The chair “Production Engineering of E-Mobility Components” (PEM) at RWTH Aachen University stands for forward-looking research and innovation in the field of electromobility. In several research areas, the production processes of electric vehicles and their individual components as well as batteries, their recycling and safety are further developed.
Interview with Professor Achim Kampker, Chair of Production Engineering of E-Mobility Components (PEM) at RWTH Aachen University.
Easy Engineering: A brief description of the organization and its activities.
Achim Kampker: As co-inventor of the ‘StreetScooter’, I had the honor of founding the Chair of Production Engineering of E-Mobility Components (PEM) of RWTH Aachen University back in 2014. Today, our PEM team is conducting research in ten specific groups where we are dedicated to all aspects of the development, production, and recycling of battery systems and their components, as well as fuel cells and the production of the electric powertrain and entire vehicle concepts. Currently, a total of 78 researchers, 35 non-scientific staff and 130 student assistants are employed at three different sites, with our headquarters being located in the German-Dutch industrial park ‘Avantis’. PEM is active in teaching as well as in nationally and internationally funded research projects and in collaboration with renowned industrial partners. Our focus is always on sustainability and cost reduction – with the goal of a seamless ‘Innovation Chain’ from basic research to large-scale production in the immediate vicinity. Thus, PEM provides the breeding ground for partly interconnected spin-offs like ‘PEM Motion’ and mobility products such as ‘Velocity Aachen’.
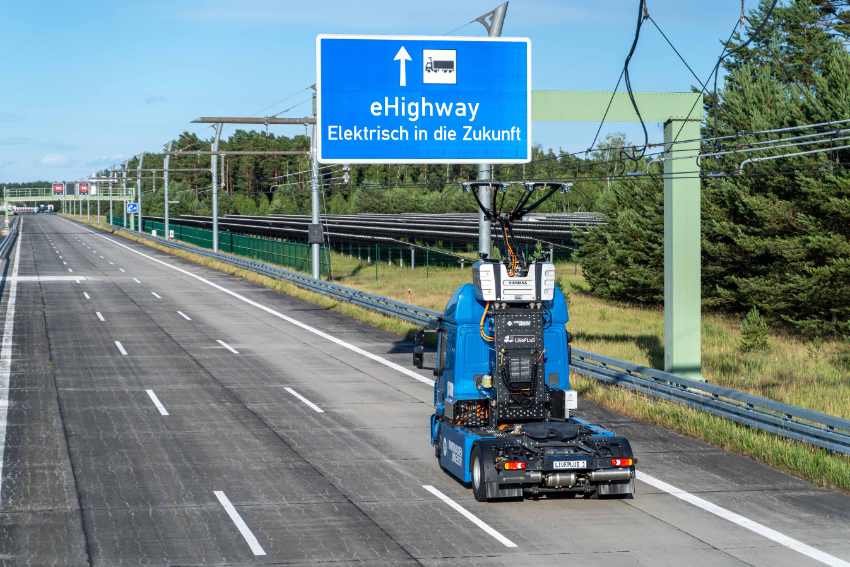
E.E: What are the main areas of activity of the organization?
A.K: In addition to teaching, we are active in numerous research projects, which are usually funded by the state or the federal government and in which we collaborate with other research institutions or with high-ranking industrial partners. In doing so, we address all aspects that play an important role in the production of electric vehicles. For example, we are currently researching the development of stationary energy storage systems consisting of electric vehicle batteries that are no longer powerful enough to operate in e-cars.
In another project, we are researching how the disassembly and recycling of electric vehicle batteries can be fully automated in the future and carried out with the help of artificial intelligence – something that until now has only been done manually, taking a great deal of time. In yet another project, we are looking at a new type of coating process for fuel cells that requires significantly less time and material. We are also currently developing an efficient production process for important electric motor components that is suitable for large-scale production, a robot on wheels that will act as a mobile charging station to supply electric vehicles of various sizes with electricity, and on an electric truck for heavy-duty transport that will run with a customizable powertrain consisting of a battery and a fuel cell.
In a project we have just completed, we have demonstrated the practicality of electric trucks that are essentially powered by a pantograph. According to a study by our institute, which is based on data from 153 logistics centers from the areas of corporate logistics, wholesale and retail as well as parcel services, 90 percent of all travel distances considered in Germany could already be covered electrically with an expansion of just 4,000 kilometers of overhead line and a battery-electric range of 175 kilometers. All of this is just a small sample of our current projects, many of which also deal with new processes for more efficient battery production.
E.E: What’s the news for 2024 about new directions?
A.K: Many of our projects extend into 2024 or further beyond. For the coming year, we therefore already expect to gain some new insights into how the production of batteries, fuel cells, and electric motors can be made much more efficient on an industrial scale – and how the industry can manage to establish a sustainable circular economy for all key components, which will most likely be crucial to the success of electric mobility. We also expect to see further progress in battery research – for example, with a view to the efficiency of electric vehicle batteries, but also concerning possible alternatives to lithium-ion technology.
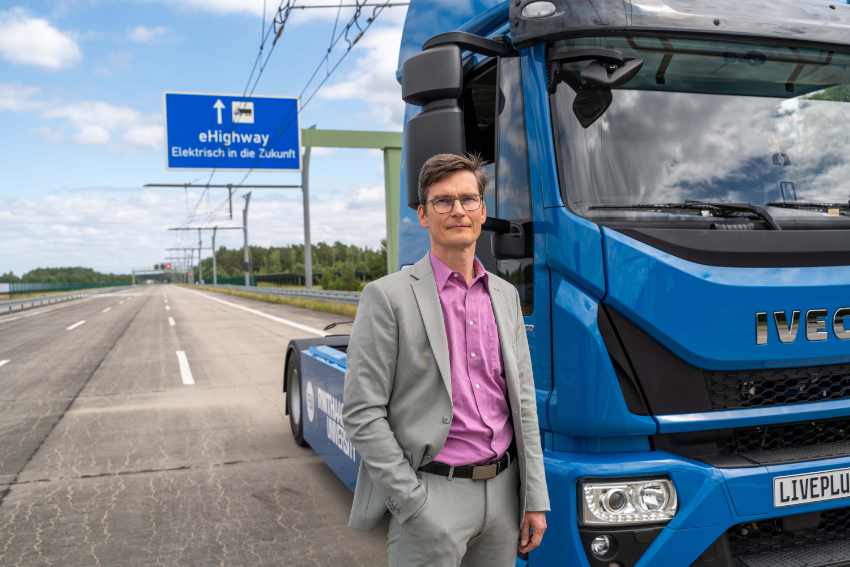
E.E: What can you tell us about market trends?
A.K: Naturally, there are very different developments taking place in industry and research in the three major areas of ‘battery’, ‘fuel cell’ and ‘electric motor’.
In battery production, new processes such as laser drying are gaining importance, which are faster, increase efficiency and improve the battery cells’ quality. Data-based optimization approaches are also coming into play. In cell production, the trend is to use Big Data, machine learning and the Internet of Things to improve production processes in real time. In addition, battery production is increasingly relying on innovative processes such as trajectory mixing or extruder technology to mix materials more homogeneously and efficiently, which improves the cells’ performance and durability.
On the product side, the sodium-ion battery is considered a sustainable alternative to the lithium-ion battery, as sodium is available in larger quantities and at lower cost and can be mined in many regions around the world. Also continuing to be a major topic is the all-solid-state battery, in which the liquid electrolyte is replaced by a solid one. It not only has higher safety due to lower thermal risks, but it also offers higher energy density, which can lead to longer runtimes and more compact battery designs.
In the case of fuel cells, the situation is different at product level, because the optimum cell assembly is not yet clear. The question behind this is, for example: Is it best to cool each cell individually or can different cell configurations be used – with increased complexity but possibly better efficiency? There are also open questions regarding the integration of multiple systems. All in all, this is a fairly open product architecture, since the major market penetration has not yet taken place and accordingly many product derivatives are emerging from research and development activities.
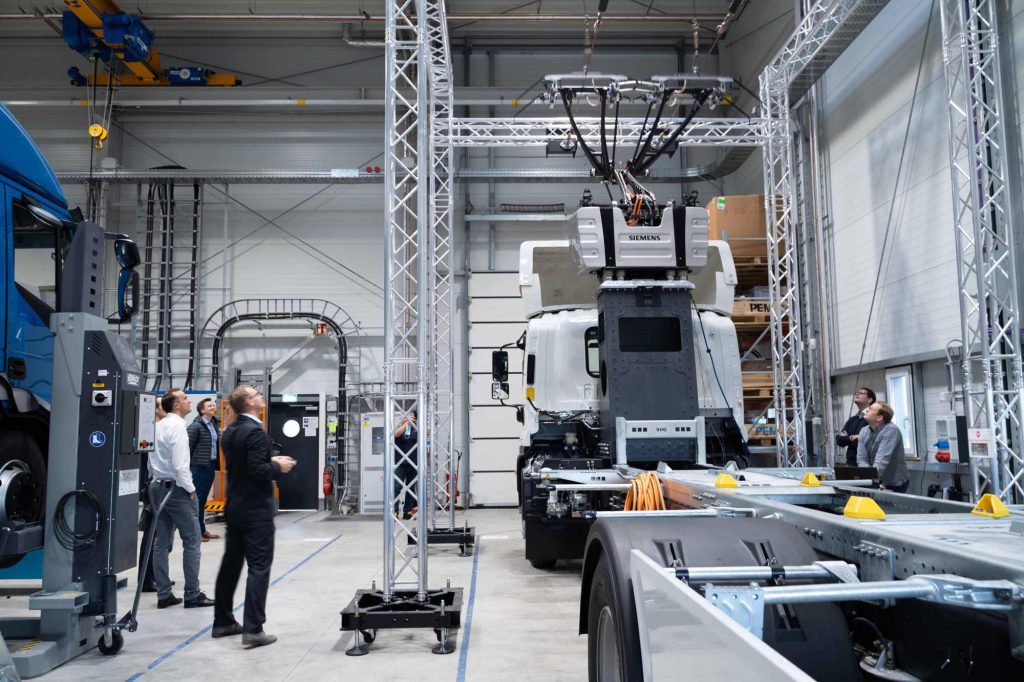
Regarding the e-motor, trends are emerging in three market areas. In the case of low-cost motors for large volumes, increasing cost pressure may lead to aluminum being used as a conductor material instead of copper in the future. Also, increasing standardization of motors can be expected. In the future, engines for medium-priced and expensive vehicles will be primarily concerned with high efficiency and good continuous performance, which is why there are likely to be many innovations, particularly in engine cooling. At the same time, it will be a question of being able to offer a large number of variants and being able to produce them. In the segment of engines with high power and high torque, as needed in sports cars, so-called axial flux motors which impress with a lot of power combined with low installation space and weight will come onto the market.
E.E: What estimations do you have for 2024?
A.K: In general, we expect for 2024 what has been clearly apparent for quite some time: Electric mobility will come. However, its acceptance and continued existence will depend to a large extent on whether we succeed in minimizing the need for critical raw materials in production, in generating the energy for both the production of the cars and the charging of the vehicles in everyday use from renewable sources, and in establishing a sustainable recycling system. Research is being conducted on all these aspects, and accordingly we reckon with positive developments there as well. On the industry side, we expect the trend among companies toward less external dependency in supply chains to intensify. Battery manufacturers are already showing that they will soon be manufacturing every component themselves much more frequently instead of buying them in as before. Current forecasts predict that in-house production of battery cells will increase from nine to 60 percent between 2020 and the period after 2024. Over the same time span, in-house production of battery modules and packs is expected to grow from 43 and 68 percent respectively to 80 percent in each case.