Sirmax’s speed, flexibility and product customization have always been its most appreciated qualities. The Italian company specializes in the production of polypropylene compounds, technopolymers, thermoplastic elastomers and recycled polymers for the most varied applications. In 2021, Sirmax generated €480 million in revenue and employed around 1000 people. In addition to its quality products, Sirmax’s services have allowed the company to grow and gain market share even during the pandemic, and despite the raw material shortages and rising energy costs that continue to affect the global economy.
Among Sirmax’s most innovative services are those offered by Smart Mold, an engineering company founded as a spin-off of the University of Padua, and which is 50% owned by Sirmax. Smart Mold is carrying out a silent yet significant revolution in the world of injection molding, with a highly technical service and consulting offer.
Smart Mold supports companies from the initial stages of product engineering design, studying product applications (for example, the internal structure of a car dashboard) and the mechanical characteristics they must have (in this case, the ability to withstand loads and impact). The company then uses advanced software to simulate the product’s mechanical behavior and recommends design solutions to reduce its weight and plastic consumption. At this stage, Sirmax – drawing on its consolidated experience – provides an optimized and accurately considered material for each application.
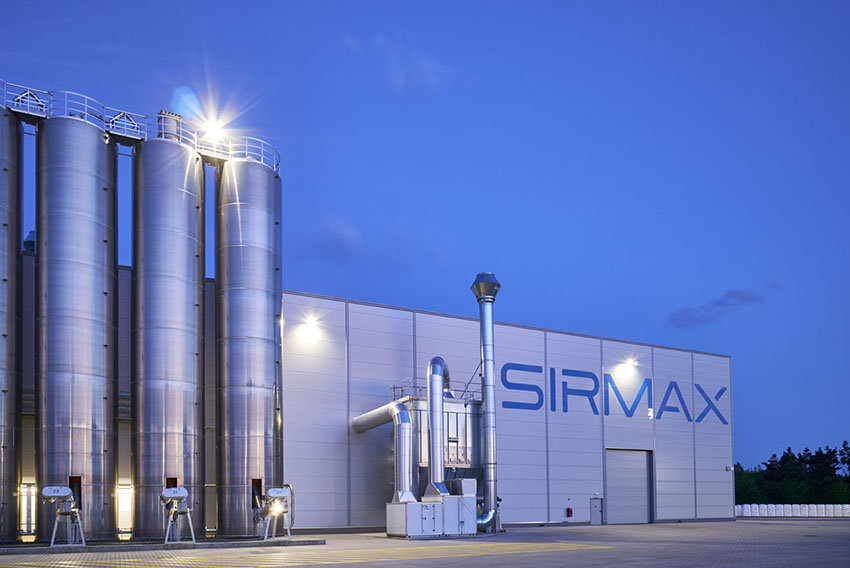
The Smart Mold team approaches the design process scientifically and rigorously. Its goal is to design and supply materials used to make high added-value components in strategic sectors such as the automotive, household appliances, electrical and electronics industries. It provides hybrid solutions that combine the performance of virgin materials with a high percentage of recycled material – a feature that is in increasing demand on the market.
“We develop advanced technologies to improve the quality and performance of injection molding,” says Giovanni Lucchetta, Smart Mold founder and partner, and a professor of Manufacturing Engineering at the University of Padua. “We co-design molded components with mold makers, maximizing their qualities and innovating the molding digitalization field.”
For clients, the end results are evident: products are lighter, cycle times, production processes and assembly stages are shorter, and costs related to materials and production times and processes are lower. Moreover, it is possible to mold several parts that would normally require welding or post-production assembly as a single component.
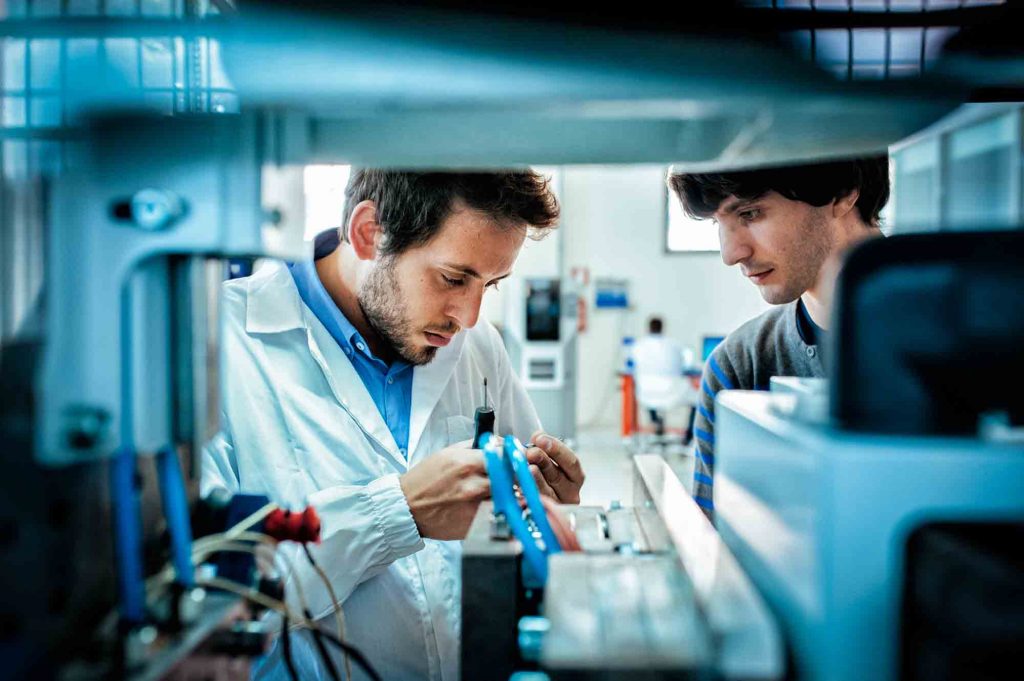
Smart Mold also stands out thanks to another service it offers its clients. Post-consumer recycled plastics usually present greater inconstancy in physical and technological properties, which limits their use in precision molding. In order to facilitate the processing of recycled plastics in this context, Smart Mold uses a digital twin of the production process. This makes it possible to detect any variations in the properties of recycled plastics in real-time, predicting and recommending parameter changes to compensate for them. It also optimizes process parameters and takes energy consumption into account.
“With Smart Mold, new possibilities are opening up for post-consumer plastics. The result is a reduced environmental impact and greater respect for the environment,” adds Marco Moretto, director of Opportunity to Market, the Sirmax division that encompasses the R&D, Marketing and Innovation sectors. “For Sirmax, it is essential to offer its clients an increasing number of services and an increasingly competitive level of innovation.”