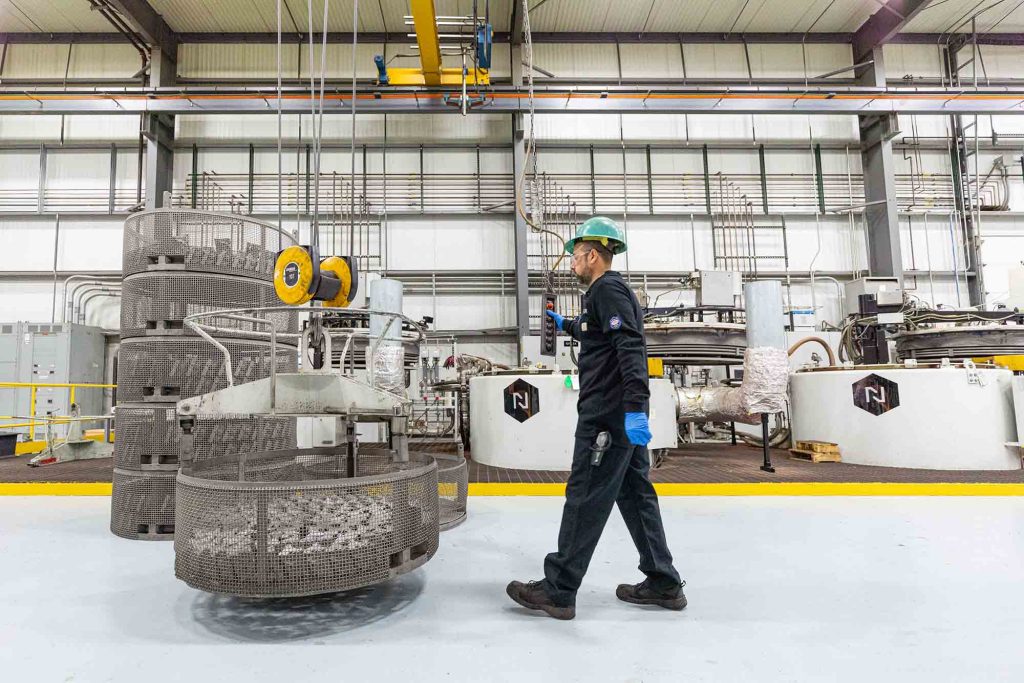
E.E: What are the most innovative products marketed?
J.O: Nitrex takes pride in our pursuit of innovation and continuous improvement. We strive to empower our customers with innovative technologies that not only improve their processes but also align with their environmental sustainability goals. Our focus on innovation can be seen in all our services and solutions, but three of our most innovative products this year are:
QMULUS: One of the most innovative products is QMULUS, an AI and machine learning software solution designed to digitize the heat treat shop floor. By harnessing the power of AI and machine learning, QMULUS enables businesses to optimize and streamline their heat-treating operations, providing real-time visibility, control, and insights into the processes. This transformative software solution has the potential to revolutionize the way surface treatment operations are managed, driving efficiency and enhancing overall productivity.
SMART ONC®: Developed specifically to address the issue of brake wear particulate emissions, SMART ONC® is a breakthrough technology that combines nitrocarburizing with in-process post-oxidation. By improving the corrosion and wear properties of brake rotors, SMART ONC® significantly reduces brake dust and particulate matter emissions. This innovative solution benefits both brake rotor manufacturers, by enabling them to meet higher environmental standards, and drivers, by ensuring high-performance braking systems. Due to its effectiveness and potential environmental benefits, SMART ONC® is also being explored for other industries and applications where corrosion resistance and wear properties are of critical importance.
ENDOFLEX S™: Our endothermic generator delivers on-demand endo gas without any waste. This solution significantly reduces energy and gas feedstock consumption, leading to substantial cost savings and a more sustainable approach to heat treatment processes. By promoting energy and resource efficiency, EndoFlex S™ exemplifies our dedication to reducing the carbon footprint of various industries.
E.E: What estimations do you have for 2023?
J.O: Nitrex’s expectations align with the overall positive trajectory of the global industry. The anticipated gradual global growth indicates that the market is rebounding from the challenges faced in previous years, such as the COVID-19 pandemic and geopolitical tensions. As economies recover and stabilize, there is increased investment in manufacturing, which presents opportunities for Nitrex.
The belief that there are opportunities in new markets suggests that Nitrex is exploring avenues for expansion and diversification. By entering new markets, Nitrex can tap into untapped potential and broaden its customer base. This strategic move allows the company to leverage its expertise and latest products to cater to a wider range of customers and industries.
Additionally, Nitrex’s confidence in its latest products indicates that they have identified specific needs and demands from their main customers. By addressing these requirements with innovative solutions, Nitrex can strengthen its position as a trusted provider and offer added value to its existing customer base.
Overall, Nitrex’s perspective on global growth, opportunities in new markets, and the relevance of its latest products demonstrates a proactive approach to adapt and capitalize on emerging trends. By identifying and meeting customer needs, Nitrex can position itself for continued success and expansion in the industry.