micrometal Group (including micrometal GmbH, Etchform, and HP Etch) specialises in photochemical etching (PCE), producing ultra-precise metal components for various industries. The company offers customised solutions for creating intricate and complex geometries in thin metal sheets in a wide variety of metals, using advanced etching technologies like reel-to-reel and optimsed sheet etching.
micrometal Group’s services cater to industries such as automotive, medical technology, electronics, and aerospace, providing high-precision components like filters, springs, connectors, and stencils. The company emphasises design freedom, cost efficiency, and high-quality standards in its production processes.
Interview with Jochen Kern, Head of Sales & Marketing at micrometal Group.
What’s the news about new products/services?
Jochen Kern: micrometal Group provides a comprehensive range of services centered around PCE, including design assistance, prototyping, and mass production of precision metal parts. The company’s unique offerings include the ability to create extremely fine and complex structures with high precision, even in large volumes, and to process metals that are difficult to machine using conventional methods. micrometal Group stands out for its ability to maintain tight tolerances and provide custom solutions tailored to various industries.
What is the state of the market where you are currently active?
J.K: PCE has advanced significantly in recent years, offering unparalleled precision in producing intricate metal components. Unlike traditional machining, PCE allows for the creation of complex geometries with fine details, especially in thin metal sheets, without introducing mechanical stress or altering material properties. This makes it ideal for industries that require high precision and consistency. PCE is particularly advantageous over processes like laser cutting or stamping because it can achieve tighter tolerances and produce components with intricate patterns and smooth edges, which are often difficult or impossible to achieve with other methods.
In terms of market sectors, PCE is well-established in areas requiring miniaturisation and high precision. The automotive industry benefits from PCE for producing fuel system components such as filters and electronic connectors, while the medical sector uses it for creating surgical instruments and implants. The electronics industry relies on PCE for manufacturing intricate circuit boards and shielding components. As industries continue to demand smaller, more complex, and higher-quality metal parts, PCE remains a critical technology, often outperforming alternative methods in terms of cost-effectiveness, precision, and material integrity.
What can you tell us about market trends?
J.K: The key market trend driving the increased use of PCE as already mentioned is the growing demand for miniaturisation, especially in electronics, medical devices, and automotive components. As industries push for smaller, more precise parts with complex geometries, PCE becomes an attractive option due to its ability to produce fine details without compromising material integrity. Additionally, the rise in electrification, particularly in automotive and renewable energy sectors, necessitates highly accurate and intricate metal components, further boosting the adoption of PCE over traditional machining methods.
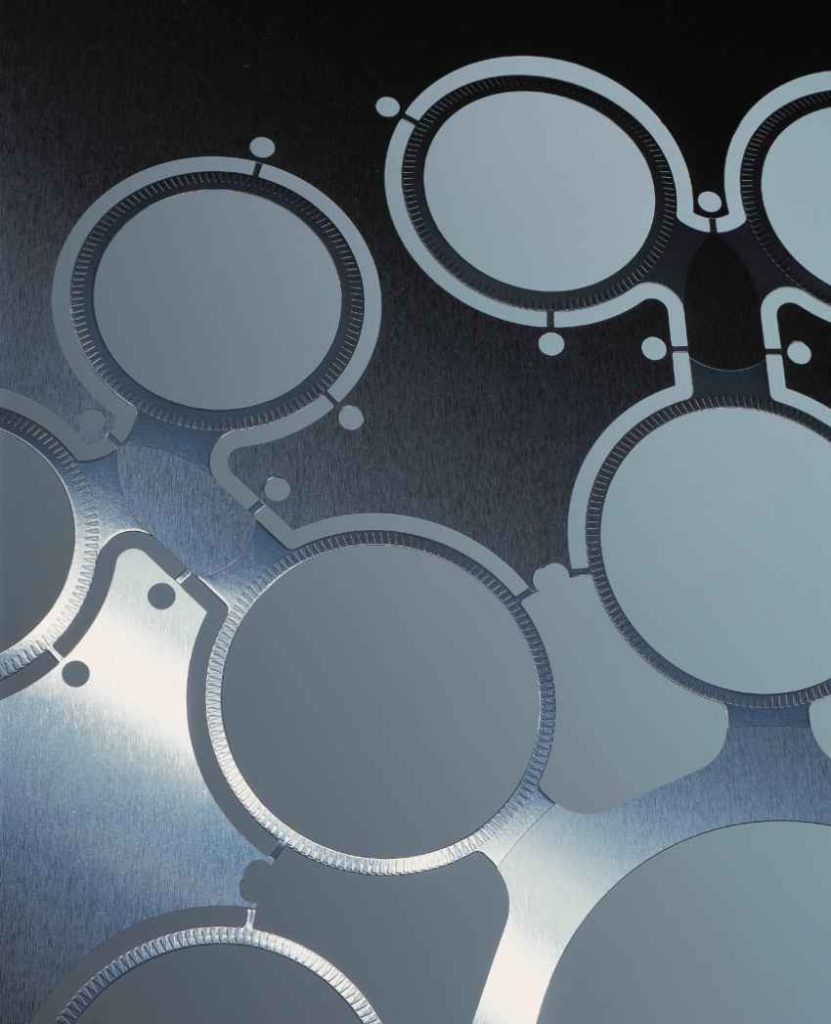
Another key trend is the shift towards customisation and rapid prototyping in manufacturing. Companies increasingly require flexible production methods that allow for quick iteration and small-batch production, which PCE efficiently supports. This need for adaptability, combined with the push for lightweight and durable components, is leading more industries to adopt PCE. The technology’s capability to meet high-precision demands, along with cost efficiency in producing complex parts, is driving a significant uptick in its utilisation across various sectors.
What are the most innovative products/services marketed?
J.K: micrometal’s reel-to-reel PCE process stands out as the company’s most innovative service due to its ability to produce high volumes of metal components with exceptional precision and consistency. This continuous process allows for the efficient handling of long metal strips, enabling the creation of intricate designs while maintaining extremely tight tolerances, often in the sub-micron range. By tightly controlling the etching environment, using glass tooing, and leveraging advanced automation, micrometal Group ensures that even complex geometries are produced with minimal variation, making it ideal for industries that require high volumes of consistent, precise components.
The reel-to-reel process is considered the “jewel in the crown” of micrometal Group’s PCE offerings because it combines high efficiency with unparalleled precision, enabling the mass production of components that meet strict industry standards. The process is particularly advantageous for applications where both high-volume production and precise tolerances are critical. micrometal Group’s ability to consistently deliver such high-quality components at scale sets them apart in the industry, making its reel-to-reel PCE process a key differentiator.
What estimations do you have for 2024?
J.K: micrometal Group is poised for strong performance through the remainder of 2024 and beyond, driven by the increasing demand for PCE across various industries. As industry continues to seek out high-precision, miniaturised components, micrometal Group’s advanced reel-to-reel PCE process and its optimised sheet PCE processes positions the company well to capture this growing market. With a reputation for delivering consistent quality and meeting the stringent requirements of high-volume applications, the company is well-positioned to benefit from ongoing industry trends and maintain robust growth.