Young post-doctoral researcher of the Center for Medical Robotics at the Korean Institute of Science and Technology (KIST) (Seoul, Republic of Korea) applied to conduct his experiment of an inertial parameter identification by using a geometric algorithm on a challenging platform.
TERRINet project gives an opportunity to excel the research ideas (beyond the limits of home infrastructures) also to non-European students, researchers, and industry.
Byungchul An’s experiment on ARMAR-6 platform (offered by the TERRINet partner Karlsruhe Institute of Technology (KIT) – Germany) is definitely a story of success.
»ARMAR-6 dual-armed platform is not challenging only hardware-wise, but also software-wise. It is hard to find a platform with a combination of torque-controlled, redundant, and dual-arm manipulators, that is mobile and also with broad-spectrum of well-working libraries«, explained Byungchul his motivation for participating in the TERRINet project.
The main purpose of his experiment was to identify the inertial parameters of an object held by two arms, which leads to improved control performance and better manipulation strategy.
By conducting such experiments on a robot, like ARMAR-6, which was assembled for a safe humanoid robot collaborative assistance for industrial environments, we can make an important step forward in a smart factory’s automatization.
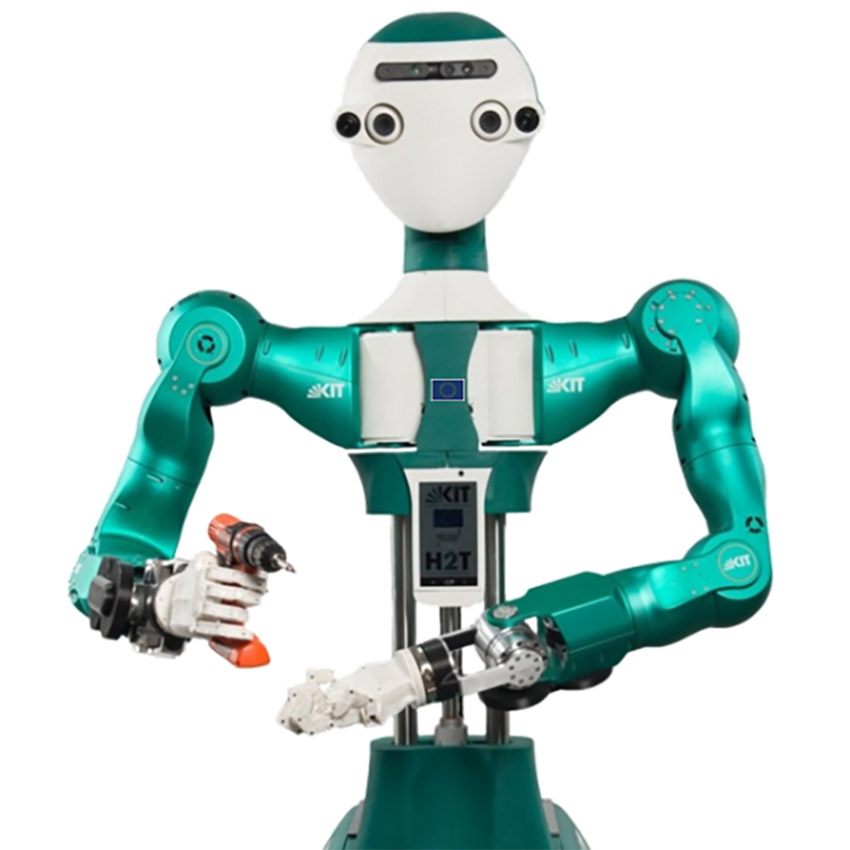
The Key to Human-Robot Collaboration in an Industrial Environment is Efficient Manipulation Of Large and Heavy Objects
To enable a close human-robot collaboration in an industrial environment, a quick and efficient manipulation of not only light and small object, but also large and heavy ones, needs to be assured.
The manipulation of the latter usually requires the usage of bi-manual handling, which can significantly improve performance by identifying an object’s physical parameters (the inertial parameter identification).
The inertial parameters of an object can be expressed as elements in the vector space, which values must satisfy a certain physical consistency condition (Traversaro et al. 2016); 4×4 symmetric positive-defined matrixes (Wensing et al. 2018).
The identification can be conducted by force/torque (F/T) sensors on two arms’ wrist, regardless of potential non-linear effects on the joints.
Two-Step Application of The Geometric Inertial Parameter Identification Algorithm
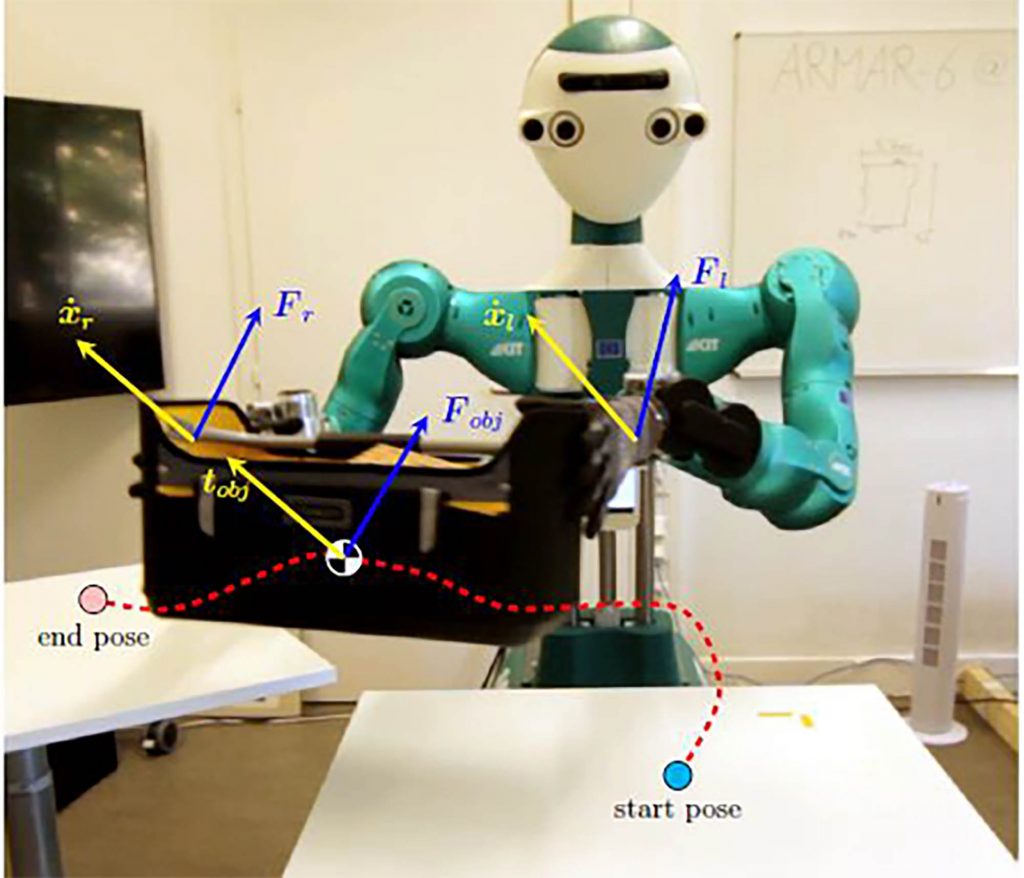
The experiment was conducted in two steps:
STEP 1: Execution of series of bimanual tasks to obtain the data using the ARMAR-6 platform:
For this purpose, the implementation of one of the bi-manual compliance controllers developed by the host institute was conducted (Figure 2). As a result, the data for the inertial parameters identification of a handled object was obtained.
STEP 2: Application of the geometric inertial parameter identification algorithm to dual- arm manipulation:
Dual-arm manipulation is accompanied by a closed-loop kinematics structure. To apply the proposed geometric algorithm (Lee & Park, 2018; Lee et al. 2020), the robot’s dynamics equations should take into account the kinematic constraint.
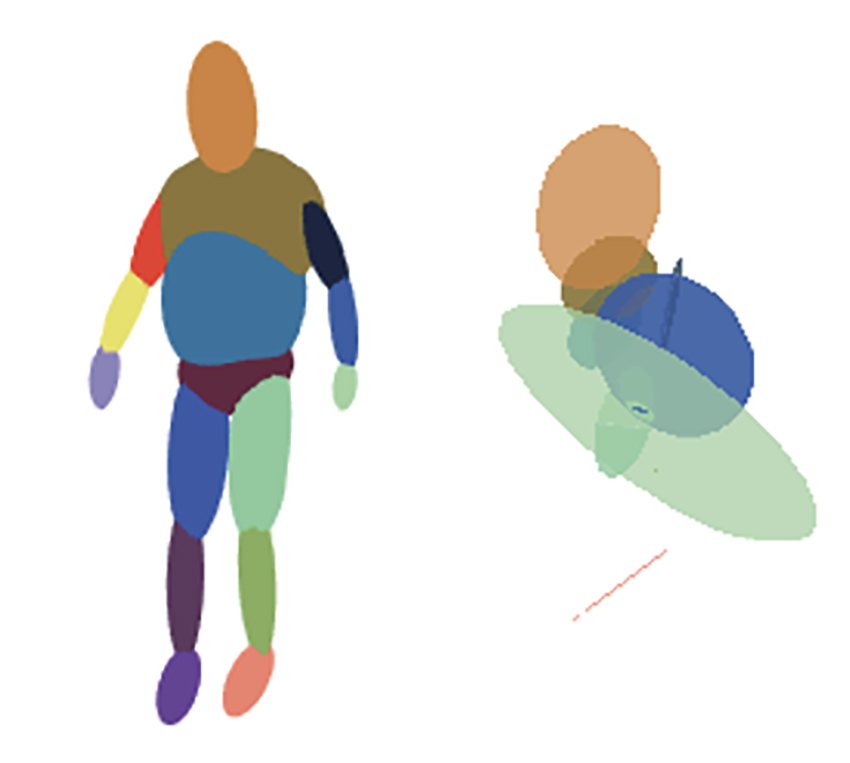
The Validation Of Identified Inertial Parameters by the Usage Of Geometric Algorithm
The conducted experiment showed, that to validate identified inertial parameters by the usage of geometric algorithm we can compare directly the mass and joint torques (obtained by solving the inverse dynamics). However, inertia matrices cannot be compared directly.