According to The Global Wind Energy Council2020 was, the second- highest year for Offshore Wind installations globally, following a record year in 2019. This underscores the global focus and investment in implementing clean energy policies and technologies. Looking at Europe, especially Spain, Portugal, England, France, Denmark, and other coastal countries, we experience numerous offshore wind energy farms. More recently, the coasts of the United States and Canada, are creating a tremendous opportunity for the monopile and floating fabricators who are not afraid to take on massive new projects and invest in solutions to streamline the manufacturing processes.
Gigantic monopiles and Floating Foundations
Double XL monopiles are forecast to measure 15 meters in diameter in lengths up to 120 meters, weighing approximately 4,000 tons. Monopiles of this size and gigantic floating foundations are going to be a reality in the next five years.Floating foundations are capable of being anchored in deep water and conceptualized in several different designs depending on water depth and weather conditions. One of the biggest challenges in enlarging floating foundations is finding the right design and material that can handle those heavy weights and large-diameter Offshore Wind Towers.
Inrotech has developed solutions for automatic welding of joints in heavy steel plates, which is used in many offshore applications.
When it comes to floating foundations, the sheer size of these does not allow manufacturing methods, which are traditional within off-shore industry, to be used.
Inrotech’s mobile welding solutions are optimal for the welding of these very large structures, both in the part fabrication as well (and especially) in the final assembly of the large components.
The only solution to Inrotech’s mobile robot welding solutions will in this context most likely be restricted to manual or semimanual welding (using a manually operated tractor).
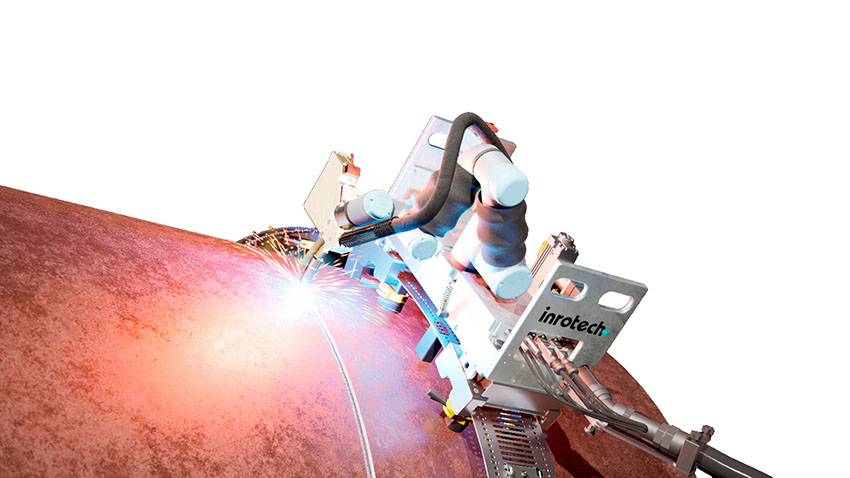
Instead of using large gantries with large robots, operating in dedicated production areas, where these large components are transported, Inrotech’s combination of mobile welding robots offers several advantages to these traditional gantry-based solutions; lower cost, less transport of floating structures and flexibility to move to different applications or working areas.
Recently, this has aroused great interest from various stakeholders, wind manufacturers, design houses, among many others. The interest in Inrotech’s welding robot is due to the fact that the robot breaks with all previous ways to use and operate welding robots in offshore wind industries.
Mobile welding robots for floating foundations
The INROTECH technology is providing a fully automated solution for parts previously thought only to be suitable for manual or semi-manual MAG. Rasmus Faudel, System & Software Manager of Inrotech explains and continue “we specialize in bringing the robot to the job, rather than the traditional method of bringing the job to the robot. This philosophy is the only way you can achieve automated welding on some of the very large structures we now see becoming a reality in many of the designs in floating wind industries.
The Inrotech solution offers a simple user interface which means that the operator only needs three to four keystrokes in order to operate the robot. There are no complicated programming codes, and the operator does not need to assign tasks to the robot manually nor monitor it.
Rasmus Faudel, System & Software Manager of Inrotech explains and continues: “we have manufactured several mobile welding robots, which is specifically designed to target complex welding jobs in offshore wind.
Three common designs of floating structures are spar, tension leg platform, and semisubmersible. These structures can be welded by combining different Inrotech solutions. The Inrotech-Vertigo is a portable platform with a robot installed on double vertical axis, capable of welding PF, V grooves. A tension leg platform can be welded by using the Inrotech-MicroTwin and the Inrotech-Classic. These solutions are normally used for shipbuilding purposes. Semi-submersible foundations are welded by using the Inrotech-Crawler, which is able to weld in various positions such as PA, PB, PC, PE, PF – V-Groove, Half-V-Groove and Tulip.
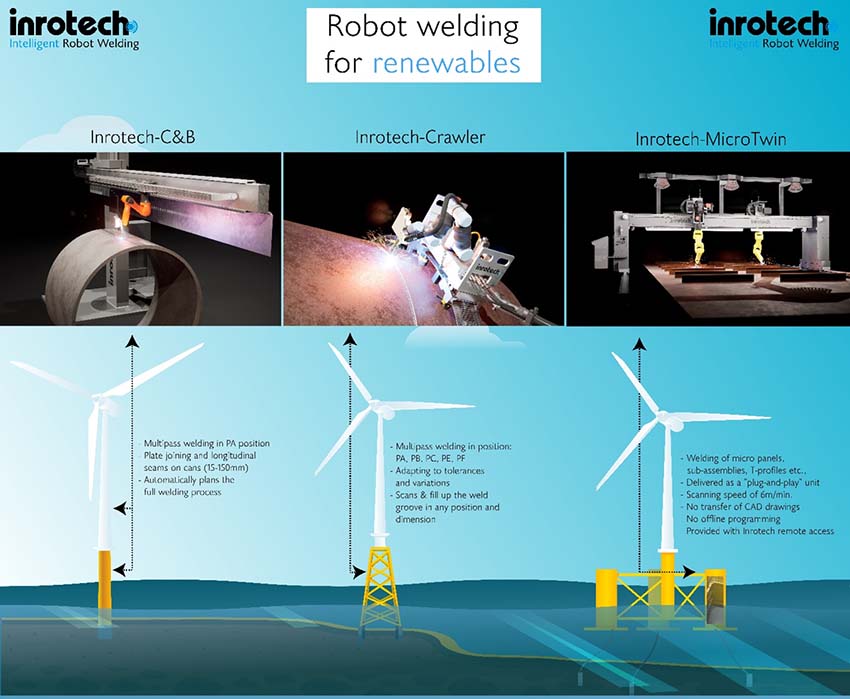
“Our close cooperation with offshore wind companies has shown us that there’s a demand in the market for automated welding solutions operating with big and complex structures where lack of space previously prevented the use of robotic welding. The operator also avoids working in narrow spaces that may impose a risk for their health and safety”, says Rasmus Faudel.
Fact: Inrotech delivers specialized and mobile robot solutions that:
- Is tailored to shipbuilding, offshore wind and heavy industries;
- Is innovative in mechanics, software and operations;
- Is easy to operate via an intuitive user interface;
- Can operate in impassable places;
- Is able to identify the subject, combine and scale the task as needed and thereafter weld according to established specifications;
- Minimizes costs for staff training, instruction and supervision.