Yamaha Surface Mount Technology (SMT) Section, a subdivision of Yamaha Motor Robotics Business Unit in Yamaha Motor Corporation, produces a complete selection of equipment for high-speed inline electronic assembly. This 1 STOP SMART SOLUTION includes solder paste printers, component mounters, 3D solder paste inspection machines, 3D PCB inspection machines, flip-chip hybrid placers, dispensers, intelligent component storage, and management software.
Bringing the Yamaha way to electronics manufacturing, these systems prioritize intuitive operator interaction, efficient coordination between all inline processes, and modularity enabling users to meet the latest manufacturing demands. Group competencies in servo-motor control and image recognition for vision (camera) systems ensure extreme accuracy with high speed.
The current product line includes the latest YR equipment generation, with advanced automated features for programming, setup, and changeovers, and new YSUP management software with state-of-the-art graphics and built-in data analytics.
Combining design and engineering, manufacture, sales, and service competencies, Yamaha SMT Section ensures operational efficiency and easy access to support for customers and partners. With regional offices in Japan, China, Southeast Asia, Europe and North America, the company provides truly global presence.
Yamaha Factory Automation Section (FA Section), a subdivision of Yamaha Motor Robotics Business Unit in Yamaha Motor Corporation, is focused on delivering flexible, high-accuracy industrial robots for precision automation challenges.
With its roots in the introduction of robot technology to Yamaha motorcycle assembly activities, the division has over 40 years’ experience solving automation challenges from factory-scale to micron-level. Yamaha’s industrial robots are now trusted by leading corporations worldwide, in activities as diverse as semiconductor fabrication and assembling electronic products, domestic appliances, automotive components, and large liquid-crystal panels.
Yamaha Motor FA Section offers a unified range of solutions for robotic assembly, including single-axis robots, SCARA, cartesian, and articulated robots. Innovations such as the LCMR200 linear conveyor module; a smoother, space-saving and more versatile successor to conventional belt and roller conveyors continue to set the pace in factory automation. Core robotic technologies as well as key components and complete robot systems are all produced in-house, ensuring consistent quality and control over lead-times.
Interview with Yasushi Miyake, Branch Manager of Yamaha Motor Europe, Robotics Business.
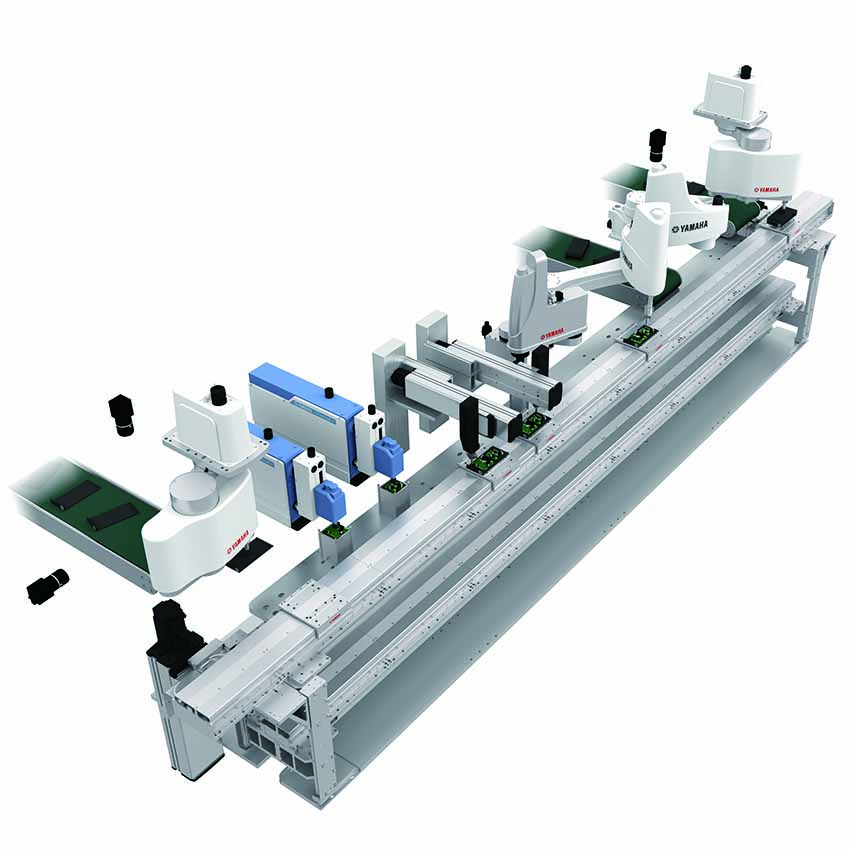
Easy Engineering: A brief description of the company and its activities.
Yasushi Miyake: Yamaha Robotics, host to two business sections: Surface-Mount Technology (SMT) and Factory Automation (FA), is part of the globally recognised Yamaha Motor Corporation, headquartered in Hamamatsu, Japan. At our European branch office in Germany, both sections offer sales and support services to our European customers.
The SMT Section is dedicated to Yamaha’s solutions for precision, high-speed assembly of electronic circuit boards. These include our 1 STOP SMART SOLUTION, which integrates highly automated equipment for building and inspecting assemblies, and the Yamaha YSUP smart factory software tools.
FA Section is responsible market for Yamaha’s industrial robots, which provide affordable, precision automation for a huge variety of sorting, picking, placing, and assembly processes. The portfolio extends down to desktop-sized robots, so they address a much broader range of applications than we often imagine, in industries like food production, textiles, and pharmaceuticals, as well as automotive and consumer electronics.
In addition to working directly with equipment end users, each business section also has its own network of sales agents and distributors, carefully selected for their market expertise and technical capabilities.
E.E: What are the main areas of activity of the company?
Y.M: SMT Section serves Europe’s original equipment manufacturers (OEMs) and electronic manufacturing services (EMS) businesses. We guide equipment selection to meet customers’ goals, and handle installation and commissioning, operator training, and support.
FA Section works directly with customers and their technical partners, third-party system integrators, and through our appointed agents, who are typically robot specialists, to solve process challenges using robots from our portfolio.
E.E: What’s the news about new products?
Y.M: Over the last couple of years, SMT Section has introduced the latest generation YR series surface-mount machines: the YRP10 printer, YRM20 component mounter, and YRi-V 3D optical inspection (AOI) machine. It’s been a busy time! The result is that our new lineup delivers even greater speed, repeatability, and efficiency. Automated features such as the printer’s auto stencil changeover and the mounter’s auto feeder change eliminate stoppage time between jobs and allow almost seamless and instantaneous changeovers.
In the new YRi-V 3D AOI machine, artificial intelligence now accelerates defect analysis and component recognition and state-of-the-art machine vision with new inspection algorithms enhance detection performance; particularly certain types of soldering defects that have always been tough to spot.
Most recently, we introduced new dual-lane machines, the YRP10 DL printer, YRM20 DL mounter, and YRi-V DL AOI. These are engineered to realise the maximum flexibility and enhanced throughput that dual-lane can offer, by making the full rail-width adjustment range and automated capabilities available on both lanes.
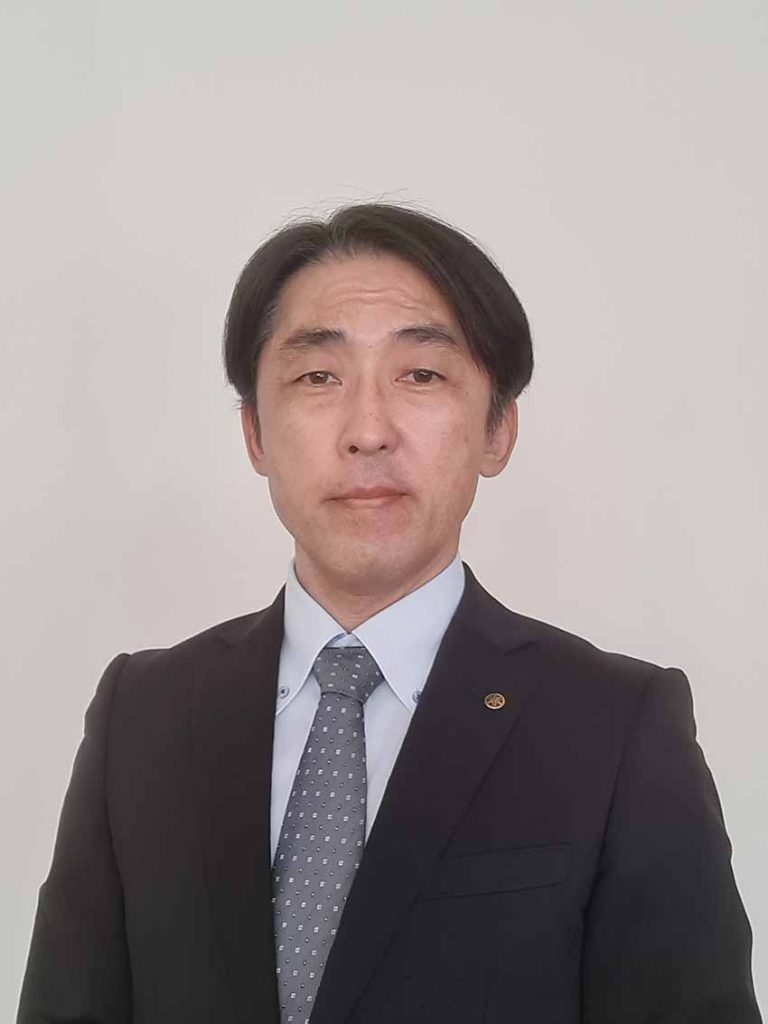
New features of our software tools include the YSUP Dashboard and the YSUP-LINK connectivity package. YSUP Dashboard helps users visualise production status. YSUP-LINK supports the latest protocols for integrating businesses’ operational technology (OT) and information technology (IT) domains.
Our Factory Automation section has introduced some great new products recently, including the YK-XE SCARA clean version series that make modernising and upgrading affordable for small and medium-sized organisations.
Also, this year, we debuted a new prototype 7-axis collaborative robot. With one more axis of movement than many current cobots, it increases dexterity and can do more within a smaller area. It’s great for companies that have little space but want to grow their business. Yamaha’s human sense technology, built-in, enhances safety and placement accuracy.
And we demonstrated our YK1200X SCARA in end-of-line handling for electric vehicle batteries. The programmable SCARA is fast and precise, as well as convenient and cost-effective. It can lift and accurately place loads up to 50kg, to position the heavy prismatic modules for electrical testing and then stacking in the battery pack.
E.E: What are the ranges of products?
Y.M: SMT Section markets our 1 STOP SMART SOLUTION, which closely integrates our cutting-edge screen printing, mounting, and inspection systems to maximise capabilities and productivity. The latest YRM generation, the YSM modular mounters, and Sigma mounters give customers flexible choices up to 200,000 cph. We also have hybrid mounters that can handle 3D substrates, and the YST15 intelligent component storage system.
We also have the YSUP suite of smart factory software tools, which provides applications for planning, monitoring, managing, and optimising equipment and processes.
FA Section has many variants of SCARA, cartesian, and single-axis robots that enhance the speed, repeatability, and efficiency of diverse industrial processes. The RCX-Studio graphical development tool lets users simulate, fine-tune, and program their applications offline for ease, speed, and efficiency.
And there are our LCMR200 modules for building production lines. Compared to ordinary conveyors typically used for workpiece transport, they are fast, quiet, and clean, with programmable stop positions, speed, and direction.
E.E: At what stage is the market where you are currently active?
Y.M: The SMT market is generally mature, populated by companies that are well established and who invest regularly to maintain their capabilities. Those producing technology for smart buildings, smart factories, and smart cities are growing particularly strongly.
Markets for industrial robots are still developing as companies everywhere are seeking affordable and flexible automation to solve their productivity challenges.
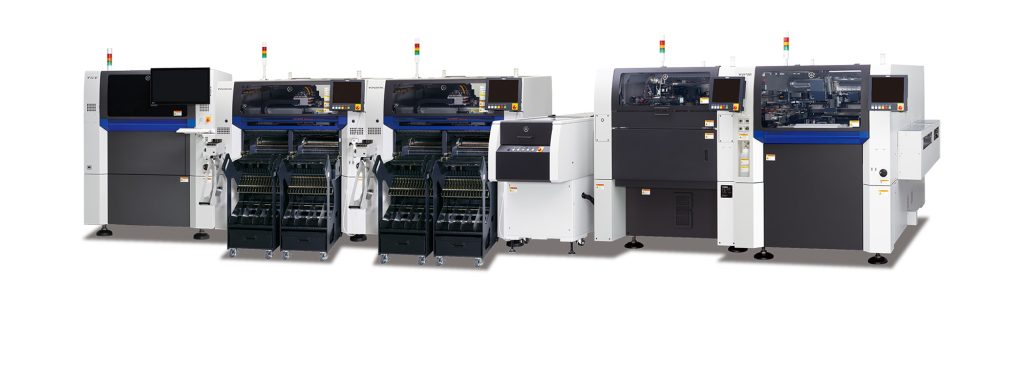
E.E: What can you tell us about market trends?
Y.M: Electronics manufacturing in Europe continues to grow, with trends like telehealth, IoT/IIoT, and automotive electrification powering innovation and driving demand for large numbers of connected smart electronic devices.
Throughout industry generally, more and more companies are understanding how industrial robots can help raise production output and quality.
E.E: What are the most innovative products marketed?
Y.M: Introducing artificial intelligence in the YRi-V 3D AOI raises inspection performance and efficiency to a new level. Combined with the new programming tools in YSUP software, YRi-V users can further accelerate new product introduction and raise production throughput. We are enhancing other equipment and software using AI, with its talents for anomaly detection and pattern recognition, to help further increase line utilisation and productivity.
E.E: What estimations do you have for 2023?
Y.M: Innovators are seeking solutions to problems such as climate change and energy security leveraging advanced technologies. So we expect Europe’s high-tech industries to remain strong, while other trends such as reshoring and the infusion of smart technologies in homes, factories, and cities will contribute to a generally healthy and growing manufacturing scene throughout the region.