Knauf Industries is the plastics division of the multinational Knauf Group, the world’s first transformer of expanded polystyrene or (EPS). Knauf Industries is the leading manufacturer in the design and production of technical parts for various industries, containers, packaging and insulation in alveolar resins (EPS, EPP, among other foams) of the market, for sectors such as: Appliances, Automotive, HVAC, Construction, Furniture and Agri-Food, among others.
Easy Engineering: Tell us a short story about innovation in your company.
First of all, it is worth mentioning what our company is in charge of. Knauf Industries is engaged in research and development of plastic solutions for various range of industries. Our main business is the production of technical components made from different kinds of plastics – mainly particular foams and these made by injection molding. We have more than 35 factories around the world, located in 8 countries on 3 different continents, with more than 2,000 employees.
Our engineering team focuses on researching new solutions, business models and technologies to ensure that our customers receive the highest quality solutions we offer.
The general innovation of our company is developing expanded materials in order to provide alternative solutions with valuable characteristics for many industries. Excellent instances are in the furniture industry, where foam materials are remarkable alternative to plywood. Foam materials are also more often used in various HVAC systems where effective insulation properties are highly desirable.
What is more, nowadays, as with most industry segments, one of the leading trends in the plastics industry is the shift toward sustainability. At Knauf Industries, we are focused to increase recycled content in our products. This allows our customers to be able to significantly reduce their carbon footprint while maintaining similar technical performance.
E.E: Which are the most significant projects from 2023?
Knauf Industries Poland has been a leader in the implementation of foam materials in the HVAC market over the past year. Thanks to us, many companies have upgraded their products by replacing heavy sheet metal components with our lightweight yet durable foam materials with excellent insulation properties.
E.E: What projects were the most challenging?
Projects for large-scale ventilation equipment for the HVAC industry and projects for structural components for modular furniture. Nevertheless, for our engineering team, challenging issues provide additional motivation for action.
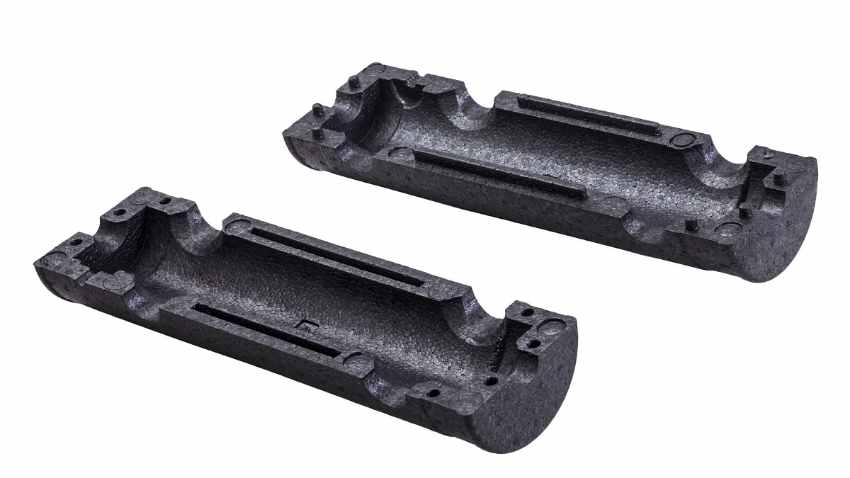
E.E: What products / solutions were used in the projects?
The solution used for these projects was expanded polypropylene (EPP), which is characterized by such features as exceptional lightness (EPP is composed of ~95% air), high durability and decent insulation parameters (thermal and acoustic insulation). Furthermore, EPP at the engineering stage can be designed in practically any shape, as a result of which it can be adapted to appliances with very complex shapes.
E.E: What are the usual challenges you encounter?
Only a few customers who come to cooperate with us are familiar with the production technology of foam materials. As a result, at the very beginning of cooperation we have to spend a lot of time educating customers and precisely defining the requirements that the final product will meet.
E.E: How did you overcome the challenges?
Our engineers support customers from the very beginning of the establishment of cooperation, so that many design errors can be caught at an early stage of the project. A feasibility study is always performed on our side before starting the production process. As part of our comprehensive cooperation, we also offer a range of pre-production services that are supported by modern computer simulations to study the most complex production processes and final product performance.
E.E: Which are the most innovative products/solutions in your lineup?
The most innovative solutions achieved by Knauf Industries in recent years include the use of EPP in modular office furniture, as well as the use of the material in large-scale HVAC appliances.
E.E: What was the research behind the products/solutions?
We knew that expanded polypropylene is a material that can successfully replace others commonly used in many industries, while being lighter than most of them, as well as comparably robust. In addition, a major added value in developing industrial solutions was the ability to mold techinical components from EPP into tailored shapes.
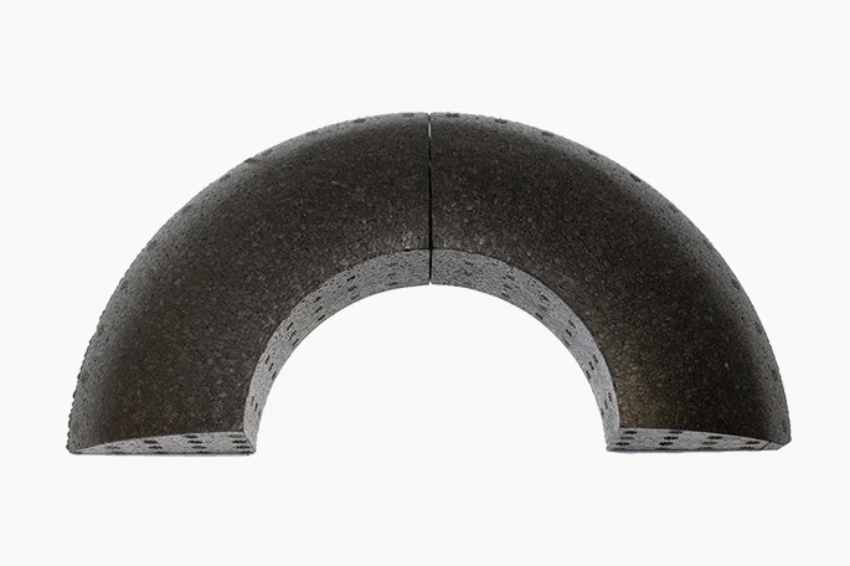
E.E: What problems / challenges do customers usually encounter?
When choosing on Knauf Industries, our customers are looking the most for solutions that can reduce manufacturing costs and at the same time to obtain a product of increased quality.
E.E: How are your products / solutions used in solving users problems?
Parts made from expanded foams as an alternative to other materials often contribute to cost optimization by reducing the number of components in BOMs and simplifying assembly processes in many applications. Moreover, it facilitates logistics processes (thanks to its extraordinary lightness).
E.E: What are your forecasts for 2024?
This year, one of our main purposes is to delve deeper into the furniture industry. Particular foams have a great potential in this industry, as proven by our projects in previous years. In addition, we are constantly working to implement recycled content materials on a wider scale. Moreover, we are introducing more and more eco-friendly materials into our portfolio such as RELOOPP, CELOOPS, NEOPS.