QUALUP SAS is a manufacturer of high-performance FFF 3D printers, specially designed for printing technical and high-temperature materials.
A brief description of the company and its activities.
Since 2011, we have been developing and manufacturing advanced solutions to meet the highest demands of Additive Manufacturing. Pioneers in the integration of heated chambers since 2013, we stand out for our unique innovations:
- Adaptives Build chambers with variable size heating in a few minutes
- Laminar flow chamber for optimal control of the printing environment
- Print heads compatible with high temperature pellets and filaments
- HT Camera with zoom on the nozzle for precise monitoring of the printing process
What are the main areas of activity of the company?
QUALUP SAS specialises in two major areas:
- Design and manufacture of high-temperature 3D printers and advanced print heads: We develop FFF 3D printing solutions adapted to technical and high-performance materials, PEI, PEKK, PPSU… Integrating innovations such as adaptive heated chambers, print heads for high-temperature pellets and filaments, and advanced filament quality control systems.
- Research and development dedicated to AM industry: We continuously invest in R&D to design solutions tailored to the specific requirements of industry. Our expertise in digital simulation and AM enables us to support our customers in optimising their processes and integrating advanced technologies.
What’s the news about new products/services?
The QU4-HT 2025 is available with new head autorizing nozzle change at cold without tools.
An innovative infinite rotating head: PIVOT will be released this year, this head will cut the print time by up to 3 compared to a standard print head, while keeping same print quality
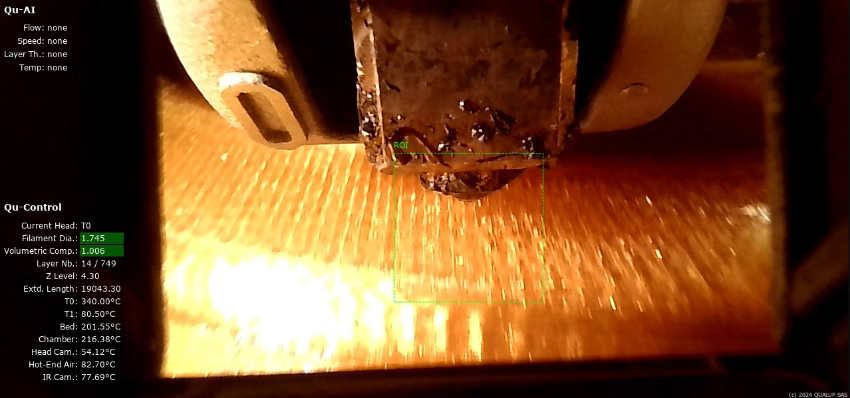
What are the ranges of products/services?
Our product range centres around ‘Qu-HT’ high-temperature 3D printers, which come in three models:
- Qu4-HT: Printing volume of 400 × 400 × 400 mm with a chamber heated up to 300°C
- Qu4-HT+: Printing volume of 400 × 400 × 500 mm, chamber up to 300°C
- Qu5-HT: Printing volume of 500 × 500 × 500 mm, chamber up to 280°C
In addition, this year we are going to launch a new range of rotary printheads, enabling a significant reduction in printing time, in the range of 2 to 3 times.
These heads will be compatible with machines using Duet3 and Klipper controllers, facilitating their integration on existing platforms.
What is the state of the market where you are currently active?
We are mainly active in the high-temperature polymer market, which is aimed primarily at R&D companies and manufacturers producing single parts or small series. This segment, focused on technical applications and advanced materials, remains relatively less affected by the crisis currently affecting other AM sectors.
What can you tell us about market trends?
AM is currently going through a major consolidation phase. After the enthusiasm of the 2010s, when massive investments were made, the market is now facing industrial reality. Many companies in the sector, despite considerable fundraising efforts about ten years ago, are still struggling to achieve profitability.
The sometimes excessive marketing promises have led some investors to overestimate the potential of AM for mass production, without taking into account its technological and economic constraints.
Although AM is now a proven technology for rapid prototyping and the production of technical parts in small series, it is still poorly suited to large-scale production, particularly for large parts.
One of the main obstacles is physical: when the size of a part is doubled, the volume of material required increases eightfold, resulting in an exponential increase in printing time. For example, a part measuring 20x20x20 mm will require a printing time that is six times shorter than the same part measuring 40x40x40 mm, and even less than a part measuring 80x80x80 mm, where the time ratio can exceed a factor of 40, or even up to 55 depending on the geometry and the desired infill percentage.
For example, although FFF 3D printing shares the same control language as a CNC milling machine – GCode – it does not have the same manufacturing optimisation possibilities. With a CNC milling machine, it is possible to use very large diameter roughing cutters in succession to quickly remove large quantities of material, followed by semi-finishing cutters, then finishing cutters, and finally very small cutters for precise local reworking. In 3D printing, there is no equivalent approach: the only adjustable parameter is the nozzle flow rate, with limited possibility of over-extrusion, which is very limited in terms of optimising production times and surface quality.
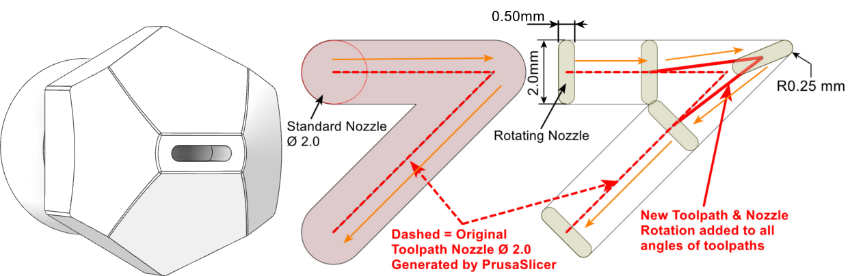
In the current state of technology, additive manufacturing cannot therefore compete with traditional processes for the mass production of large parts.
However, it remains a „magic” and relevant tool for specific applications, particularly in sectors requiring complex, personalized, lightweight parts, or parts produced in small series, such as aeronautics, medicine, certain fields of advanced engineering, methods department and R&D.
The future of this technology undoubtedly lies in optimising processes and improving print speeds and, above all, print volumes.
What are the most innovative products/services marketed?
2 products:
QU4-HT: High Temperature 3D printer
- Print volume 400x400x400, Print chamber up to 300°C, Heads 490°C
- Adaptive chamber: less than 7mn to heat the chamber for PEI 1010 (220°C)
- Excellent Thermal homogeneity: temperature variation of around 5% between different measurement points.
- Print chamber with double thermal insulation
- Laminar flow chamber: a blade of hot air approx. 100mm high passes right through the chamber across the entire width of the print bed.
- High-temperature head cameras with zoom on the nozzle.
- Monitoring display on the video image being printed: Temperatures, current layer, extruded length, etc.
- Filament and pellet heads available.
- Interchangeable print heads in less than 5 minutes.
- For each print, the Qu4-HT records all the print parameters. The files generated are Excel-compatible, so you can retrieve the data you need and check that the print has been completed correctly.
- Optionally, a Filament Quality Control adjusts the flow rate according to the actual measured diameter of the filament, guaranteeing a constant material flow rate.
PIVOT
Heavy Duty Rotating Printhead, capable of infinite rotation in both directions. This innovation enables the nozzle orientation to be continuously adjusted as a function of movements on the X and Y axes.
During linear movements, PIVOT maintains an orientation perpendicular to the direction of movement, ensuring increased print speeds and flow by simulating the behaviour of a 2.00 mm diameter nozzle.
At corners, the head pivots to reduce its effective diameter to 0.50 mm, ensuring optimum precision for fine detail.
The goal is to cut printing times by a factor of 3 while maintaining the print fineness of a Dia 0.50mm nozzle.
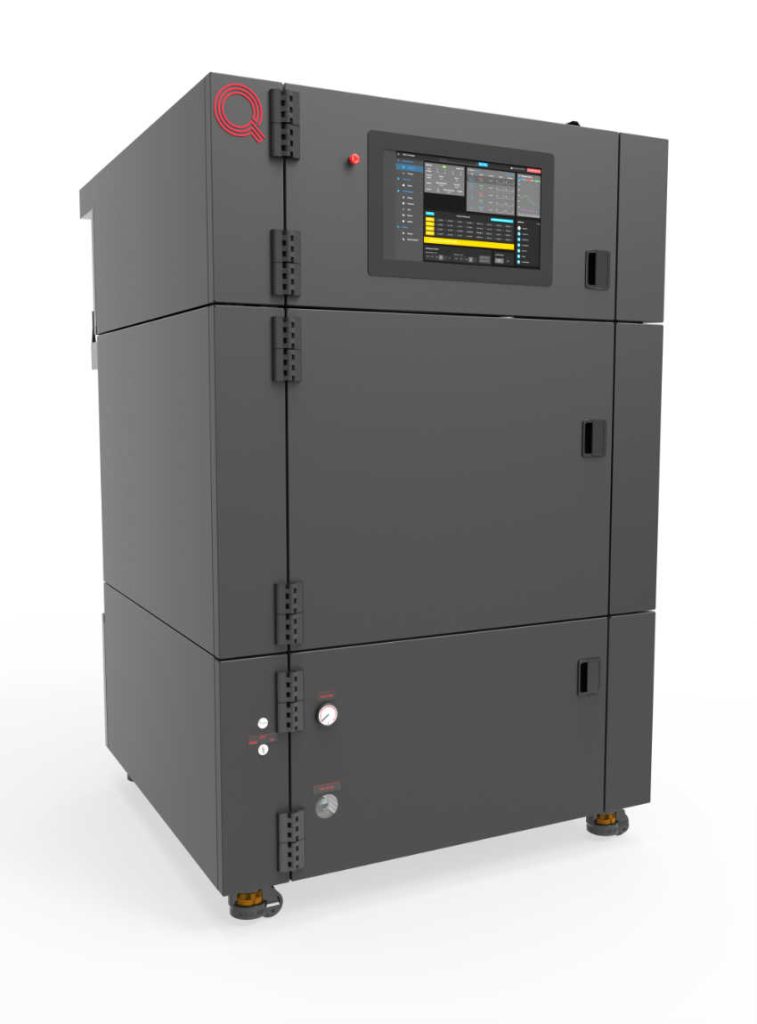
What estimations do you have for the beginning of 2025?
The beginning of 2025 is shaping up to be a rather difficult time for many sectors of additive manufacturing, with the economic climate characterised by a certain degree of caution on the part of investors and manufacturers. However, the market is tending to stabilise and, according to analysts, the outlook remains very positive.
It is essential to keep a realistic view: additive manufacturing will never replace traditional processes such as injection, laser cutting, sheet metal, machining, etc.
On the other hand, it is increasingly establishing itself as a strategic complement, offering unique design freedom and enabling the manufacture of parts with complex geometries impossible to manufacture with standard process, provided that the part volume and quantities remain suitable for this technology.