Interflow was founded in 1974 under the name Bos & Eelman. In 1983, the name Interflow was introduced. Interflow is an independent company within the BAM Specials division of the Royal BAM Group. Interflow has its own production facility and office located in Wieringerwerf in North Holland. the company is one of the top 3 players in the Benelux in the area of construction, maintenance and validation of cleanrooms, operating rooms and Laminar Air Flow units.
What is a cleanroom?
For the application in pharmacy or medical research Contamination Control focuses on the prevention of contamination by viruses or bacteria. This protects both the patient, the product and the employees. An operating room is type of cleanroom. For the application in the High-Tech sector and the Semiconductor industry (microchips) it is mainly about counteracting (polluting) particles, such as dust particles. The last application is to protect the product.
In a cleanroom there are specific conditions of temperature, humidity and pressure. For example, an operating room is usually pressurized to prevent contamination from the outside. Low humidity can lead to static (dis) charge, high humidity can lead to corrosion or mold growth. In the High-Tech industry temperature is of great importance with regard to the expansion and contraction of parts in an environment where one is working on technology of nanometers. The filtration and number of changes of air in the room also determines the level of classification.
Sustainability
The technology behind the cleanroom is also subject to sustainability. The continuous conditioning and circulating the air costs a lot of energy for cooling, heating, dehumidification and ventilation. In the field of “energetic sustainability” cleanroom builder Interflow some time ago opted for gas-free solutions for cooling and heating by means of an “all electric” heat pump for cleanrooms and operating rooms. Currently, there is a growing demand for a sustainable, Breeam / LEED-certified cleanroom. Next to energy usage, sustainability also affects the choice of material, the CO2 footprint of the entire chain and the possible reuse of material. Interflow already designs its products with the Total Cost of Ownership in mind, in other words, the costs over the lifecycle. That Cost of Ownership is therefore no longer just about money, but also about “cost for our planet”. For the Laminar Air Flow unit, smart solutions can also be devised, which further reduce energy consumption. Thanks to intensive contact with users of the units, solutions sometimes seem obvious. For example, in Interflow’s latest type of flow unit (the so-called “Safe Change”) a few minor changes have been implemented which not only lead to 30% energy savings but also the most silent product of its kind. So energy savings and comfort improve together.
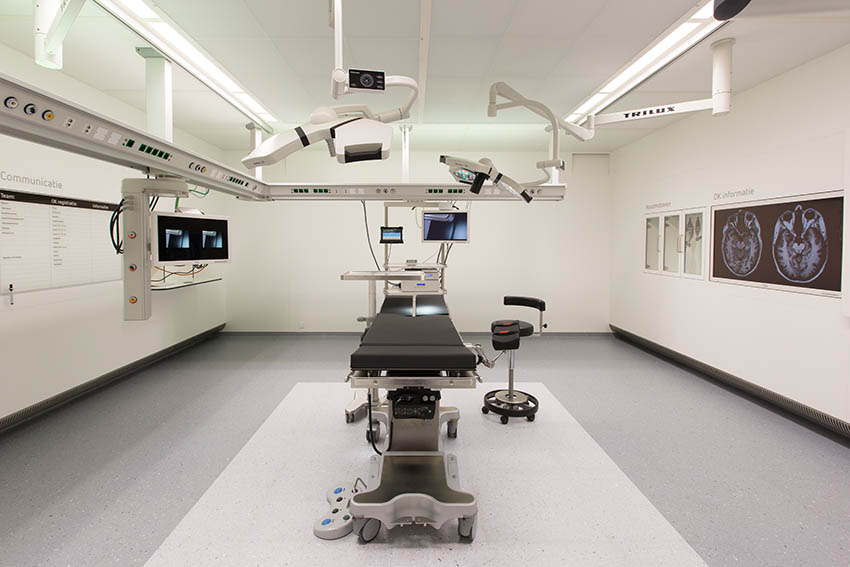
Digitization
Digitization is a big topic in every industry. So also in the world of cleanrooms and operating rooms. Digitization is about valuable data or communication for the user and on the other hand about smarter and more efficient design and production. In today’s operating room, there is a rapid development of technology used and we see a growth of “robotization”. To keep up with that development, you also want to be able to adapt the operating room quickly, without major renovations. That saves money and keeps the operating room available to a maximum. Interflow has invented the so-called “Flex-OK” solution. In the hollow wall of the operating room, a kind of interchangeable drawers or cassettes are placed with adaptable data connections. The airtightness of the operating room remains guaranteed, but the equipment can be replaced quickly and cleanly. Interflow has a complete working and validated “Flex-OR” at their location in Wieringerwerf. This enables them to test new innovative concepts directly in a real validated OR environment.
Digitalization also plays a role in the design process and in the validation of cleanrooms, operating rooms and the Laminar Air Flow units. Earlier this year Interflow and Actiflow jointly published the outcome of their validation research through simulation of air flows in Computational Fluid Dynamics (CFD). These tools are also used in the world of aerodynamics in aircraft and car design. Thanks to the simulation, a design can already be tested virtually in advance, allowing the operation and classification of chosen solutions can be guaranteed in the design phase. On one hand, this saves costs and time, but also provides flexibility to develop and test new innovative concepts during the design phase.
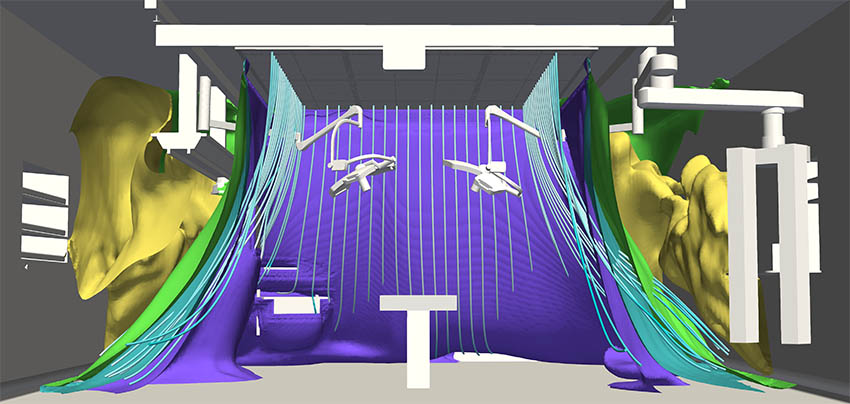
Standardization, Circular & Modular
By applying a standard library of solutions (at Interflow they refer to them as their “Lego blocks”), an initial design for a cleanroom is quickly made. Interflow has been building cleanrooms based on this standardized approach. The advantage of this approach is that cleanroom components are manufactured to size in advance and they can be assembled in a clean way on site. Another advantage of this standardization is the flexibility into the future. The construction of the cleanroom can be modified with a relatively simple conversion. The walls can also be more easily reused, an important advantage with the circularity perspective. Interflow is currently developing a circular concept with a take-back guarantee of used cleanroom wall panels. It is expected that this circular concept can be introduced to the market in 2023.
Currently, Interflow sees an increasing demand for modular cleanrooms that can be quickly built, are portable, but can also be expanded or downsized quickly. In collaboration with a major customer, Interflow has already installed examples at locations outside the Netherlands. The modular concept allows Interflow to build a cleanroom in a very short time frame at any suitable location, inside and outside the Netherlands. Modular flexibility in this case means that the architectural construction and the HVAC systems are linked together. Simply put: if we want to make the cleanroom larger by 2 modules in width, then automatically the HVAC solution will be proportionally larger. The modular concept is very attractive for companies with a rapidly growing demand, temporary demand or still uncertain demand for cleanroom space.
An interesting variant of the modular cleanroom is the temporary expansion of the pharmacy of Leeuwarden Medical Centre, which Interflow is currently installing together with its partner Q-bital. The assembled modules, containing the prefabricated cleanroom, form a robust stand-alone building.
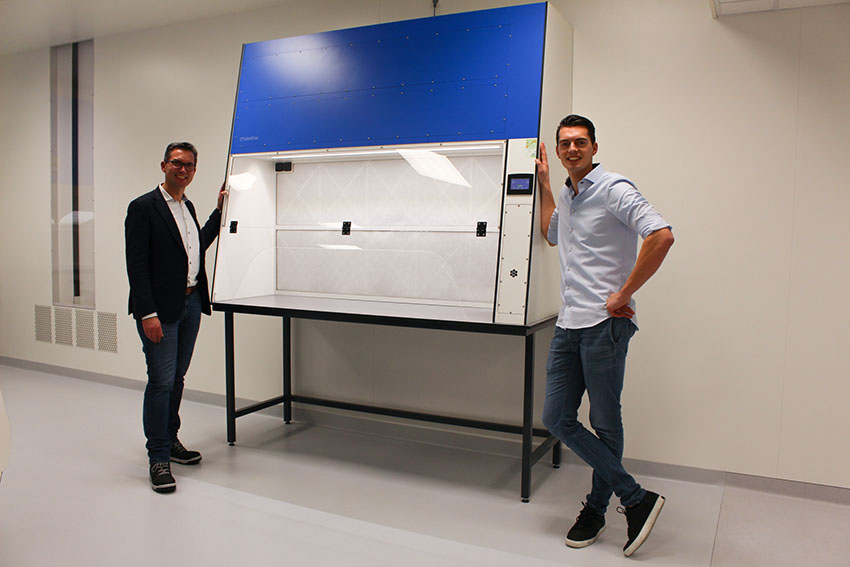
New business models
In 2022, Interflow also introduced new services for their customers. For example, since this year, with the help of their partner De Lage Landen (DLL), a financial lease can be taken out for the purchase of Laminar Air Flow units. In addition, Interflow just contracted the aforementioned modular cleanroom solution for the first time in a rental concept. Thanks to this concept, customers of Interflow can for example continue their operations in the temporary modular cleanroom, during an expansion of the existing cleanroom. But also for a quick expansion of production capacity the rental concept can offer a solution, until a permanent expansion has been realized. From the rental concept, it is a small step to the “Cleanroom as a Service”.