Structural design plays a pivotal role in ensuring the safety, functionality, and longevity of our built environment. From towering skyscrapers to humble residential structures, every building project relies on the careful calculations and meticulous attention to detail of structural engineers. However, even the most experienced professionals can fall prey to common design errors that can have far-reaching consequences. Thankfully, specialized software solutions for structural design can streamline the process and minimize the risk of these errors.
In this article, we’ll delve into five of the most frequent pitfalls in structural design, exploring their causes and providing practical strategies for minimizing risk.
One of the most fundamental aspects of structural design is determining the loads that a structure will be subjected to over its lifetime. Underestimating these loads, whether dead loads (permanent weight), live loads (occupancy), wind, or seismic forces, can lead to a design that is unfit for its intended purpose.
Dead Loads: Dead loads encompass the weight of all the structural components themselves, along with permanent fixtures, finishes, and built-in equipment.
Live Loads: Live loads are variable, stemming from people, furniture, movable equipment, or stored materials. Building codes often specify minimum live load requirements based on the structure’s intended use.
Environmental Loads: Geographic location plays a critical role in environmental loads. Wind loads, dictating lateral and uplift forces, vary significantly based on regional wind speeds and your site’s exposure. Snow loads must be determined from ground snow load maps specific to your region. In earthquake-prone regions, seismic loads depend on site-specific hazard analysis and your structure’s dynamic properties.
Tips for Accurate Load Estimation
- Strictly Adhere to Codes: National or regional structural design codes, such as the Eurocodes or the American standards, provide comprehensive guidance on load calculations and combinations, with built-in safety factors.
- Use Reputable Data Sources: Obtain reliable wind and snow load data from sources aligned with your design code, such as ground snow load maps or wind speed contours. For seismic design, utilize regional seismic hazard maps to assess earthquake risks and determine appropriate design parameters. Your local building department or relevant government agencies can often direct you to these resources.
- Consider Dynamic Effects: Analyze if specific load cases will trigger vibrations or other dynamic behavior in your structure, especially for slender or long-span elements.
How SDC Verifier Help Prevent This Structural Design Error?
Specialized structural design software solutions streamlines load case generation. Its built-in generators, now including EN 13001 and Eurocode 0 standards, automate the calculation of different load combinations your structure must resist. This significantly reduces the risk of errors from manual calculations or misinterpreting the complexity of code-mandated combinations.
2. Incorrect Assumptions about Shapes and Material Behavior
The performance of a structural element depends not only on its material but also on the shape of its cross-section. Additionally, understanding how material properties translate to the behavior of the entire structure is equally crucial. Incorrectly assuming these factors can lead to a structure that is weaker or deforms more than intended.
Shape and Length Properties: A structural member’s resistance to bending, buckling, and deflection is heavily influenced by its shape (depth, width, cross-sectional area, etc.) and its length. Neglecting either aspect when simplifying models can lead to underestimated forces or deflections, compromising the design.
Modulus of Elasticity: This describes a material’s stiffness and plays a critical role in deflection calculations.
Long-Term Behavior: Materials may exhibit creep (gradual deformation under sustained load) or shrinkage (volume change due to moisture loss). Over time, these effects can significantly impact deflections and stresses, potentially leading to unexpected cracking or serviceability problems.
Environmental Sensitivity: Factors like temperature extremes, moisture, chemical exposure, or freeze-thaw cycles can degrade performance. Consider these during material selection and consider protective measures.
Tips for Managing Shape & Material Assumptions
- Accurate Modeling: Ensure your structural analysis model accurately reflects these crucial aspects:
- Material Properties: Correct modulus of elasticity, yield strength, and other parameters based on your chosen materials.
- Section Properties: Dimensions, thicknesses, moment of inertia, section modulus, etc. of beams, columns, plates, and other structural elements.
Refer to Reliable Standards: Codes, handbooks, and manufacturers provide:
- Material Properties: Strengths, allowable stress ranges, and long-term behavior data (e.g., creep coefficients for concrete)
- Section Properties: Tables for standard steel shapes, concrete dimensions, and engineered wood product specifications.
- Factor in Degradation: If environmental exposure is a concern, consider the long-term impact on material strength and factor that into your design where possible. Consider protective measures such as coatings, corrosion-resistant alloys, or increased section sizes to offset potential deterioration.
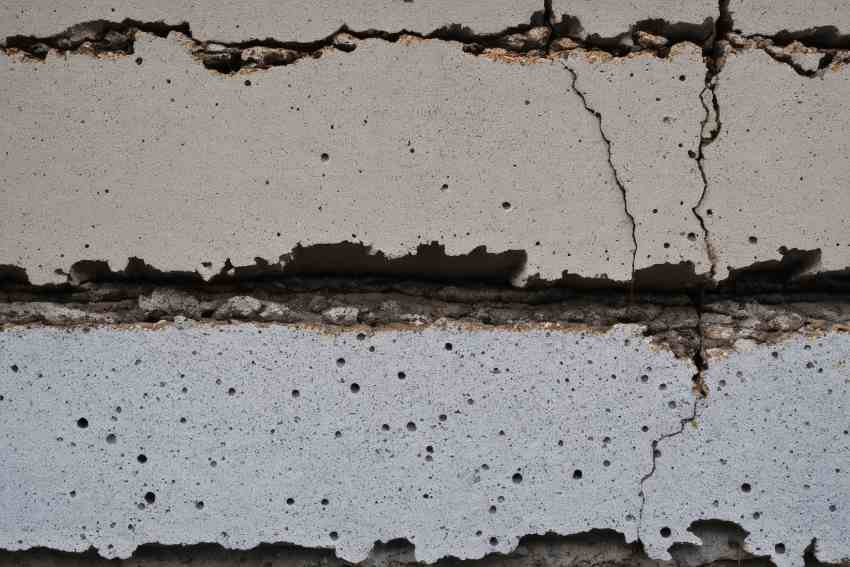
How SDC Verifier Help Prevent This Structural Design Error?
SDC Verifier’s analysis considers both material properties and the true shape of elements within your model. This helps avoid errors stemming from incorrect assumptions about material behavior, cross-sectional properties, or long-term performance changes.
3. Connection Detailing Oversights
Connections are where individual structural elements meet. Neglecting the proper design of joints, splices, and supports can generate critical weak points within the structure.
Force Flow Visualization: Before diving into connection design, mentally trace how forces distribute through your structure. Where do they change direction? Where are there points of high-stress concentration?
Stress Concentrations: Geometric changes, like bolt holes, abrupt transitions, or notches, amplify local stresses. Poorly detailed connections can create unintended ‘hot spots’ prone to failure, even if the bulk of the connected members are strong enough.
Common Connection Types
- Welded: Strong and rigid connections but require skilled labor and quality control during fabrication. Pre-qualification of welding procedures and inspections during construction are often necessary.
- Bolted: Versatile, allowing for field adjustments, but introducing stress concentrations at bolt holes. Poor weld quality in welded connections can also create significant stress concentrations.
- Hybrid (Welded + Bolts): Combines the strengths of both types for demanding connections. These often utilize shop-welded subassemblies combined with bolted field connections.
- Shear Connections: These connections are designed to primarily resist forces perpendicular to the connection axis. They can be bolted, welded, or employ other methods of force transfer. Simple shear tabs, slip-critical bolted connections, or a beam welded directly to a column flange are examples.
Tips for Robust Connection Design
- Leverage Industry Resources: Standard details and handbooks, offered by organizations like the American Institute of Steel Construction (AISC), provide a wealth of tested and proven solutions.
- Don’t Reinvent the Wheel: Adapt proven details to your project rather than starting from scratch whenever possible.
- Thorough Connection Analysis: SDC Verifier goes beyond simple member sizing. It rigorously analyzes connections, factoring in potential secondary effects and code-based capacity checks. These include:
- Eccentricity & Prying: Assesses connections subjected to loads with offsets, ensuring forces are transferred safely.
- Bolt & Weld Capacity: Verifies bolt strength (shear, tension) and weld sizes according to relevant codes (AISC 360, Eurocode 3, etc.).
- Member Capacity: Checks if connected beams, columns, etc., can handle the forces at the joint.
- Stability & Buckling: Examines potential buckling of connection components (gusset plates, web stiffeners).
- Fatigue (Optional): If applicable, specialized modules assess susceptibility to fatigue cracking.
- Consult with Detailers: Experienced steel detailers or connection specialists can be invaluable partners during the design process, bringing practical knowledge to ensure your ideas are constructive.
How SDC Verifier Help Prevent This Structural Design Error?
SDC Verifier goes beyond simple member sizing. It thoroughly analyzes connection forces to identify potential issues like overstressed bolts (by AISC 360, Eurocode 3, or similar), insufficient weld sizes, or instability within joints. This enables the optimization of connection designs for greater safety and efficiency, ensuring adherence to industry-recognized standards.
4. Stability and Buckling Neglect
Tall, slender elements or large spanning members are susceptible to instability and buckling failures. These occur when structures undergo sudden and dramatic changes in shape under relatively small load increases, often defying simple understrength calculations.
The Physics of Buckling: Buckling isn’t primarily about material failure but about geometry. A slender member can abruptly bow sideways or twist even if the material itself hasn’t reached its capacity. Imagine a ruler standing on end it can support some weight but easily snaps sideways if even slightly perturbed.
Visualizing the Risk: Identify slender columns, long-span beams, or thin plates within your design, as these are more buckling-prone. Think of a thin-walled soda can – it can support some vertical weight, but easily crumples with a modest squeeze.
Tips for Preventing Buckling Failures
- Know Your Weaknesses: Pay close attention to elements with high slenderness ratios. Effective length factors, determined by support conditions, are crucial.
- Bracing Strategies: Lateral bracing can turn a slender column into a series of shorter, more stable segments. Think of the stiffening in truss members or diagonal bracing in walls.
- Choose Stable Shapes: Wide-flange beams are more resistant to lateral-torsional buckling than narrow rectangular sections. Box sections are inherently better than open channels in resisting torsional buckling.
- Software is Your Ally: Buckling calculations are often more complex than simple strength checks. Analysis software can be highly beneficial in identifying and mitigating these risks.
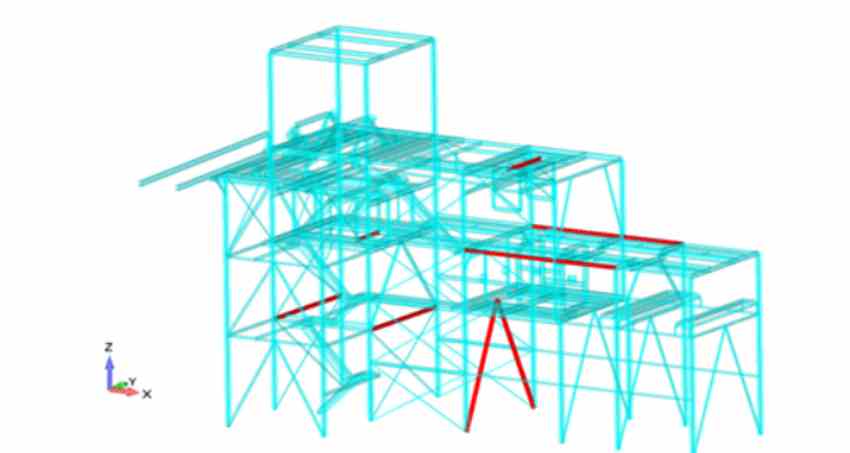
How SDC Verifier Help Prevent This Structural Design Error?
SDC Verifier excels in advanced buckling analysis, going beyond just columns. It performs Euler buckling checks for slender elements, lateral-torsional buckling assessments for beams, and even localized buckling analysis for plates. This allows you to pinpoint vulnerable members and proactively optimize bracing, shapes, or web stiffeners for improved stability and structural safety.
Structures subjected to repeated cycles of loading and unloading can experience fatigue damage, potentially leading to premature failure even at stress levels far below their ultimate strength. This is especially critical for bridges, machinery supports, crane rails, and other components exposed to dynamic effects.
Fatigue Considerations:
- Variable Loading: Identify structural elements or connections subjected to fluctuating loads from traffic, equipment, or environmental factors. Assess the magnitude and frequency of these cyclic load variations.
- Material Sensitivity: Steel, aluminum, and even concrete exhibit fatigue behavior. Refer to design codes and material-specific fatigue design guidelines for allowable stress limits and reduction factors.
- Connection Details: Welded and bolted connections can be particularly prone to fatigue cracks due to stress concentrations. Utilize fatigue-resistant detailing practices whenever possible.
- Specialized Analysis: Structural analysis software often includes fatigue assessment modules. These tools help analyze stress fluctuations, estimate fatigue life (cycles to failure), and identify fatigue-critical areas within your design.
- Constructive Detailing: Minimize stress risers through smooth transitions, generous weld profiles, and carefully detailed connections. Consider improved materials (higher strength steels) for fatigue-sensitive zones.
- Inspection & Maintenance: Incorporate a plan for regular inspection and maintenance of fatigue-prone elements for early detection and repair of cracks or signs of deterioration.
How SDC Verifier Help Prevent This Structural Design Error?
Advanced structural analysis software often includes fatigue evaluation tools. These automate much of the complex calculations involved in fatigue design, allowing you to optimize details, explore material choices, and predict service life with more confidence.
Structural design is a complex discipline where seemingly small errors can have significant consequences. By understanding common pitfalls, adhering to established codes, and utilizing advanced analysis tools, engineers can design structures that are safe, efficient, and built to last.
Software solutions, like SDC Verifier, streamline the design process and catch potential errors early. They perform rigorous code-compliant calculations, analyze connections in detail, assess buckling risks, and even evaluate fatigue life. This allows engineers to focus on innovative and efficient solutions, knowing the fundamental checks have been covered by a robust software solution for structural design.