Vivek Chinoy is the Marketing Director of Sigma CapSeal, a leading packaging machinery solutions provider. As an industry veteran, he has worked over two decades in multiple roles and handling business operations of various sizes. He has worked on packaging solutions for industries like Food, Pharma, Cosmetic & Chemical etc. whose products are available in markets of more than 80 countries.
He gets fascinated by distinct product packages in supermarkets and how they attract visitors to buy them among a host of other products. Offering innovative and automated solutions to clients worldwide remains his prime objective. Furthermore, he believes in adhering to safety standards to the core and offering the best customer support through the best use of technology.
Let’s take a look at his interview now.
Easy Engineering: A brief description of the company and activities.
Vivek Chinoy: Sigma CapSeal is a brand company of Electronics Devices Worldwide Pvt. Ltd. With over 45 years of industry experience, we are a leading packaging machinery solutions provider. We have our business presence in 85 countries, where a steady customer base of 30,000 loyal patrons trusts our solutions.
We have a range of packaging machinery solutions as part of our product range. These machines help industry-leading businesses to safeguard the quality of their products. Products also remain free of counterfeiting, tampering, and adulteration.
E.E: Tell us about your ranges of products.
V.C: Our product range comprises induction sealers and cap & closure automation machines. There are eight different machines in the induction sealer product range, which suit the needs of businesses of all sizes. The machines come with a maximum line speed of 100 feet per minute.
We also have three types of cap and closure automation machines. There is a flip-top cap closing machine, wad inserting machine/cap lining machine and Cap assembly machine. Industries like personal care, dairy, healthcare, F&B, specialty chemicals, and much more use our solutions.
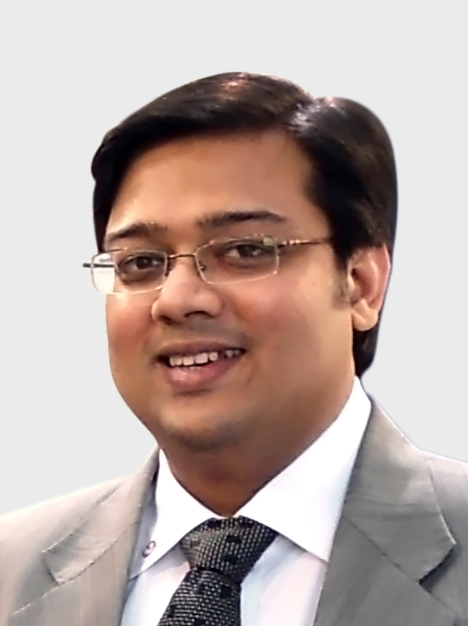
E.E: What special characteristics do your products have?
V.C: We have designed each of our machines after extensive research and development on the pain points of the industry. We always believe in innovation, which helps us deliver cutting-edge solutions to meet the changing demands of the industry. Keeping up with our tradition, we recently launched two new machines. These are Sigma Neo 65 Induction Sealer and Lotion Pump Assembly.
Sigma Neo 65 is an automatic induction sealer that comes with an IP 65 enclosure. It helps in protecting products from dust, oil, and water. Based on the size of the bottle and the cap, it can function with a maximum line speed of 12 meters per minute. It will fit into most production lines without any need for modifications. There are also inbuilt castors for improved mobility between production lines. It is best suited for products like tablets, coffee powder, and CBD powder.
The second latest machine is the Lotion Pump Assembly. It is an Industry 4.0 IoT product that allows the assembly of 12 components. Some of these include housing, liner, and spring in one machine. The machine has a part feeding and assembly arrangement. It will inspect all parts, and there is also a leakage test.
E.E: In what kind of projects are they used?
V.C: Our packaging machinery solutions find use across a range of industries. Businesses use them to package their products and improve shelf-life. Furthermore, it also helps them prevent product tampering and counterfeiting. Some industries using our machines are healthcare, personal care, dairy, FMCG, special chemicals, confectionery, plastic cap manufacturers and much more.
E.E: How do your products differ from others?
V.C: We have always believed in innovation when it is about designing our machines. Our research and development wing spends a lot of time in identifying solutions that not only solve the problem of today but also meet the demands of the future.
We had recently launched an innovative product in the induction sealing category. We have introduced an induction sealer with a universal head. Today, manufacturing businesses can stop worrying about the length of containers they wish to package. Our induction sealer with a universal head can accommodate containers with sizes of 35-150mm.
E.E: How are they used by your clients?
V.C: Our clients install these machines into their manufacturing plants. The machines work on the principle of any other machine in a manufacturing process with production lines. Products need to pass through the line where they get pushed into the machine for packaging. Once the packaging gets done, the products are ready to be packed and transported.
E.E: What kind of problems do your clients face on the job site?
V.C: Automation continues to be one of the biggest problems faced by this industry. The packaging industry, in many ways, is still to realize the true potential of automation. It gives us the chance to focus on this aspect when we design our new machines. We remain committed to innovation and will continue focusing on automation in our future products.
E.E: How do your products help them overcome these problems?
V.C: Our products are designed around solving the problem of automation. Keeping in mind our commitment, we recently launched an induction sealer with a universal head. Businesses no longer need to worry about having different sizes of caps for products. They can seal products with varying cap sizes at once. There is no need to change the sealing head. By doing so, we are able to save a lot of time for our clients. It directly translates to improved productivity and profit margins.
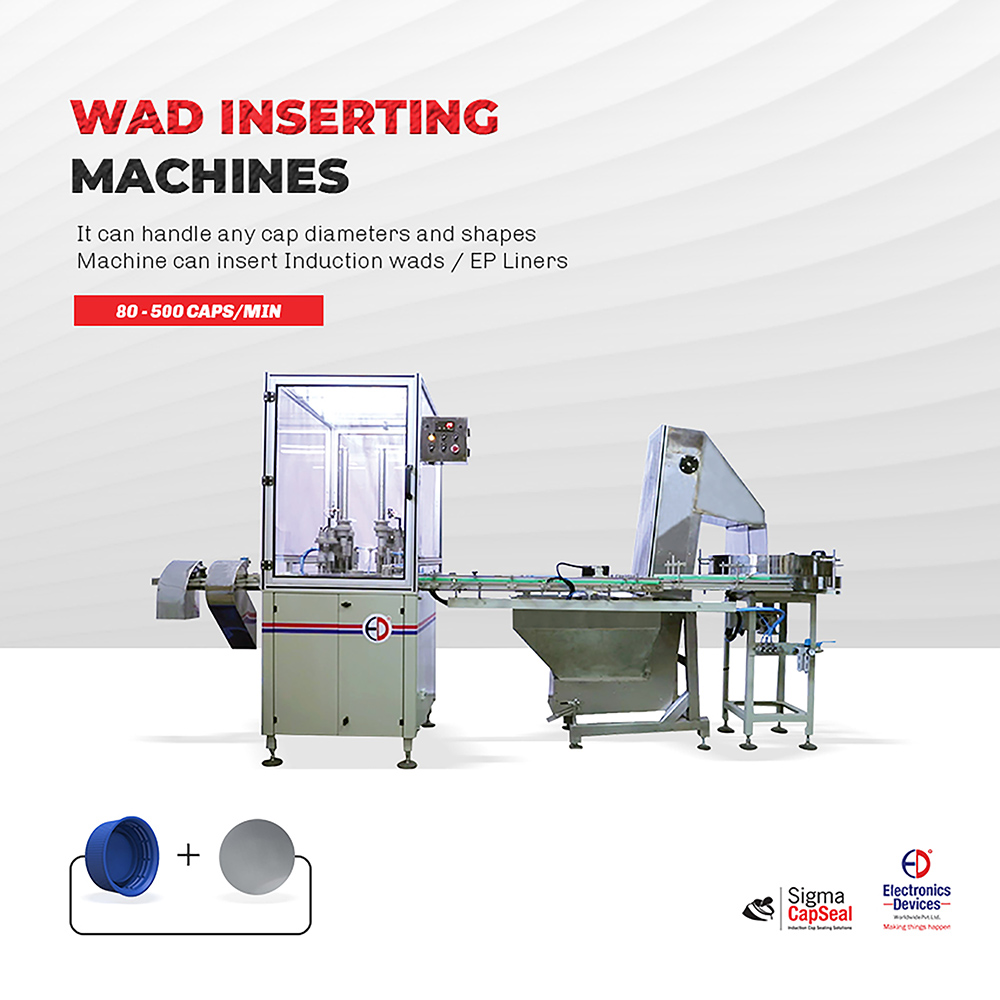
E.E: Tell us about the future improvement of your products?
V.C: Innovation and automation will continue to remain our focus areas. We remain dedicated to ensuring that our clients reap the numerous of automation. Packaging thousands of products manually without any errors is difficult. We understand that a single faulty product can be damaging to the brand’s value. So, we are here to simplify and improve the production standards of our clients.
E.E: Is there a special project that your products were used in?
V.C: We deal with industry giants from around the world. So, each project is special for us. Our teams ensure that we deliver only the best solutions to our clients. It is our dedication and commitment to top-notch services that have helped us grow and expand our business from its humble origins. I am proud of my team, and we look forward to continued excellence in our production standards and customer service.