Element Logic has been optimizing warehouse performance for more than 30 years. The company’s core competence is the planning and implementation of tailor-made warehouse solutions that enable customers to meet the increasingly complex requirements and dynamics of today`s markets. Being the world`s first, AutoStore® partner with 130 systems supplied all over Europe, they have a wealth of experience designing, delivering, and installing state-of-the-art solutions that improve our customers’ workflow and profitability. Their customers include companies from a wide variety of industries and sizes, from start-ups to listed corporations.
Element Logic has about 200 employees in Europe and had a turnover of more than 100 million € in 2020. Being headquartered in Norway, the company is locally present with subsidiaries all over Europe – also in the Czech Republic and in Poland.
Interview with Joachim Kieninger, Director Strategic Business Development at Element Logic Germany.
Learn more about Element Logic and their solutions in the video below:
Easy Engineering: Which are the most digitalized products / solutions?
Joachim Kieninger: Being a one-stop-shop for warehouse automation, our portfolio includes automatic storage systems, robotic solutions, conveyor technology and additional material flow handling systems, warehouse management software, design and consulting, as well as service and support, including remote maintenance.
E.E: What are the characteristics of these products / solutions?
J.K: Digital information and data are the foundation of all our products. In all our warehouse solutions product identification is digitized, e.g. by barcodes as part of the goods-in and picking process. Customer orders are usually received as digital data. These data are then transferred into tasks that are processed by the automated systems.
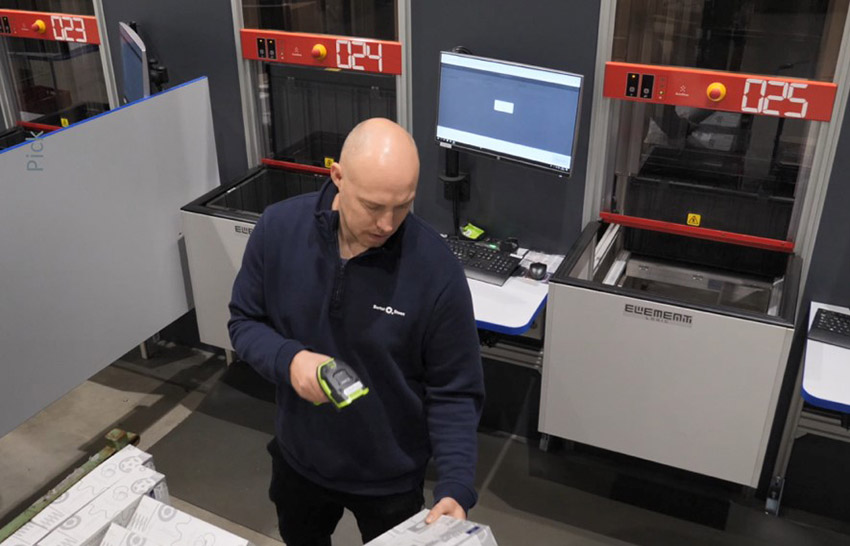
E.E: What are the benefits for the users?
J.K: The main benefits for the users within a warehouse are simplification of processes, improvement of customer services, e.g. remote maintenance, and transparency about in-house logistics operations. Customers will benefit from faster order processing and higher accuracy, close to zero picking errors.
See what our customers say in these videos:
New Wave:
EET Group:
E.E: In what type of projects are they used?
J.K: Our products and solutions can be used wherever items smaller than a full carton are stored and picked. Even full cartons up to 600×400 can be stored in an AutoStore bin. The variety of our customers is endless. We have implemented solutions within fashion, pharma, electronics, e-grocery, spare parts and many more branches. Recently, we installed several systems for 3PL companies. Automation helps to increase process and storage transparency, reliability, speed and therefore reduce cost, independent of the company`s size.
E.E: Do you plan to implement digitalization in other products / solutions?
J.K: We also have solutions for automatic carton and tote transport, either by conveyors or by AMRs, as well as automatic piece-picking solutions. In the future even more data will be collected, especially in respect of service and maintenance of technical equipment. Preventive maintenance will turn into predictive maintenance to bring uptime and availability even closer to 100 %. The main benefits for the users will be increased system availability and lower maintenance cost.
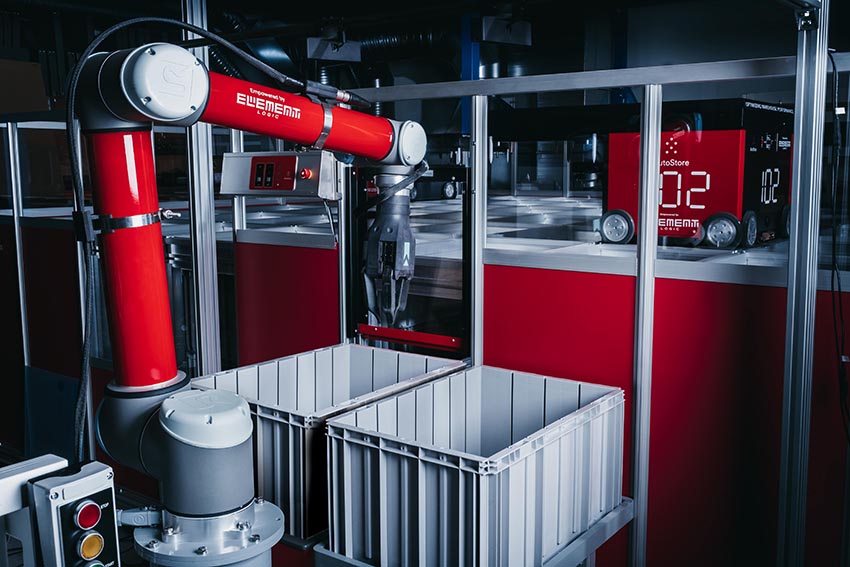
E.E: How important is digitalization in your field?
J.K: Without digitalization, automatic storage and retrieval, but also automatic picking and automatic transport is not possible. Data exchange and collection is crucial for this kind of technology. It increases speed and accuracy, leading to significant cost reductions.
E.E: In which directions do you think digitalization is heading towards?
J.K: We see the trend that customers demand and expect faster and better deliveries for all kind of orders. Warehouses are therefore moving closer to urban areas, and since ground space is limited, storage needs to be more dense and therefore automated. These Micro-Fulfillment-Centers are pick-up points for the customers or for last mile logistics providers. Element Logic is also providing solutions for Micro-Fulfillment-Centers.
E.E: What was the employee feedback regarding the digitalization process?
J.K: Our experience is, that the employees are satisfied with the new working environment.
Long distance walkways are no longer necessary, and the workstations are ergonomically optimized. The workflow becomes less complex. Electronic equipment like touchscreens is used to exchange information in a structured way instead of using paper and pen, what we still find in some warehouses.
E.E: What industries do you think will be more digitalized in the future?
J.K: In the warehouse optimization-business, more and more smaller companies will also automate and therefore digitalize their processes. Another area are stores where shelves will either be digitalized by electronic pricing or replaced by automatic storages as part of the store, where customers can pick up their orders that they placed via app from home or in an exhibition store.
E.E: Did the current situation made your company implement digitalization sooner than predicted?
J.K: Yes, the demand for digitalization and automation is further increasing, especially in warehouse automation. On the one hand to be able to store more products and more volume on the same footprint, and on the other hand to have more control regarding inventory and processes. Both have an immediate effect on customer satisfaction and loyalty.
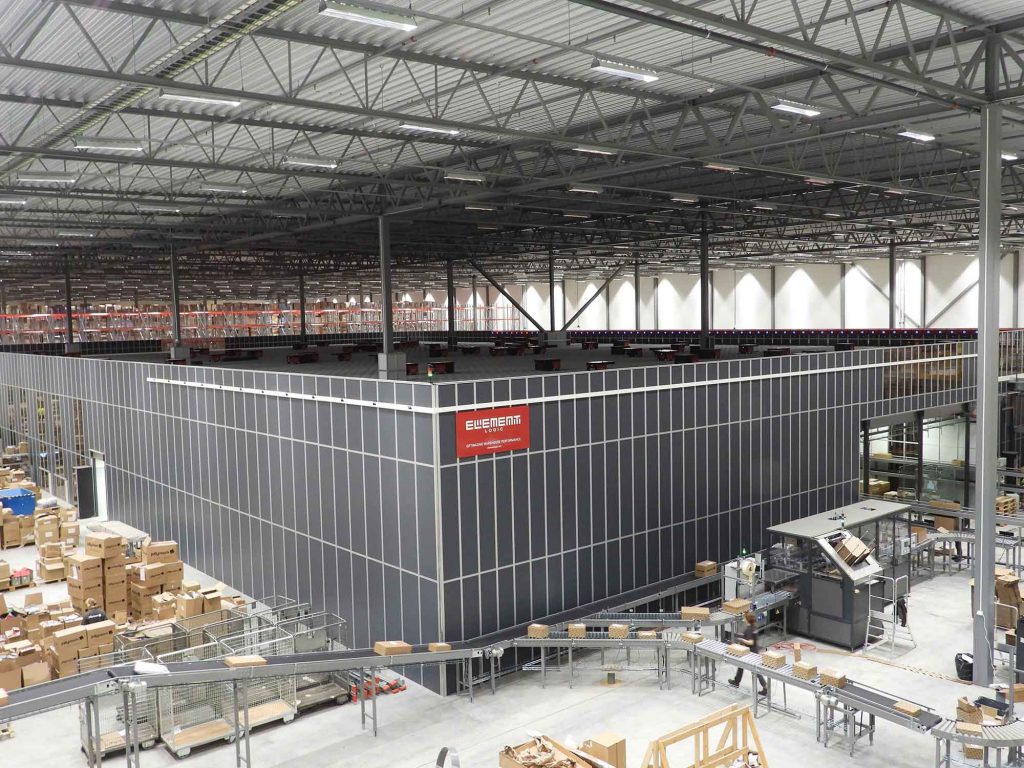
E.E: What are your forecasts for the first half of 2021?
J.K: The current situation will hopefully not accompany us into the second half of 2021. Nevertheless, supply chains around the world will be further digitalized and this also includes warehouse processes. Hence digitalization and automation will continue and will be more and more part of our daily life.
Mail: joachim.kieninger@elementlogic.de
Phone: +49 7136 2704980
Mobile: +49 151 53640898