The logistics industry is booming. With demand growing rapidly, there is an urgent need for innovative transport solutions, especially within the warehouses. BHS Intralogistics has developed an autonomous transport shuttle that is both compact and powerful. The brain of the shuttle is the ESX.4cs-gw control unit from the German automation specialist STW.
Hardly any other industry has experienced the years of upswing currently being experienced by the logistics branch. In 2020, the Corona pandemic and the associated increase in demand in e-commerce meant positive results throughout the branch. However, continued growth is leading to a shortage of skilled workers within the industry and an increasing need for automation, especially in intralogistics. More and more frequently, autonomous tugger trains and automated high-bay warehouses are taking over tasks that were still being performed by skilled workers just a few years ago. This trend is enabled by increasing digitalization of the infrastructure within warehouses, and increasingly powerful control and sensing technology in autonomous vehicles and machines used in the internal material flow.
An individually scalable transport platform
BHS Intralogistics GmbH is a joint venture, founded at the end of 2018 between the machine and plant manufacturer BHS Corrugated GmbH and automation and control specialist KS CONTROL GmbH, which has specialized in the development of machines and systems for automated processes in internal material flow and load tracking.
One of these machines is the iShuttle, an autonomous mobile transport platform with a load capacity of up to 4.5 t. The shuttle is only 285 mm high and can be integrated into the in-plant transport flow, independent of the spatial conditions, with 2D laser navigation or camera supported line guidance. Multiple iShuttles of different sizes can be integrated as a fleet solution with the autonomous shuttles customizable to the customer’s requirements. With different platform configurations such as lift table, push & pull function for goods transfer, belt or chain conveyor and variable travel speeds, the iShuttle is suitable for a wide range of intralogistics tasks.
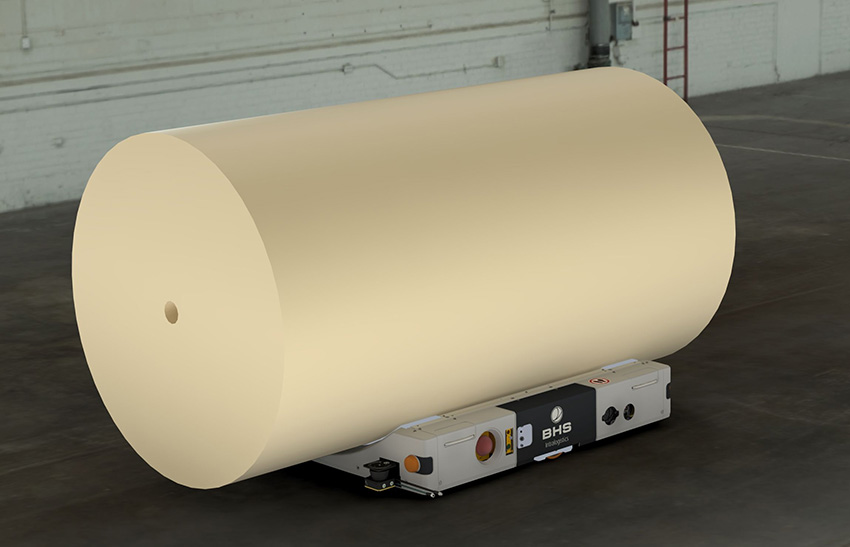
Safety first
Control systems from STW play a significant role in the safe operation of the autonomous transport platforms. The automation specialists have been supplying control components for mobile machinery for over 35 years, from agricultural technology and construction machinery to material handling machines, as in this case. When BHS Intralogistics was looking for a control system manufacturer that could offer proven functionally safe controllers for their industry, the choice quickly fell on the ESX controller family from this long-established company from Kaufbeuren, Germany.
„With the development of our iShuttle, we did something very new. It represents the first autonomous driverless transport system in our portfolio, and we were looking for control expertise with plenty of experience, especially regarding the functionally safe design of mobile machines. STW is exceptionally well established in this field,” explains Tristan Warias, software developer at BHS Intralogistics.
In the iShuttle, an ESX.4cs-gw operates as the master controller. The ESX.4cs-gw has a three core processor (an Infineon Aurix, 3 x 300 MHz), six CAN bus interfaces and five Ethernet interfaces. With the help of a managed four-way 100 Mbit/s Ethernet switch, large amounts of data can be selectively forwarded in the system without using processor power. “With our new generation of controllers, machine manufacturers have even more performance at their disposal. The powerful processor and extensive support for sensor integration contribute to this,” says Stefan Hohn, STW project manager, in explaining the advantages of the ESX.4cs-gw.
In the iShuttle, two additional ESX.3ios controllers are connected to the master controller via CAN, expanding the functionality and connectivity options, for example for the autonomous vehicle’s extensive sensor suite. To avoid any safety risk, the ESX controllers regulate the iShuttle’s drives in accordance with Safety integrity Level 2 and Performance Level d. This was the functional safety requirement for the iShuttle to be able to operate in an industrial environment.
Application specific programming
Users of the ESX.4cs-gw have various options for the development of the application software at their disposal: The open and free open source development and life cycle management tool openSYDE from STW offers the possibility to map and test functionalities in “C” as well as according to IEC61131 (logi.CAD3) in Structured Text (ST). Even older, existing systems can be configured, managed, and updated with the help of openSYDE. Via the numerous pre-installed widgets in openSYDE, data available via CAN or Ethernet can be displayed graphically and used in HMIs or cloud solutions. Numerous convenient functions such as current controlling and ramp functions for outputs or frequency averaging for inputs are already integrated. Additional libraries simplify system integration. An 8 MB flash memory, 2 MB RAM and a 32 kB EEPROM are available for the customer application.
BHS Intralogistics used STW support and consulting during the development of the iShuttle to get the most out of the programming environment and to build a standards-compliant safety architecture. “Despite Corona and the associated contact bans, STW Service was there to help us with advice and support, providing various online seminars. This helped a lot with the system design,” recalls Tristan Warias.
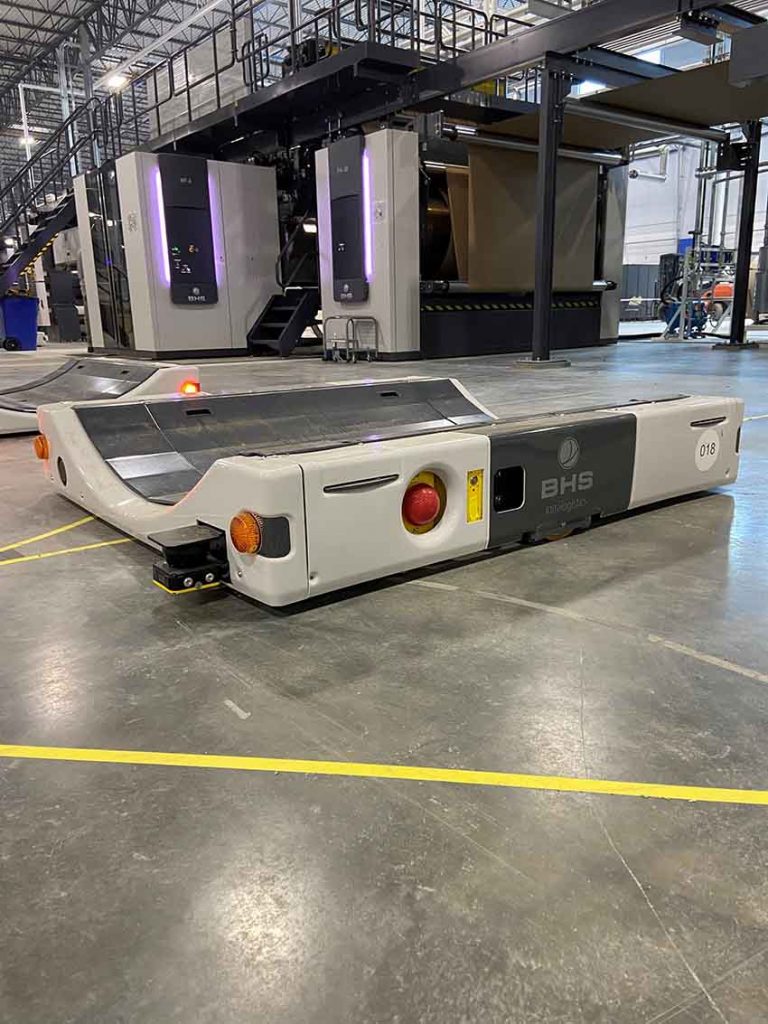
A collaboration approach
The iShuttle from BHS Intralogistics is a high technology solution for one of the fastest changing industries of our time. Anyone who has had the chance to experience a swarm of autonomous vehicles working together knows what an impressive sight this is. STW’s flexible and safe control solutions are fundamental to this exciting experience. The iShuttle is another example of a successful partnership between an innovative machine manufacturer and the automation experts at STW.
About STW
As an internationally active company with Headquarter in Kaufbeuren, we stand for the digitalization, automation and electrification of mobile machines for 35 years. With generic or customer-specific products, systems and solutions developed and manufactured at our headquarters in Germany, we support our customers with innovative technology on their way to making their machines the best in the world.
Supplemented by partner products and accompanied by our training, support and system teams, we help medium-sized companies and large OEMs to increase the performance and efficiency of their machines and increase safety. Through communication between machines, connectivity with cloud platforms and additional partner services, we enable the integration of mobile machines into business processes.
Sensor-Technik Wiedemann GmbH Phone: +49 8341 9505-0
Am Bärenwald 6 Fax: +49 8341 9509-55
87600 Kaufbeuren E-mail: presse@wiedemann-group.com
Deutschland Internet: www.stw-mm.com