sensXPERT is a data-driven manufacturing solution for the plastics industry that enhances productivity in real-time. Their system reduces scrap by up to 18%, energy usage by up to 23%, machine downtime by 15 days per year, and speed up cycle time by up to 30%. An intelligent manufacturing technology combines measuring hardware and data science to characterize materials in sync with machine and cavity, to control and detect all necessary influencing factors, driving process reliability.
The company’s technology supports several production processes such as Reactive Injection Molding, Resin Transfer Molding, Hot Pressing and Vacuum Infusion with a high focus on thermoset materials. sesnXPERT brings together stakeholders from the plastics part production environment to collectively solve challenges and follow a holistic approach to respond to customer demands in the automotive, aviation, renewable energy, electronic encapsulation, and construction industry.
Interview with Dr. Alexander Chaloupka, CEO of sensXPERT.
Can you describe your company’s approach to driving innovation in product development?
Alexander Chaloupka: At sensXPERT, we pursue innovation by transforming materials processing into a smart, data-driven discipline. Our apporach is rooted in the integration of real-time material characterization, AI-powered analytics and data-driven process control. We view product development not as a linear process, but as a continuous evolution toward intelligent manufacturing. This means we don’t just automate – we empower manufacturers to make decisions based on live insights during the manufacturing process. With each innovation cycle, we aim to redefine how quality, efficiency, and sustainability are achieved in plastics processing.
What recent products or solutions have you introduced, and how are they shaping the industry?
A.C: Our most recent technological advances have made it possible to capture and analyze material behavior during the manufacturing process – in real time. These innovations are helping manufacturers shift away from static, fixed-cycle production toward dynamic, adaptive control. This shift has already delivered up to 23% reductions in cycle times in elastomer and thermoset processing and has proven to significantly lower scrap rates and energy usage. By embedding intelligence directly into production processes, we’re enabling a new standard of precision and repeatability in plastics manufacturing.
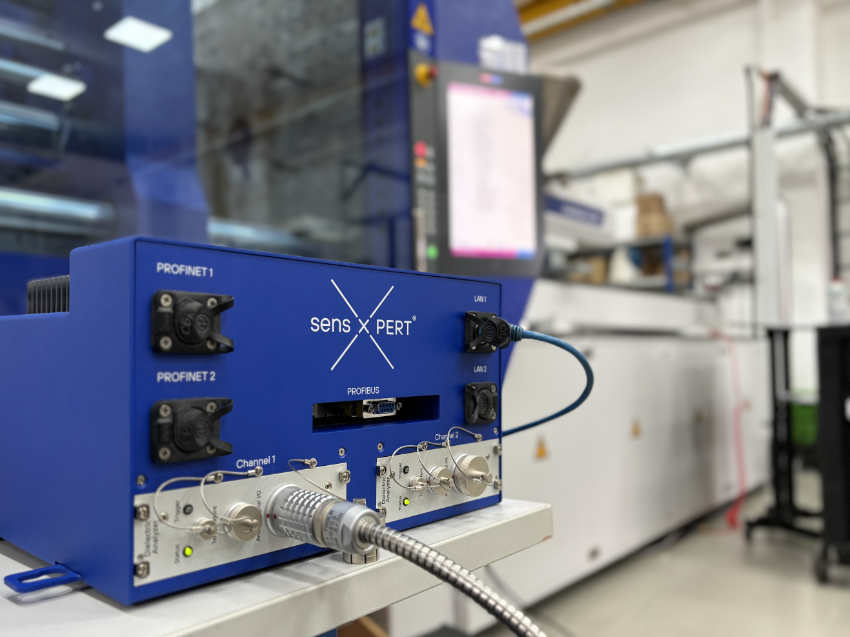
What technologies or trends are influencing your latest innovations, and how do they benefit your customers?
A.C: Our latest developments are deeply influenced by trends in smart manufacturing, including AI, edge computing, and the growing demand for production transparency. By leveraging dielectric analysis and machine learning, we offer manufacturers unprecedented visibility into curing behavior and material consistency. This enables predictive adjustments in process parameters, helping our customers reduce waste, save energy, and ensure consistent product quality—even when material batches or environmental conditions vary.
How do you ensure your innovations meet both current market needs and long-term industry evolution?
A.C: We work closely with manufacturers across automotive, aerospace, and industrial sectors to understand both their current challenges and future ambitions. Our technology is designed to be scalable and interoperable, ensuring long-term relevance even as production demands evolve. Additionally, by focusing on open standards and cloud connectivity, we enable our customers to future-proof their operations, connect their data ecosystems, and adapt seamlessly to new materials, regulations, and sustainability goals.
What challenges did you face while developing your latest products, and how did you overcome them?
A.C: One of the main challenges was adapting laboratory-grade sensor technology to withstand the harsh and variable environments of industrial manufacturing. We overcame this by developing robust dielectric sensors and embedding them into resilient edge systems that deliver reliable data in real time. Another challenge was creating machine learning models that could accurately interpret highly variable data across different materials and processes. Our solution was to use an iterative approach with close customer collaboration, continuously refining our models based on real production data.
How do your latest products differentiate you from competitors in the market?
A.C: Rather than relying on assumptions or simulations, our solutions provide manufacturers with direct, in-situ insights into how their materials behave under real conditions. This sets us apart by enabling truly adaptive process control. Manufacturers gain the ability to optimize every single production cycle—reducing curing time by up to 9% in fast-curing cases and lowering energy usage significantly. We offer more than monitoring: we empower intelligent decision-making on the production floor.
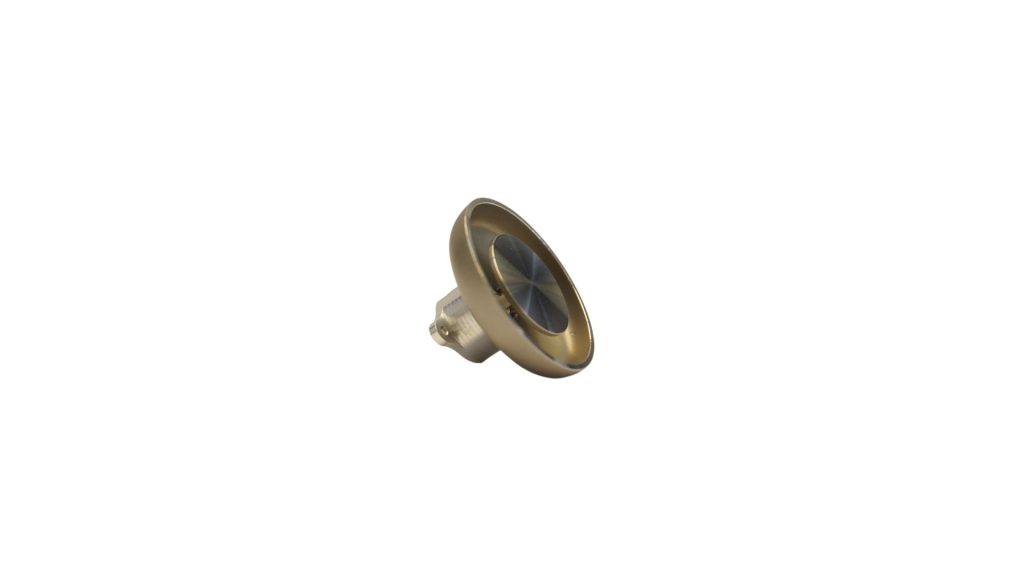
Can you share any feedback or success stories from customers who have adopted your new innovations?
A.C: A leading automotive supplier integrated our technology to encapsulate electronic components in reactive thermosets. As a result, they achieved a 4% average reduction in cycle time, with up to 9% in faster-curing cycles. Additionally, a global pump manufacturer reported a 23% average cycle time reduction in elastomer stator production—some runs reaching 32%. These results not only improved efficiency and sustainability but also increased confidence in product quality and minimized rework.
How is sustainability integrated into your product development strategy?
A.C: Sustainability is a fundamental driver behind every innovation we develop. Our technology directly contributes to reduced energy consumption, optimized use of materials, and lower scrap rates. By shortening cycle times and minimizing unnecessary curing or heating, we help manufacturers significantly lower their environmental footprint. Moreover, our cloud-based analytics allow companies to track their sustainability performance across production sites and report reliably on efficiency improvements.
What emerging trends or technologies do you think will drive the next wave of innovation in your industry?
A.C: We believe the next wave will be driven by greater convergence between AI, advanced sensors, and interoperable data platforms. As regulatory requirements and market demands for traceability and sustainability increase, manufacturers will need transparent, real-time data from every step of production. Technologies that enable in-situ decision-making, predictive maintenance, and full process traceability will become industry standard. Those who embrace this transformation early will gain a significant competitive edge.