Electric cars have become an integral part of the modern automotive industry and are a crucial component of the pursuit of a more environmentally sustainable future. Global production of electric cars numbers in the millions, with leaders in this field being the United States, China, and Germany. However, every electric car is essentially a machine, and like any technical system, it can experience malfunctions and issues, even in high-end, hand-assembled vehicles. These issues can be quite normal for any technical system.
One crucial aspect of electric car breakdowns is that battery malfunctions can lead to fires, resulting in significant financial losses. For this reason, electric car manufacturers have equipped their batteries with appropriate protection systems. Nevertheless, continuous monitoring of the battery’s technical condition and immediate repairs upon detecting faults are key to the safety and efficiency of electric cars.
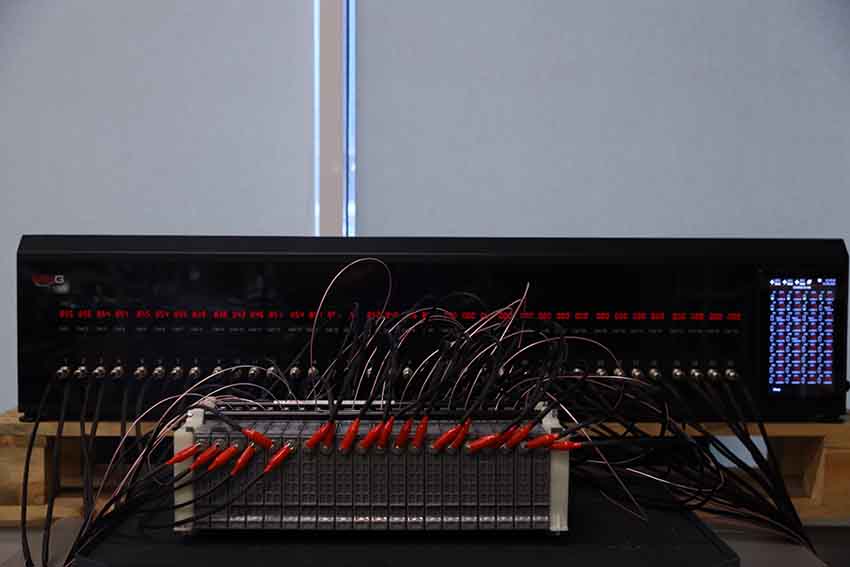
How to assess the condition of an electric car’s battery?
Every modern electric car is equipped with a self-diagnostic system that allows for the monitoring and analysis of the battery’s condition. By connecting a diagnostic scanner to this system, you can gather data on voltage, current, temperature, and other battery parameters. With this information, an experienced electronic mechanic can assess the overall battery condition and identify the source of any faults.
If problems with one or more modules are detected, it’s necessary to remove the battery from the car and disassemble it to access the problematic modules. This is where the MS800 tester for nickel-metal hydride (Ni-Mh) and lithium-ion (Li-Ion) batteries comes into play.
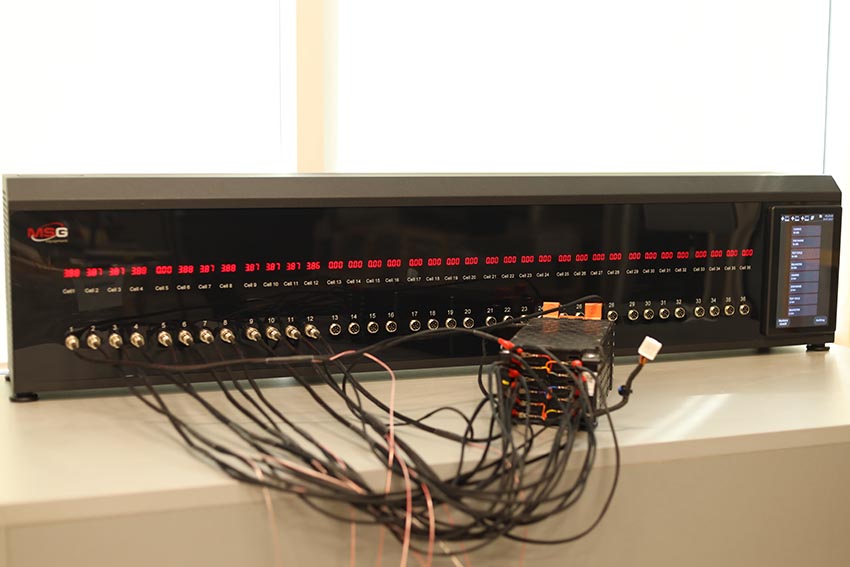
Features and capabilities of the MS800 tester:
- Measures the capacity of high-voltage Ni-Mh and Li-Ion battery modules. The remaining capacity of these modules is a critical indicator of the electric car battery’s technical state.
- Balances the charge levels of serially connected Ni-Mh modules during hybrid battery repairs.
- Voltage-balances the modules before assembling and installing the battery in the car, ensuring that all modules have the same charge level.
- Prepares modules for storage by charging them to a specific level. A capacity of 30% to 60% is considered optimal for storing lithium-ion batteries.
The specific features of the MS800 Li-Ion battery tester include:
- 36 independent, galvanically isolated channels for module testing and balancing.
- Test status indication for each channel.
- Flexible parameter adjustment for testing.
- Protection against incorrect battery connections.
- Temperature monitoring and prevention of overheating.
- Automated testing process.
- The entire testing process is saved and can be analyzed using dedicated software.
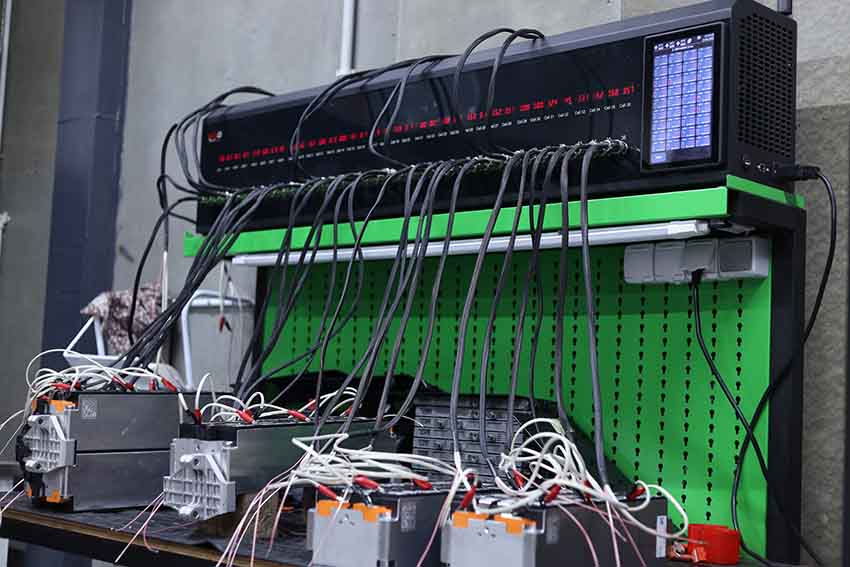
Conclusion:
Electric vehicle battery repair service and hybrid battery rebuilding provides a unique opportunity to enter a growing market and take your business to the next level. As the number of electric cars on the road increases, the service for high-voltage battery repair will play a crucial role in ensuring the reliability and long-term performance of electric vehicles. A successful business in this field requires the right skills, a commitment to continuous learning, and specialized equipment like the Li-Ion battery tester. All of these factors offer excellent prospects for development and profitability.
To learn more about the MS800 electric car battery tester, you can watch this video or visit the websites: https://servicems.eu/ and https://msgequipment.pl.
You can also get detailed information by calling these phone numbers: +38 (073) 529-64-26, +48 886 89 30 56 (Viber, WhatsApp, Telegram).