Movacolor is the first choice of plastics producers worldwide that strive for excellence in injection molding and extrusion. Movacolor’s leadership in dosing technology is based on almost thirty years of partnership with plastics producers all over the world.
Interview with Lucas Leeuwenkamp, Junior Marketeer at Movacolor.
A brief description of the company and its activities.
Lucas Leeuwenkamp: Movacolor specialises in developing and selling (tailored) dosing, blending, and measuring solutions, predominantly for the plastics industry.
Movacolor’s solutions are modular, meaning they can be altered and combined to fit the changing demands of the production process. They integrate with Industry 4.0 technologies, allowing you to make your entire production line work together.
With intuitive designs, Movacolor enables its customers to be flexible in their growth ambitions and evolving needs by providing configuration possibilities. This helps tailor solutions to align with diverse plastic production processes.
What are the company’s main areas of activity?
L.L: Movacolor has a modern headquarters in Sneek, The Netherlands, where it has the knowledge and facilities to develop, assemble, and test all of its solutions. Together with its vast network of over 70 distributors, Movacolor supplies its customers all over the world. Each distributor specialises in the Movacolor dosing systems’ applications and plastics producers’ dosing requirements.
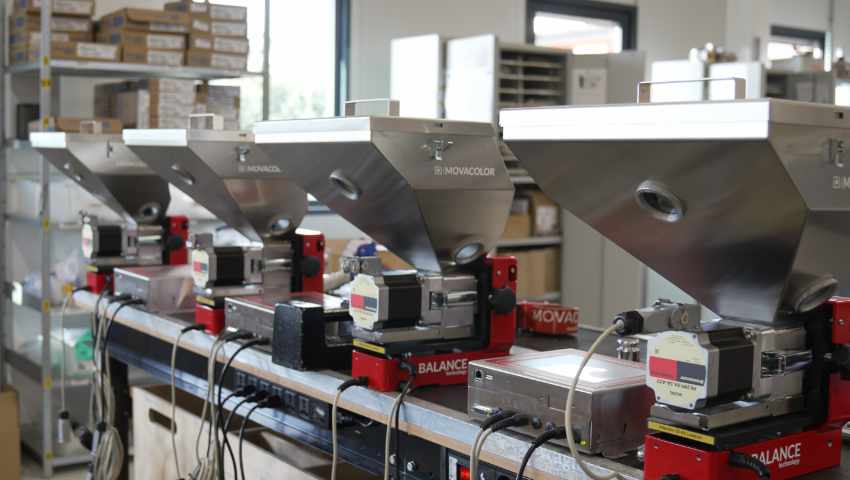
What’s the news about new products/services?
L.L: The MHBS Hybrid Blender is a patented solution that combines gravimetric technology and blending into one integrated solution. Created to help manufacturers improve their shot-to-shot blending accuracy while maintaining quick batch production for high-throughput applications.
Movacolor launched the new MDS Volumetric Feeder, setting the new standard for plastic volumetric dosing solutions. This new solution was specifically developed for manufacturers seeking a cost-effective way to significantly enhance material handling and operator efficiency in their production processes.
For producers looking for a safe way to access their dosing solutions, Movacolor created the MCS Off-line dosing. This solution allows Operators to access the machine without climbing dangerous ladders or even standing on the production line. With the MCS Off-line dosing, the MDS Balance is situated on a movable trolley or mounted in a convenient location. The MCS Off-line dosing makes the operator’s job safer and eliminates any possible vibrations from the production line that can affect the dosing accuracy.
What are the ranges of products/services?
L.L: Movacolor’s roots lie in the science of dosing. They were among the first to use gravimetric dosing technology in the plastics industry.
The product portfolio has expanded in the last few years, and Movacolor offers solutions in dosing, blending, and measuring. Additionally, their solutions effortlessly integrate with Industry 4.0, allowing manufacturers and their entire production lines to work together and collect and export valuable data about the production process.
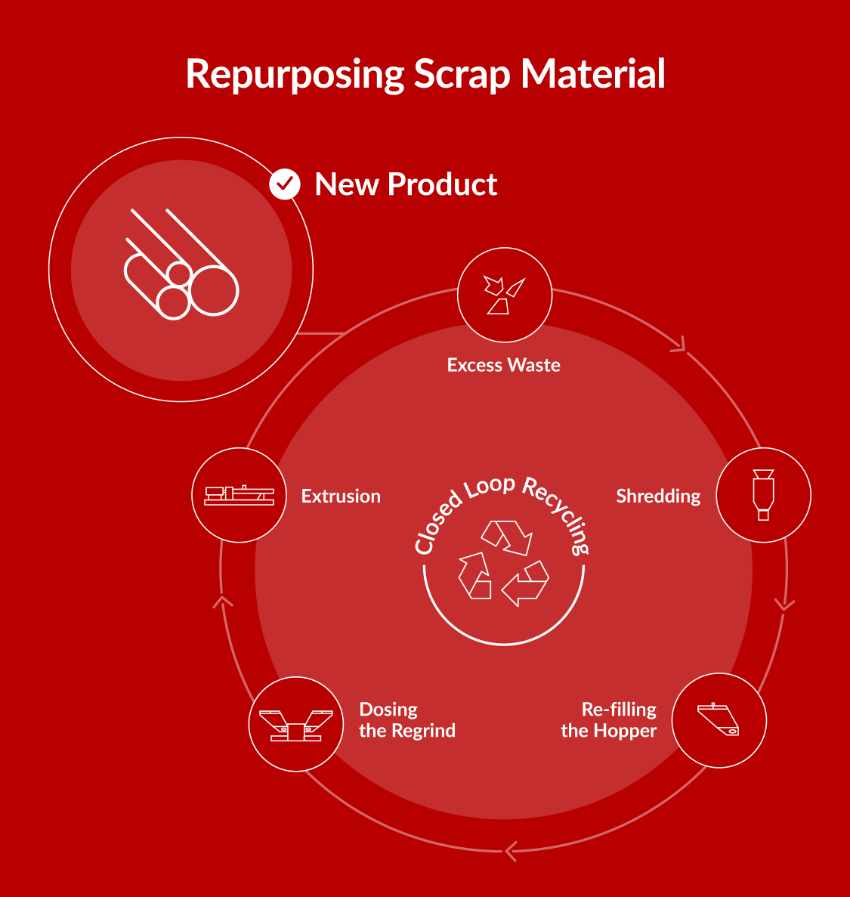
What is the state of the market where you are currently active?
L.L: The plastic production market is undergoing significant changes, driven by a strong focus on sustainability, cost efficiency, and material conservation, which are increasingly shaped by stringent government regulations. Companies are striving to reduce their environmental footprint while also meeting economic goals, which has heightened interest in technologies promoting waste reduction and recycling.
One key solution to address these market demands is Movacolor’s MCS Regrind system. The MCS Regrind is a closed-loop recycling solution that allows manufacturers to dose rejects and sprues in the form of regrind, which not only helps to reduce waste but also saves expensive additives. This aligns perfectly with the market’s demand for resource efficiency, enabling companies to meet regulatory and sustainability goals while optimising production costs.
What can you tell us about market trends?
L.L: Market trends in plastic production focus on sustainable materials, automation, and efficient processes. The industry is shifting towards integrated software solutions, enabling full production control from a central system, which optimises operations and enhances sustainability. Collaboration across the supply chain is key to meeting efficiency and environmental goals.
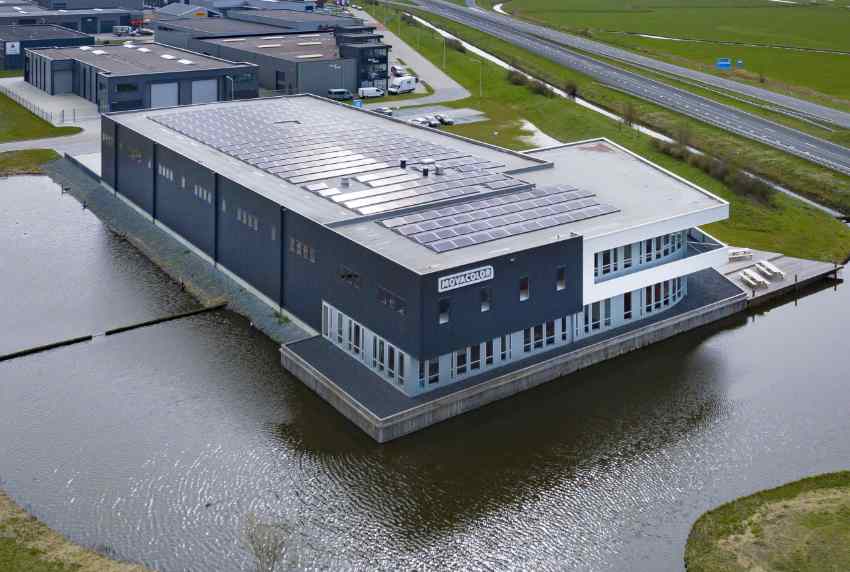
What are the most innovative products/services marketed?
L.L: Some of Movacolor’s most innovative products currently on the market are the MDS Balance, the MHBS Hybrid Blender and the MCS Regrind. These solutions are based on Movacolor’s Balance technology, a gravimetric dosing technology for precise material dosing that has been perfected over 25 years. In addition to the Balance technology Movacolor is also unique in its dosing cylinder. A tool that stands from the competition because they use a cylinder with a ridge to accurately dose the material instead of an auger that can miss some of the material because the material can fall off.
According to Jelle Wibo Elsinga, Process Engineer at Enitor Primo, switching from volumetric feeders to the MDS Balance has resulted in significant efficiency gains. “The customer gets a good product, and we don’t use too much raw material,” he noted, highlighting how these innovations support both quality and sustainability in production.
What estimations do you have for 2025?
L.L: For 2025, Movacolor anticipates a shift in the automotive industry toward using more sustainable materials, driven by growing environmental demands and regulatory pressures. As material costs continue to rise and raw materials become increasingly scarce, manufacturers will emphasise maximising material efficiency. Every grain of material must be carefully managed, and solutions like Movacolor’s precise dosing technologies will play a key role in ensuring sustainability, cost-effectiveness, and optimal resource utilisation across industries.