Since 1978, Standard Industrie International has been a leading engineering and manufacturing group specialising in the handling, storage and transportation of bulk materials. Its innovative solutions help to improve production performance and efficiency, reduce maintenance costs and risks, and ensure a safer working environment. They are regularly used in more than 60 industries throughout the production process.
The AIRCHOC® prevents production stoppages due to material build-up.
The AIRCHOC® air cannonacts preventively on the material through regular shots. It is an economical solution that uses air only when the shots are activated. With a wide range of products (tank capacities from 4 liters to 400 liters), this solution is suitable for many areas of bulk material.
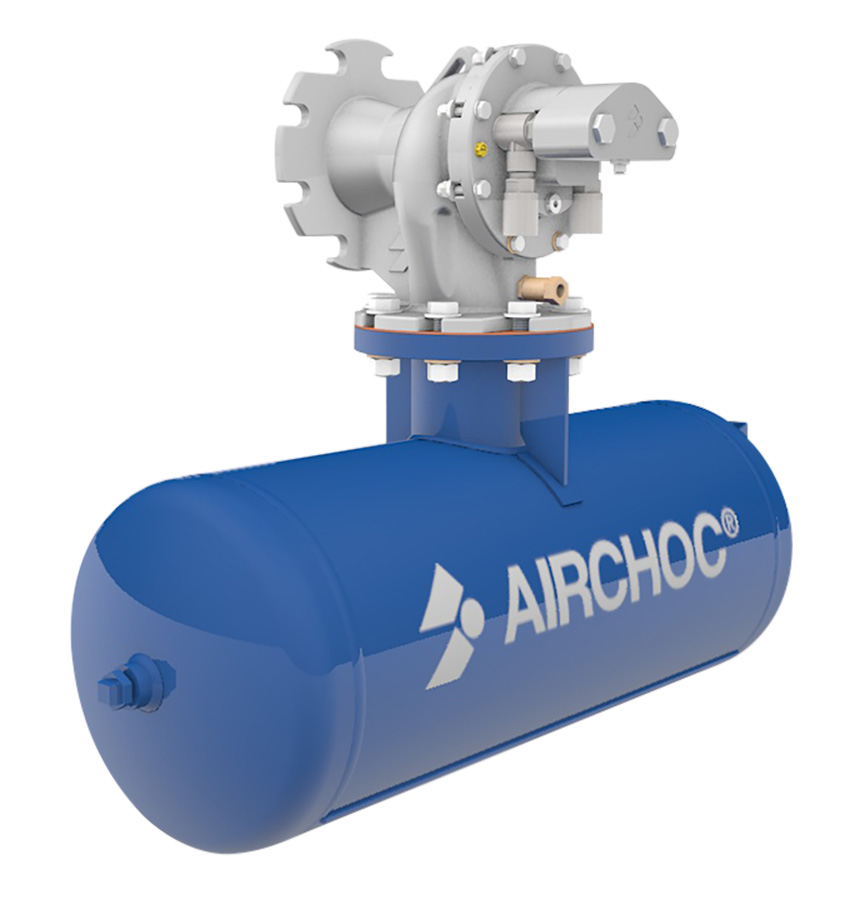
What are the areas of application of the air gun in the factory?
The AIRCHOC® is regularly installed on raw material storage units (sand, powders, flours, grains, wood chips, peat, straw, mulch, etc.). AIRCHOC® can also be found at the end of the process on fly ash or lime silos.
Used in boiler rooms, for example, AIRCHOC® air cannons, placed at the level of heat exchangers, guarantee continuous heat production and allow operators to supply energy without the risk of breakage due to fouling.
STANDARD INDUSTRIE’s technical teams carefully study the blockage factors, the behaviour of the clogged product, the inclinations of the storage unit, the productivity issues, etc… This complete diagnosis allows to establish an optimal installation recommendation according to the environment of use (various risks, high heat zone, corrosiveness, humidity). The recommended AIRCHOC® solution will also take into account the need for precise orientation of the shot, the number of shots, the diameter of the spigot according to the available pressure, the volume of the tank and the length of the spigot.
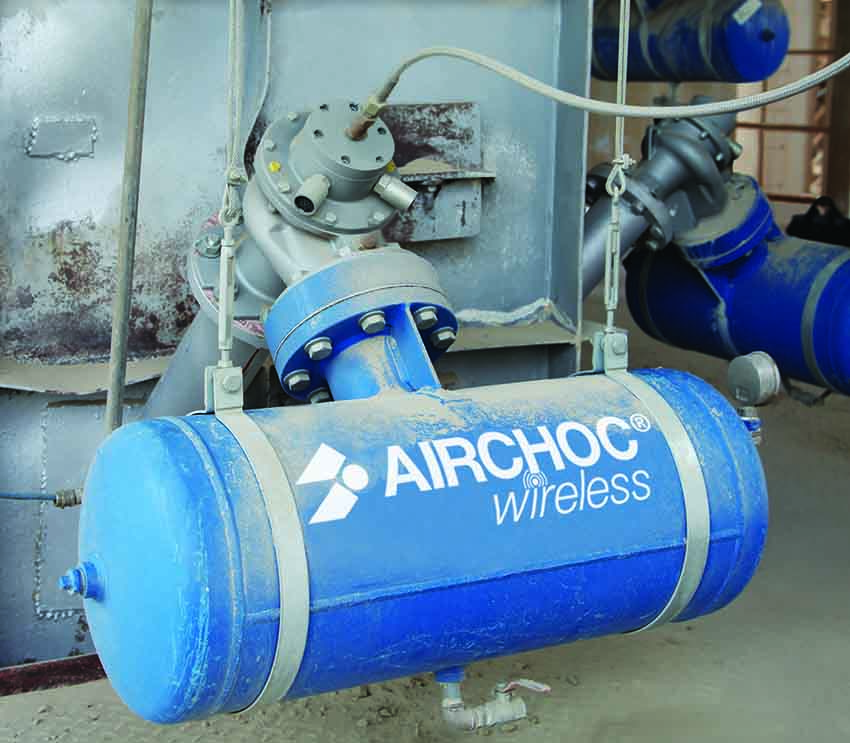
What developments are offered to AIRCHOC users?
Particularly attentive to the requirements of its customers, STANDARD INDUSTRIE, and in particular the design office team, has spent more than a year testing modifications to its legendary AIRCHOC® air cannon in order to make it even more efficient and economical.
The AIRCHOC® has always had performance, economy and safety features. The latest innovations focus on:
- saving compressed air, thanks to a better sealing of the piston and the possibility of shooting using only part of the air contained in the tank. It is also planned to program jerky shots.
- Reliability, due in particular to an improvement in the force of impact of shots from the barrel.
- (No AEP): no air passes through the piston seal, so no seal wear.
- Spare parts, such as the solenoid valve, the valve or the silencers – Rationalised and selected for their durability, these new components of the AIRCHOC simplify its maintenance.
- In this respect, Standard Industrie has also created an AIRCHOC maintenance kit that avoids the need for long and costly interventions by production site operators.
How to upgrade an existing AIRCHOC fleet?
STANDARD INDUSTRIE offers its customers fleet audits to evaluate the needs in terms of equipment renewal and homogeneity. Of course, the transition to the new version of AIRCHOC® guarantees the continuity of supply of compatible spare parts. The conversion of the fleet only concerns AIRCHOC® heads, so the change of tank is not systematic.
Building on its proven expertise with more than 5000 customers worldwide, STANDARD INDUSTRIE brings, with its new generation of air cannon, a reliable and long lasting cleaning solution.
The LIFTUBE® allows plants to meet safety and environmental standards.
Plants, subject to regulatory pressures, are looking for solutions to minimize their impact on the environment and increase the safety of their employees. They can find an answer with LIFTUBE®. Indeed, this equipment, developed by STANDARD INDUSTRIE International, is placed on belt conveyors to optimize sealing. This system thus ensures a reduction in dust emissions, loss of materials, maintenance time and guarantees the safety of operators.Â
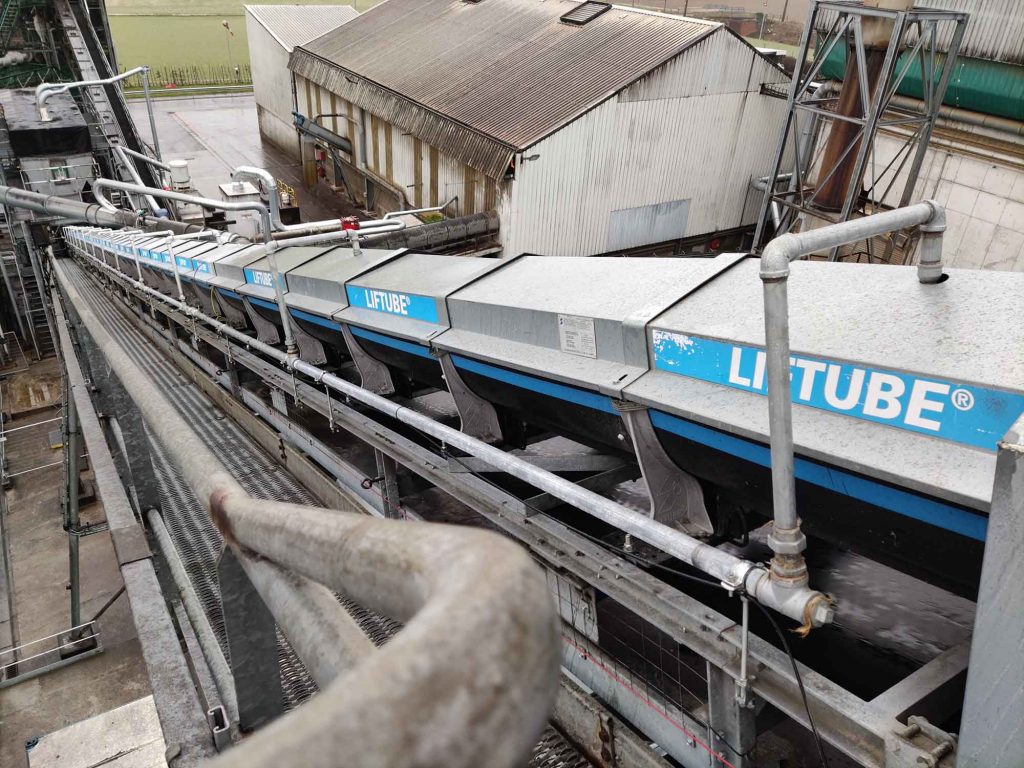
The LIFTUBE® replaces stations equipped with 3 rollers on conventional conveyors. In concrete terms, standard 1-meter modules and upgradeable modules can be easily installed on all or part of a new or existing conveyor, while retaining the original belt, chassis and motorization. This system is installed between the loading and unloading point. Available in widths from 500 to 1600 mm, in high temperature, explosive, food grade or self-extinguishing versions, it avoids any contamination of the transported product with the outside. This watertight system allows, by tilting the glideboards and the central roller, an easy and minimal maintenance.
Reduce material spillage and dust emissions
Covering rubber belts is necessary: it is a containment method adapted for some specific points, for example the protection of sand chutes, or to protect a conveyor when it is exposed to the wind.
Therefore, the LIFTUBE® is real solution to contain dust in the industry.
As an example, here is the case study of HOLCIM Theodore plant (USA) which started using an alternative fuel mix of shredded plastics, paper, and wax to supplement their energy input. Spillage around the transfer area, combined with the low-density material being blown off the belt caused an environmental headache. On windy days, the plastics and paper would be blown all over the site and end up in waterways next to the plant. The nature of the material also makes it very difficult to contain and recover once it is spilled.
The installation of 140m/460’ of LIFTUBE® on both alternative fuel conveyors contained the material on the belt and eliminated spillage. It has stopped any material being blown off the conveyor into the nearby waterways and eliminated the costly efforts to recover small pieces of plastic and paper from all over the site.
Control health and safety constraints
In a quarry, the installation of the LIFTUBE® allows customers handling silica to comply with the new regulations on dust emissions from this material.
The LIFTUBE® device has enabled the plant to drastically reduce dust emissions and material losses and, as a result, its cleaning and maintenance costs have decreased considerably.
Thanks to the belt containment provided by the LIFTUBE® design, the product circulates as if it were in a sealed envelope, thus reducing the outward flow of material as well as the loss of material from the belt. Because the cover can be clipped on, it snaps perfectly into the upper grooves of the Glideboards Supports and therefore provides a perfect seal to the system. This sealing is also achieved by the foam-laminated hoops which, installed at each end, enclose the strip.Â
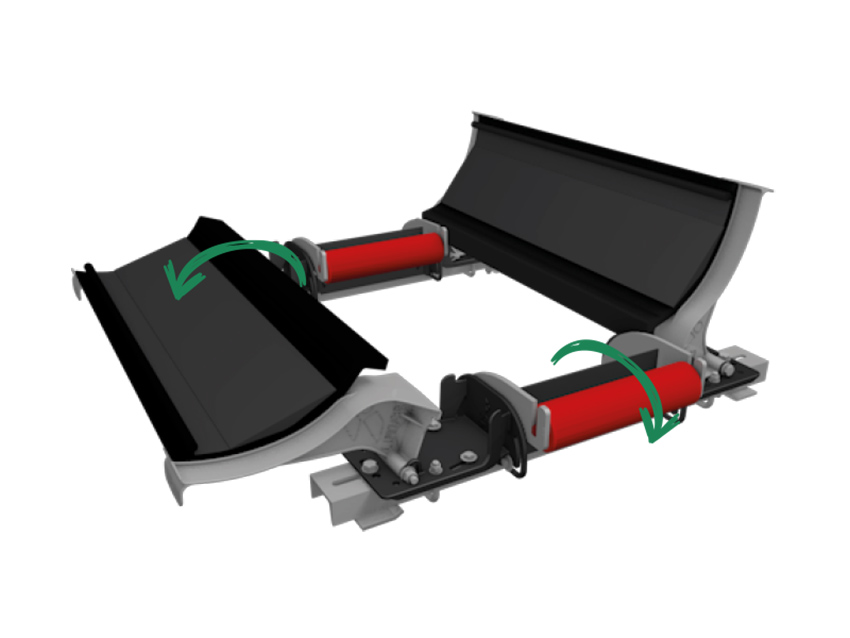
It is these advantages that can create a healthy interest when the transported product presents a danger to the operators. The latest measures against silica can be included in these conditions.
Thus, the enclosed belt, controlled material overflows, reduced cleaning requirements and reduced exposure to a product considered hazardous, mean that the LIFTUBE® system has all the advantages needed to be part of the search for a healthy solution for industrial equipment for the transport of low or high toxicity powders.
Standard Industrie International’s range of solutions can cover most of all customer needs, regardless of the volume of cleaning required or the optimization of existing conveyors that are failing.
It can help plants with handling and storage problems optimize the performance of their production tools while reducing their operating and maintenance costs.