Schwäbische Werkzeugmaschinen (SW) is a leading manufacturer of high-performance multi-spindle machining centers for large-scale production of metal components. The company’s largest target market is the automotive industry. The focus has been on maximum productivity and cost-effectiveness for parts with relatively small and medium dimensions.
World premiere at AMB
The world premiere of the new BA 711 space will take place at the AMB trade show in Stuttgart in September 2022.
New SW machining centers: Larger parts, more flexibility
Recently, priorities in the industry have shifted towards larger dimensions, smaller batch sizes and greater changeover flexibility. SW has developed new machine concepts for this purpose, including more single-spindle machining centers. These new machines are of interest for the manufacture of battery housings, vehicles for rail transport, commercial vehicles, mechanical engineering and the aerospace industry, among others.
“Typical SW machining centers used to be mostly multi-spindle in design and had a double-swivel carrier that enabled loading during machining time,” explains Patrick Schneider, Product Manager at Schwäbische Werkzeugmaschinen GmbH in Waldmössingen, Germany. With each swivel of this unit, several workpieces enter the work area of the machine, where they are machined simultaneously by a corresponding number of spindles. A partition wall on this double-swivel carrier enables loading and unloading without interfering with the machining process taking place on the other side. The multi-spindle capability and the drives, which are consistently optimized for maximum dynamics, permit the shortest chip-to-chip times and highest productivity. From the user‘s point of view, the only drawback was the size of the components, which is limited by the design principle. The reason for this is the partition wall between the loading area and the work area, which is critical for this machine concept.
Shift in priorities in the industry
“Both in the automotive manufacturing sector and among other industrial users, priorities are currently shifting with regard to machine tool requirements, “ adds SW Product Manager Michael Kreuzberger. On the one hand, he says, there is a strong upward trend in terms of the dimensions of the parts being machined. Partly, he says, this is a consequence of the increase in electric vehicles, which require battery housings with very large dimensions, for example. In the area of the chassis, large structural components such as body frames or subframes are increasingly being used. As their machining takes considerably more time, the changeover times are much less significant in terms of percentage. With such large components in mind, SW has also introduced models with only one spindle in its new machine series.
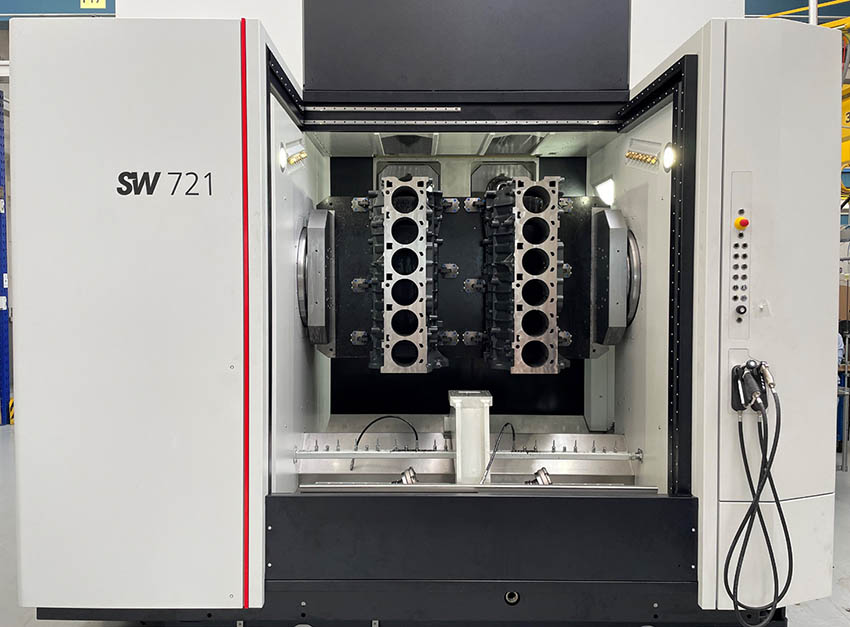
Another aspect is the significant decline in the long-term nature of orders. Today, industrial manufacturers can count less on a series running at high volumes for several years. This is causing a shift in the selection criteria towards questions of retooling flexibility and the increasing emphasis on automation.
Space for significantly larger parts without a partition wall
“To meet these customer requirements, we have expanded our machine series to include single-table machines without a double-swivel beam,” says P. Schneider. Instead of the double-swivel beam, these machines feature only a rotary axis with a clamping bridge. The elimination of the partition wall expands the available space enormously so that considerably larger parts can be machined with the same machine footprint. SW has also adopted different approaches in terms of changeover flexibility and automation by optionally equipping the workpiece carriers with integrated zero-point clamping systems. Three series of these new machining centers are currently available with different equipment variants. These new models are likely to be of interest to manufacturers in industries such as agricultural and construction machinery, industrial gearboxes, hydraulic power units, rail transport and aerospace, among others.
BA 711 space and BA 721 space for heavy machining of cast iron, cast steel or steel
“Like our previous BA 7 series machining centers, these machines are characterized by their stable monoblock design, high axis speeds and the high performance of the spindles,” explains M. Kreuzberger.
All three main axes are driven by robust ball screws. This means that the two new machines are also ideally suited for medium- and large-scale production of large, complex components.
The “space” suffix on the new additions indicates that the vertical travel of the spindle block has been almost doubled from the previous 650 mm to 1,175 mm, and the Z axis also has a 90 mm longer travel. In the case of the BA 711 space with one spindle and one workpiece carrier on the swivel bridge, this means that a work envelope of 1,350 x 1,175 x 650 mm is available without the machine taking up more shop floor space.
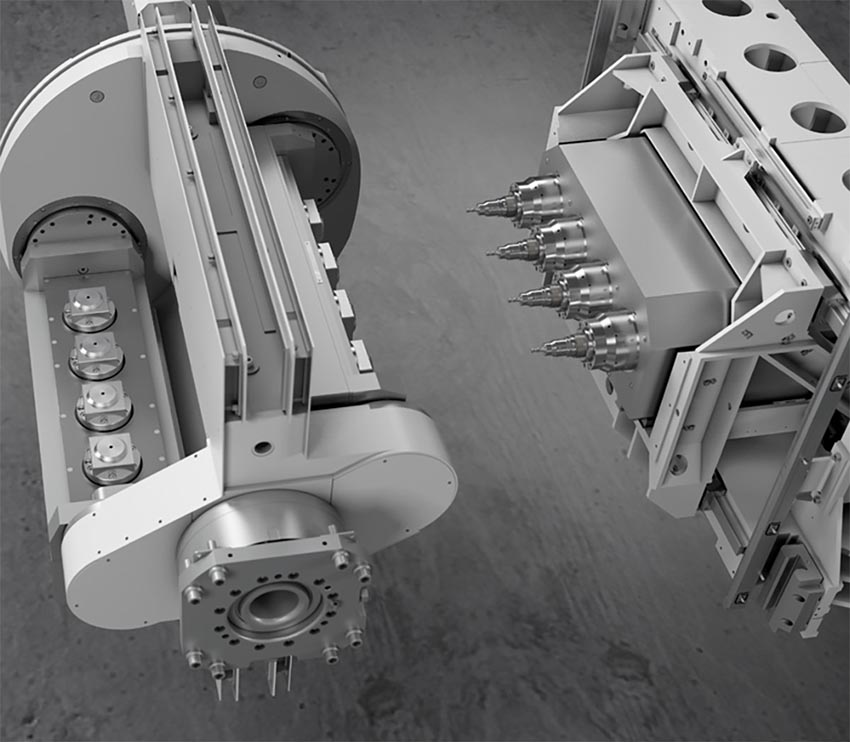
BA 721 space
The sister model BA 721 space has the same substantially expanded Y-travel of 1,175 mm and can therefore also machine longer components. However, due to the doubling of the number of spindles, the maximum available working space width per spindle is reduced to 650 mm, but productivity is almost twice as high thanks to the use of the second spindle.
Expansion of the product portfolio
In order to meet changing market requirements, SW has expanded its range to include single-station machines without double-swivel beams.
BA W08 space machines for aluminum and non-magnetic materials
Thanks to the linear drive in the three main axes, these machines achieve accelerations of up to 2 g and travel speeds of up to 120 m/min. Similar to the development of the BA 7 series, the BA W08 series has also been expanded to include models with only one rotary axis. For these machines, the Y travel has been increased from 800 to 1,500 mm. As a result, the new BA W08-11 model with one spindle and one clamping bridge has a work envelope of 1,500 x 1,025 x 660 mm compared to the 800 x 1,025 x 660 mm of the standard two-spindle BA W08-22 model. Other new models include the BA W08-11 space and the BA W08-21. The performance characteristics of the standard spindle for all models are 35 kW with 80 Nm of torque. The reliable design principles such as monoblock construction and box-in-box design of the spindle unit, which have proven to guarantee stability and precision, have also been adopted in the new BA W08 series machines.
This bridge can be loaded on both the front and rear sides, enabling workpiece changes to be carried out during machining. With its working area of 3,000 x 1,800 x 875 mm, the BA space3 allows the machining of large frame and structural components. The machine is available in a 3-axis version with a rigid spindle or, with the same performance data, in a 5-axis version with a swivel head spindle. In this version, 5-axis machining from all angles is possible. As with all SW machining centers, automation up to and including integration in complex, fully automated production lines is also offered.
“For machining aluminum and other non-ferrous materials, we have a proven series with our BA W08 machining centers.” Patrick Schneider, Produktmanger at SW.
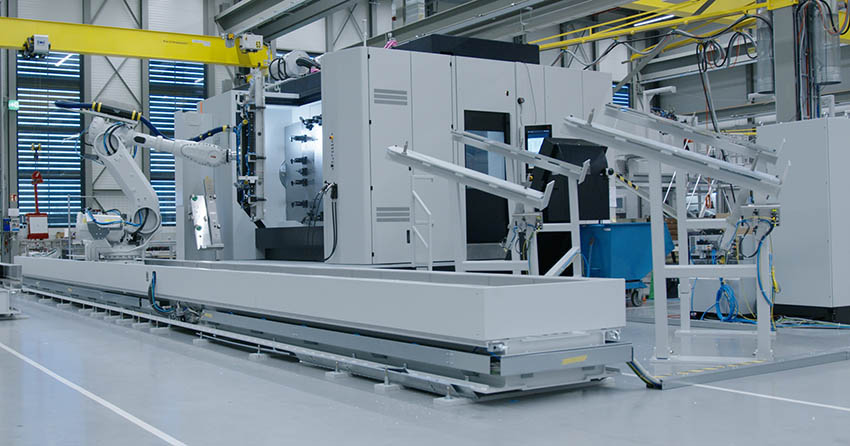
Machining large structural components – the BA space3
“In the new development of the BA space3, the initial focus was on applications in the field of e-mobility,” reveals M. Kreuzberger. Here, too, linear drives in all main axes ensure high dynamics of the machining processes. In contrast to the previous design philosophy, the BA space3 has a horizontal swivel axis with integrated clamping bridge.
Large workpieces manufactured with precision
The new machine concepts are suitable, among other things, for large-format structural components such as cast aluminum subframes, battery housings, transmission housings, engine blocks, strut domes and many more.
Schwäbische Werkzeugmaschinen
Tel.: +49 7402 74-7480
Mobile: +49173 1966533