Amsterdam IJmuiden Offshore Ports (AYOP) is an active association representing over 120 companies, regional governments and research/education institutes active in offshore oil & gas and wind energy in the North Sea Canal region.
Members have a strong focus on offshore wind maintenance (including cable logistics), drilling projects for gas extraction, changes to and maintenance of work vessels and platforms, and the disassembly of offshore structures and vessels. In addition, our association accommodates logistic services providers, HR companies and facility services providers such as caterers and hotels, allowing us to represent the entire offshore chain.
DecomMissionBlue is a partnership between various Amsterdam Ijmuiden Offshore Ports members (AYOP). They have a shared ambition to realize the efficient, fast and, crucially, sustainable decommissioning and recycling of offshore installations and large maritime objects.
Hundreds of objects and installations at sea, varying from platforms to vessels and wind turbines, will reach the end of their lifespan in the coming decades. With a history of exploring new worlds and possibilities, The Amsterdam-IJmuiden region is ready to play its part, with DecomMissionBlue actively taking on the challenge of finding increasingly smart, efficient and sustainable ways to decommission and recycle large maritime objects and installations. The ultimate goal is a cleaner North Sea.
Situated behind the world’s largest sea lock, the brand-new yard is equipped to work tidal-free and time-efficient. In addition to the ideal geographical location in relation to the North Sea, the company is able to process all parts and materials within a radius of 10 miles.
DecomMissionBlue is renowned for the exceptional way its partners reinforce each other with their diverse expertise, disciplines, experience and perspectives. Together BK Ingenieurs, Boskalis Nederland, Building Careers, Koole Contractors/Decom Amsterdam, Mammoet, Port of Amsterdam, Reym, Seafox, Tata Steel and VLZS cover the complete value chain.
Interview with Sylvia Boer, Director of Amsterdam Ijmuiden Offshore Ports (AYOP).
Easy Engineering: What are the main areas of activity of the company?
Sylvia Boer: DecomMissionBlue is committed to a cleaner North Sea and is the answer to decommissioning and recycling offshore & large maritime objects in innovative and sustainable ways. We work closely with our partners to tackle the growing challenge of dismantling and recycling offshore installations such as platforms and wind turbines, and offshore vessels, in a fast and effective manner.
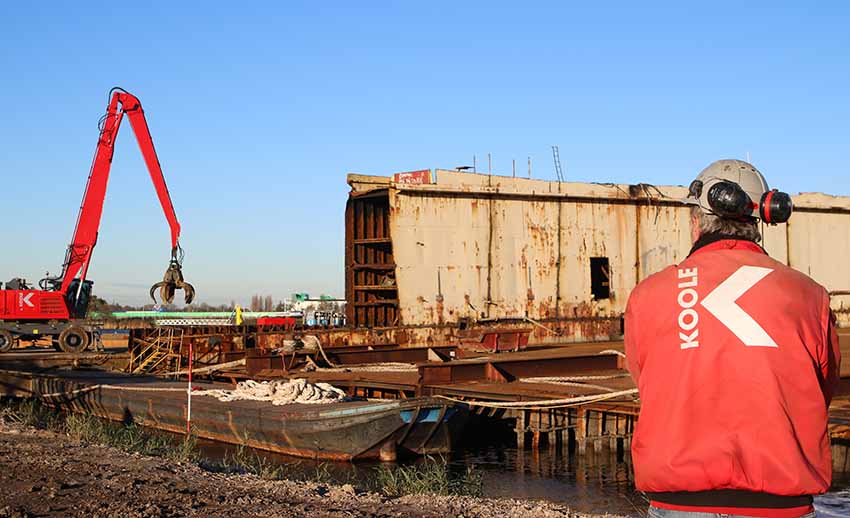
With our network-based approach, we accept each decommissioning challenge by combining 5 different perspectives, representing the key objectives of the Amsterdam IJmuiden Region:
Local
With the yard’s central location and the complementary expertise of its different partners, DecomMissionBlue can decommission and process all materials within a radius of 10 miles, thus minimizing emissions and the ecological footprint of the process.
The long offshore heritage of the region means that local industry and local players know each other well, forming a strong network that often cooperates on (decommissioning) projects.
Circular
Building a circular economy is an important objective of the Amsterdam IJmuiden region. Recycling materials and re-using resources is therefore key to each decommissioning project.
Contaminated objects are cleaned for reuse or recycled. Steel can be recycled by Tata Steel, oil and fats are recycled for re-use as biofuels while demolition waste such as wood, paper, rubble and plastic are separated for 90% re-use.
Smart
DecomMissionBlue is focused on the future and is part of the entrepreneurial ecosystem of the Amsterdam IJmuiden region. Continuously expanding its infrastructure and facilities to stimulate and support innovative new solutions.
Automating processes – by using a cutting robot, for instance – helps accelerate lead times, as does the use of the latest cleaning techniques. Rainwater can be collected to use for cleaning purposes while wastewater can be treated and re-used.
Efficient
DecomMissionBlue’s unique collaboration of perfectly aligned, specialized partners working closely and directly together results in customized time and cost-efficient decommissioning solutions. Coordinated by a single point of contact, managing all the certifications, safety and quality requirements in the decommissioning industry.
Transportation over water by ships allows larger volumes to be moved at once, which is more efficient in terms of time as well as the environment. The automatization of processes also saves time and – by minimising waste – materials.
Sustainable
By combining perspectives and expertise, DecomMissionBlue actively and continuously challenges itself to produce innovative new solutions and seek more sustainable ways to decommission. By sharing knowledge and learning from each other’s experiences.
With around 1000 tones transported in each shipment, vessels can carry far higher volumes of materials than trucks, leading to significantly lower CO2 emissions. Moreover, by filtering the waste released during decommissioning, mercury and radioactive substances can be separated from the liquid fraction to reduce mercury and radioactive residue levels.
S.B: What’s new is the market of decommissioning are the offshore wind parks that will be decommissioned in the near future. The first wind parks that were installed at sea are reaching the end of the economic lifespan and they need to be dismantled in a sustainable manner. The first one in Holland will be the Prinses Amaliawindpark from Eneco, 23 km off the coast of Ijmuiden.
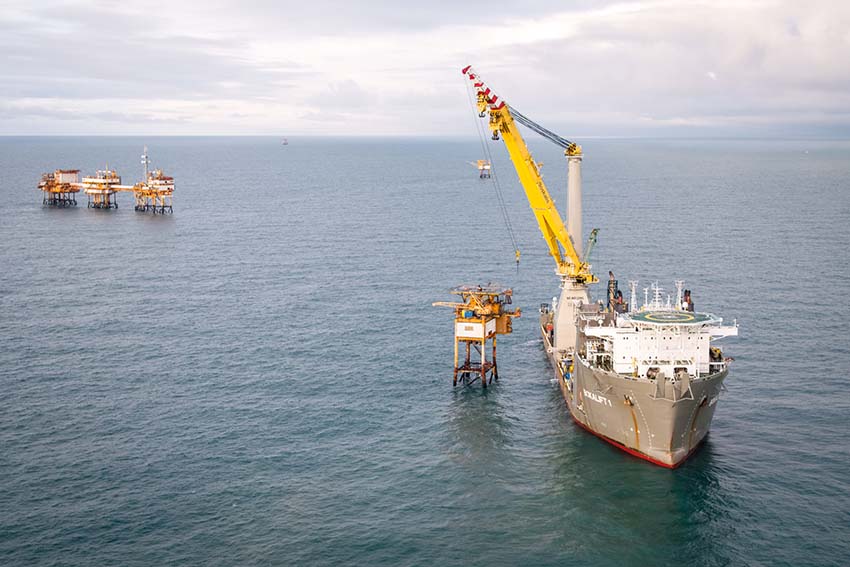
E.E: What are the ranges of products?
S.B: The range of DecomMissionBlue covers: platforms (including underwater infrastructure), wind turbines and electrical infrastructure, ships and data & electricity cables.
The yard is sixteen hectares in size and has its own quay suitable for mooring vessels with a draft of up to nine metres and length of up to 150 metres. The plan is that vessels will be dismantled on the right side of the premises, while the left will be accommodating oil and gas platforms.
E.E: At what stage is the market where you are currently active?
S.B: The decommissioning of platforms can be considered as a mature market. We have been doing this for many years now, the same goes for ships. However, decommissioning of wind parks is a new and upcoming market for which we still have a lot to learn and discover. For example, on how we are going to recycle them? And what is the most efficient way to remove the windmill from the seabed?
E.E: What can you tell us about market trends?
S.B: Whatever you put into the sea has to be cleaned up eventually. Oil & gas producers know they will have to dismantle their old platforms in the North Sea once they no longer have any economic value. Decommissioning has slipped down the to-do list for years, however, and the war in Ukraine has pushed it even further down the line. Because if there is even a little bit of oil or gas left in the field, restarting the platform in these times of unprecedented energy prices could suddenly be interesting.
For years, a peak has been forecast in the number of decom projects. This was also reflected in the number of tenders issued by producers for this purpose; there seemed to be a bit of momentum. But that has all been re-shuffled again. Producers are delaying decommissioning due to the current high energy prices.
The geopolitical playing field will be permanently changed due to the Ukraine war as no one wants to be dependent on Russian gas anymore. We all want to become energy independent.
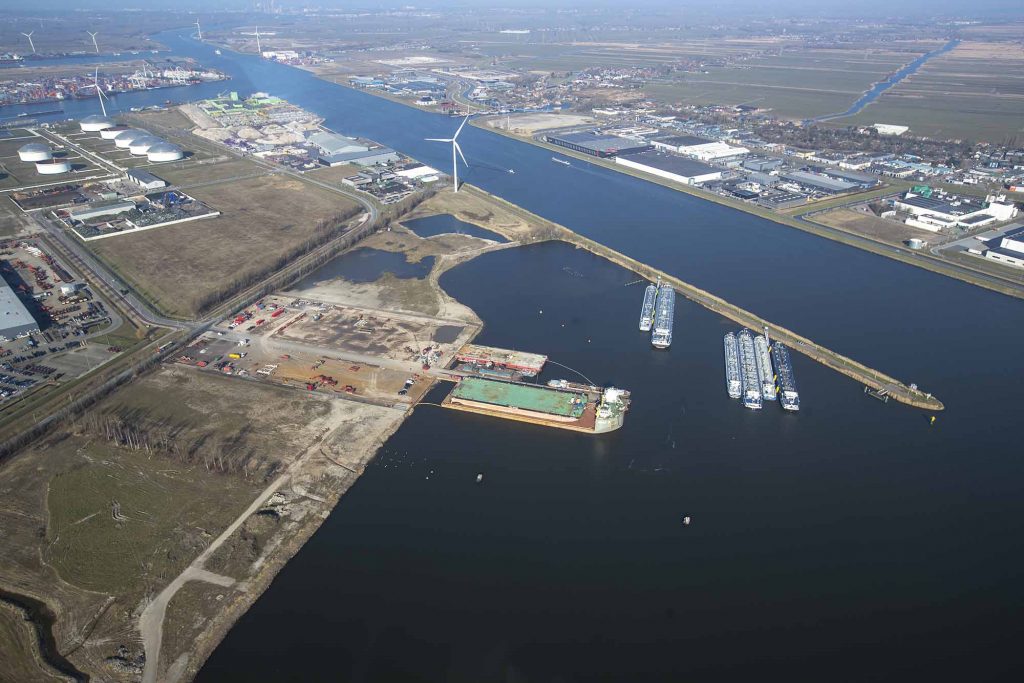
At the same time we see that the market for renewables is now extremely busy, especially with the ambitions of the Dutch government to install 21.5 GW offshore wind before 2030. The vessels used to install wind turbines are the same ones used for decommissioning assignments. The ships are mainly reserved for the renewables market.
E.E: What are the most innovative products marketed?
S.B: The fact that the decommissioning yard is situated behind the largest sea lock in the world, makes it that we are equipped to work non-tidal and save time. With an ideal geographical location in relation to the North Sea and the benefit of being able to process all parts and materials within a radius of 10 miles.