CEO Helmut De Roovere founded RoboJob in 2007, together with his former fellow student Luc De Ceuster. For three years, the two friends built an accessible automation for the automatic loading and unloading of CNC machines in the basement of De Roovere’s parental home.
In 2010, RoboJob’s first robot application was launched on the market, and the company quickly grew to become the international market leader in CNC Automation. Today, RoboJob has more than 800 installations at home and abroad. “Our goal has always been to make the job of the CNC operator attractive again. After all, our robots take over the physical, repetitive and often boring work, freeing up time for the more creative work. And, of course, our customers can significantly increase their yield, efficiency and also their flexibility.”, affirmed Helmut De Roovere, CEO RoboJob.
Easy Engineering: What are the main areas of activity of the company?
Helmut De Roovere: The core activities of RoboJob lie within the R&D Team, since all product development is done in-house. Mechanical Developers, Electrical Engineers and Software Specialists work together to build a product portfolio which currently consists of 15 standard products. Other main activities include the Assembly of these products, the Installation at home and abroad, and Service. A Sales Team is responsible for both Direct and Indirect Sales.
E.E: What’s the news for 2020 about new products?
H.D.R: No need to say that 2020 has been an exceptional year for RoboJob. The Covid-19 virus has hit hard in Belgium and Europe, but the RoboJob team has proven itself to be extremely flexible. The R&D Team has not stopped working and has continued to work on further developments for all products. Even though the Turn- and Mill-Assist products are already in their 3rd generation, RoboJob never ceases to further improve functionality, ease of use and efficiency.
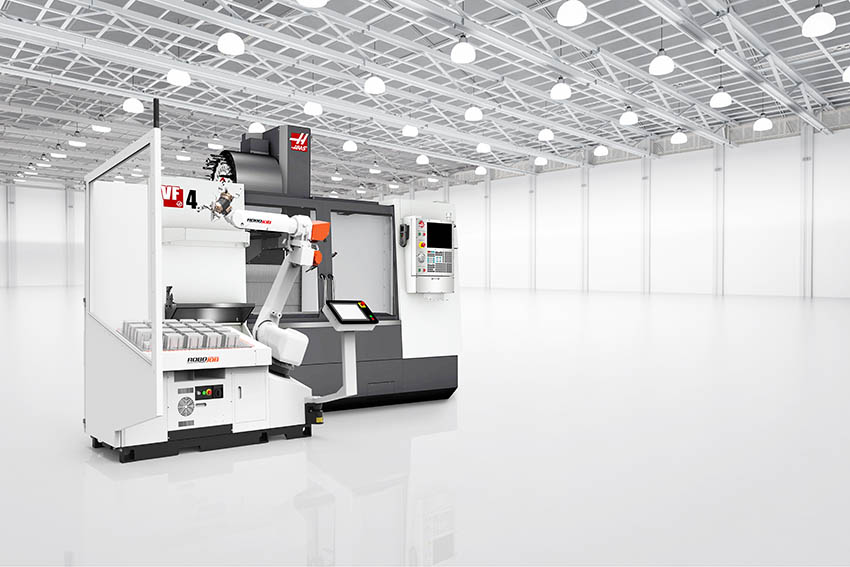
E.E: What are the ranges of traded products?
H.D.R: Today, RoboJob offers standard products which allow the automatic loading and unloading of CNC lathes and milling machines. These products can be divided into 4 categories:
- Turn-Assist Series: this automation enables the automation of CNC lathes. Workpieces of various sizes can be stacked on a configurable table from where a robot will position them in the lathe. Finished pieces will be put back onto the table.
- Mill-Assist Series: the same ‘table’ principle is applied, but for milling pieces.
- Racks: when workpieces cannot be stacked, or when batches are larger, the ‘Racks’ are a popular choice. Workpieces can be positioned in metal racks, which are stacked on top of each other.
- Tower: whereas all other product categories allow workpiece handling, the Tower offers more possibilities. Workpieces, but also pallets, clamping devices and tools can be stored in a 4,60m high Tower. An elevator system can bring each of the 28 drawers up and down to provide these to the robot.
E.E: At what stage is the market where you are currently active?
H.D.R: RoboJob is currently active in Western Europe and Australia. Every of the countries where RoboJob is active, is at a different stage of accepting the relatively new technology of CNC Automation. The most mature markets include the Benelux and Germany, where most systems are currently installed. Some markets are developing fast though, and the current health crisis seems to be a catalyst for further growth.
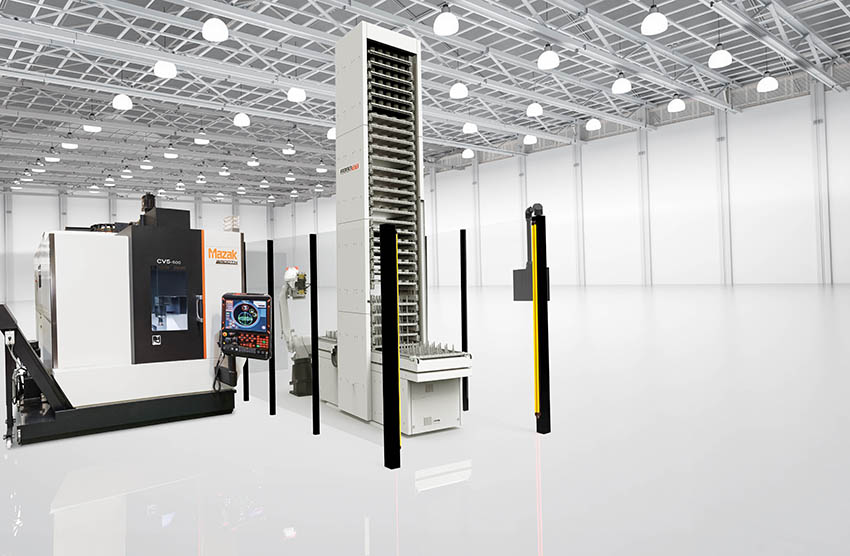
E.E: What can you tell us about market trends?
H.D.R: Manufacturing companies that are already working with automation are making full use of the fast and direct demand for mechanical components. Their people are ready and their machine park has been set up for that. “Many of our customers have called us out of the blue to tell us that automation has saved their business. We are enormously proud of this and we will tap into this spirit going forward in the post-Corona era.”. Companies who have not yet invested in the automation of their CNC machines, are currently investigating the possibilities. “We are receiving a very high number of requests from companies all over Europe and even beyond. It is clear that subcontractors, machine builders and all companies who use CNC machines in their production process want to make sure that they can continue their production when a virus strikes again.”.
E.E: What are the most innovative products marketed?
H.D.R: The RoboJob Tower is the product for the future. This automation can provide the customer with much more autonomy. Whereas a Turn-Assist, Mill-Assist or Racks can create machine autonomy for a few hours, the Tower can create unmanned production for several days. The Tower technology perfectly fits with Industry 4.0 principles to enable lean manufacturing with a digital character to continuously improve the process based on data.
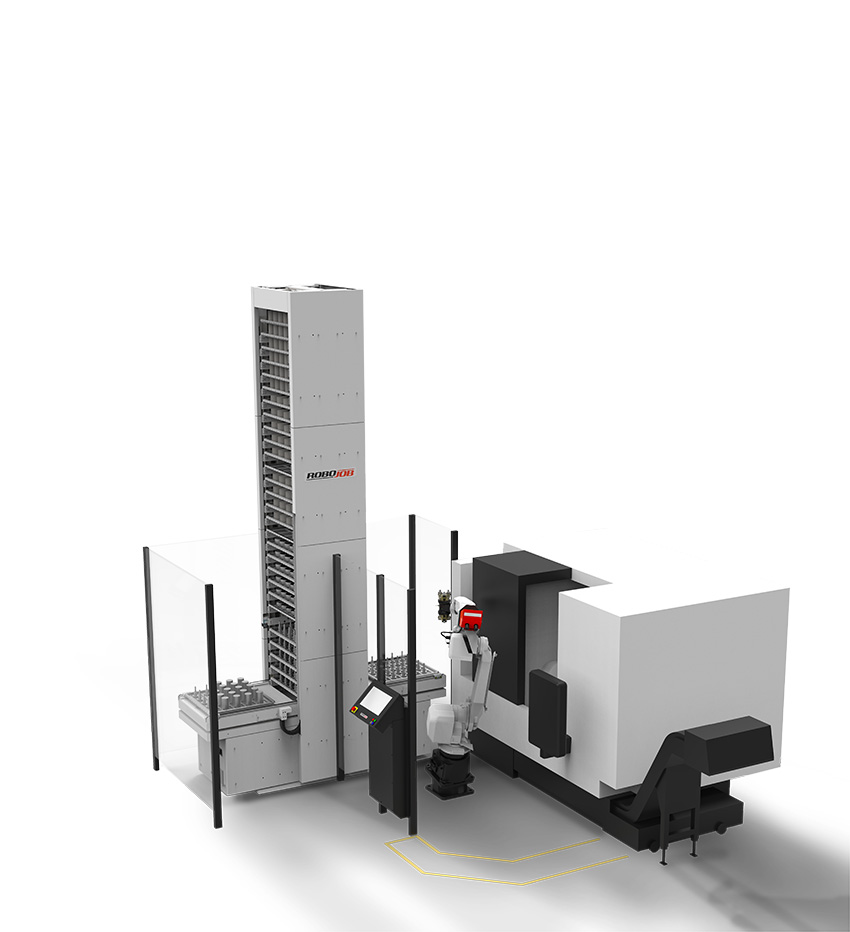
E.E: What estimations do you have for 2020?
H.D.R: 2020 will be a transition year: installations have been postponed due to closed borders and closed companies. On the other hand, RoboJob has never received this many requests from new customers all over Europe. Expectations are therefore that the speed of implementation will pick up in 2021.