The term “sustainability” has become increasingly popular in recent years. It is frequently seen in headlines, featured in forms of news media, scientific research, and practical seminars. Is the word sustainability merely a trending word or the question of the hour?
The emphasis on sustainability stems from global growing awareness intended for critical environmental issues and climate change, largely caused by human activity. The focus on sustainability reflects our deep commitment to the principles of securing a better future for the planet and generations to come.
Consequently, sustainability has gained prominence in various fields, ranging from everyday life and business to transportation, urban planning, and manufacturing. Manufacturing should unquestionably be sustainable. Today, there is widespread recognition and agreement regarding the correctness of this statement. Manufacturing processes use natural resources, consume energy, create waste, and pollute the environment. We can mitigate the negative environmental impact only by adopting sustainable production technologies.
Machining remains a primary method for producing parts of machines and mechanisms. Therefore, the question of how to make machining sustainable is relevant more than ever. A cutting tool contacts the machined workpiece directly and shapes it to its required form, removing the rest of the unnecessary material in the form of metal chips. Can a cutting tool be a key factor for improving sustainability? The answer to the above question is undoubtedly a resounding, yes!
Despite its smaller size in comparison to other elements of a technological system, the machine or workholding fixture called the cutting tool can play a pivotal role in achieving sustainable manufacturing practices. The cutting action involved in material removal during machining is an energy-intensive process. However, the cutting tool is designed to be energy-efficient and, therefore, can significantly reduce energy consumption.
The impact of key tool characteristics cannot be underestimated. Advanced cutting geometries minimize cutting forces while anti-vibration designs mitigate chatter, which causes force oscillation. Progressive coatings enhance lubricity, diminishing friction, and efficient cooling methods effectively reduce heat generation. Collectively, these tool elements substantially reduce the environmental impact of machining operations.
In many instances, a cutting tool can hinder productivity growth, limiting the full realization and capabilities of modern machines. Therefore, tools that guarantee higher productivity play a crucial role in reducing cutting time, machine power consumption, and greenhouse gas (GHG) emissions. Reliable, long-lasting cutting tools that enhance tool life, reduce the frequency of tool replacements, or insert indexing. This diminishes machine downtime associated with tool changes, ultimately improving overall manufacturing efficiency.
In addition, utilizing cutting tools that provide a better surface finish can eliminate the need for finish machining operations, thereby decreasing the machining allowance or material stock to be removed. As a result, a dual effect is achieved reducing both machining time and material waste.
Hence, the term “sustainable cutting tool” is not merely a passing trend but a vital concept that is progressively embraced and integrated as a fundamental principle of sustainable manufacturing. Ultimately the main parameter to analyze a tool is its performance. However, the component of tool sustainability has become a contemporary factor of paramount importance. Understanding the various aspects of how cutting tools impact sustainability largely shapes the requirements for modern tools and guides their development.
A case study featuring how ISCAR’s tools improve machining sustainability.
How can a cutting tool improve machining sustainability? A brief review of select ISCAR products helps us to understand this profoundly. The design concept of tools with replaceable cutting parts significantly contributes to the sustainable utilization of cutting material.
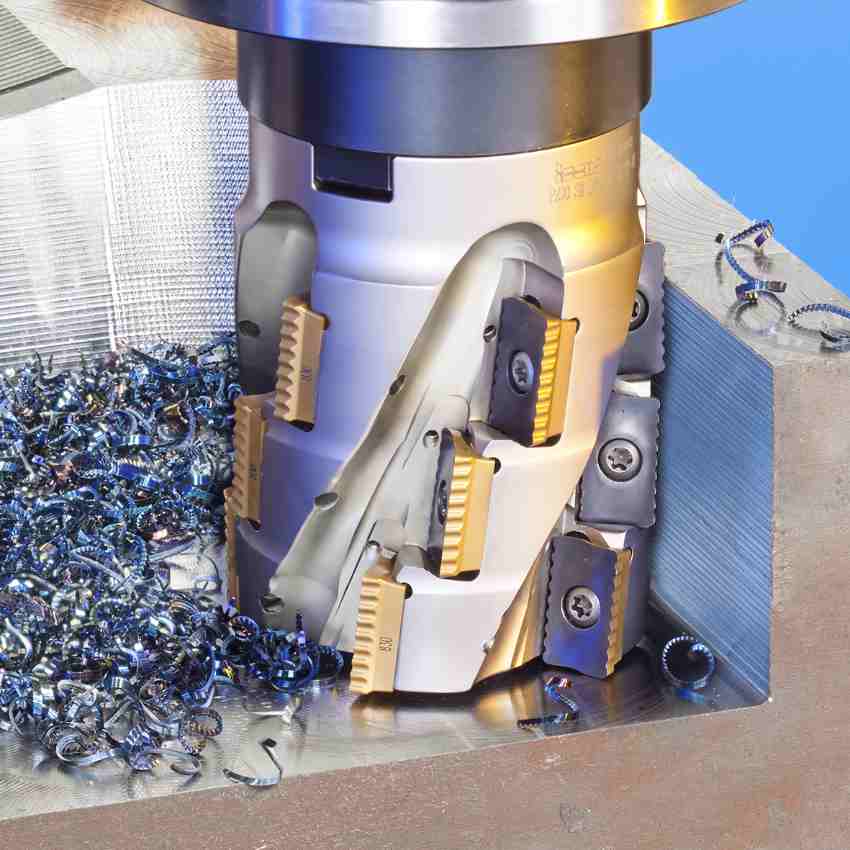
ISCAR’s tool systems with exchangeable carbide heads, such as MULTI-MASTER and SUMOCHAM, provide a good example of this concept by allowing the rational use of cemented carbides. In addition to the traditional approach of saving cutting material, the mentioned systems offer further advantages related to sustainability. Both the MULTI-MASTER and SUMOCHAM families feature high repeatability, which allows for the realization of the NO-SETUP-TIME principle. This means that replacing a worn head does not require additional setup operations to adjust tool parameters. As a result, machine downtime is significantly reduced.
LOGIQ-3-CHAM represents the next step in the development of drilling tools with exchangeable heads, based on the features of its predecessor, the SUMOCHAM drilling line. One notable parameter that sets LOGIQ-3-CHAM apart from the other drilling systems is its three flutes (Fig. 1), as opposed to the traditional two. This change enables increased feed and speed of up to 50%. Alongside improved productivity, this new design also brings sustainability advantages by reducing energy consumption and GHG emissions. Drilling 16mm diameter holes with an 80mm depth in a part made from low alloy steel exemplifies these features well. With a tool life of 500 holes, when compared to a competitor’s drill with a replaceable two-flute head, the use of ISCAR’s LOGIQ-3-CHAM tool results in a 26% decrease in cycle time and a 19% decrease in energy consumption. Consequently, CO2 emission is reduced by 19%.
The anti-vibration design of cutting tools plays an essential role in reducing power consumption, extending tool life, and improving the surface finish of the generated surface. ISCAR has developed vibration-damping solutions that use various principles. These include vibration damping through specially designed mechanisms, such as in boring bars (Fig. 2), as well as the development of specific chatter-resistant cutting geometries. The geometry incorporates variable helix and unequal angular pitch in multi-flute solid carbide endmills and heads, along with a serrated cutting edge for effective chip splitting action in indexable inserts (Fig. 3). Additionally, these tools and inserts ensure better chip handling, which enhances the performance of machining operations. The smart design of the pocket reducer allows mounting smaller size inserts, which provides the option of extending the use of existing tool bodies instead of purchasing new ones. This not only reduces the waste of raw materials but also helps decrease GHG emissions.
Additive manufacturing (AM) has introduced new sustainability features in tool design. Firstly, AM technologies enable the production of a tool body that closely resembles its final shape, minimizing the need for finish machining and significantly reducing tool material consumption. Additionally, these technologies make it easier to create inner coolant channels in an optimal manner, improving the coolant flow through the tool body to the cutting zone.
The examples featured in this article illustrate how energy- and material-efficient, durable cutting tools can have a significant impact on technological sustainability. Such tools not only help reduce energy consumption and waste, but also contribute to cost savings and environmental stewardship.