Founded in 1953, Trasmetal is an Italian finishing system company with 70 years of experience, but always with an eye on the future and innovation. Thanks to its know-how and experience in the design and construction of turnkey plants, the company is a leader in the field.
Trasmetal is a company dealing with steel works, which already has a stake in Faber. This year, as a first step towards a subsequent merger, they have acquired the units of Varnish Tech, an Italian company leader in the design and installation of painting systems for plastic components.
The goal of the company is to become an important player on the national territory, where a fragmentation of small companies prevails, and then of course in Europe and all over the world.
Interview with Luca Maitan, General Manager of Trasmetal S.p.A.
Easy Engineering: What are the main areas of activity of the company?
Luca Maitan: The main areas in which Trasmetal operates are automotive, aluminium, plastics, enamelling, electrophoresis (excluding car bodies), general industry. One sector can draw on the other for an exchange of expertise and process solutions. The company also provides an after-sales service able to guarantee spare-parts supply, technical operation specialists and also a constant monitoring of the state of the system with both scheduled visits by technicians with experience and remote assistance.
E.E: What’s the news about new products?
L.M: OFB electrostatic powder coating disk has been and still is one of Trasmetal most innovative products. It is a vertical powder coating device for aluminium profiles charging the powder within an on-board fluidized bed tank with high-voltage generators, each of which manages a series of electrodes that cover the entire disk circumference.
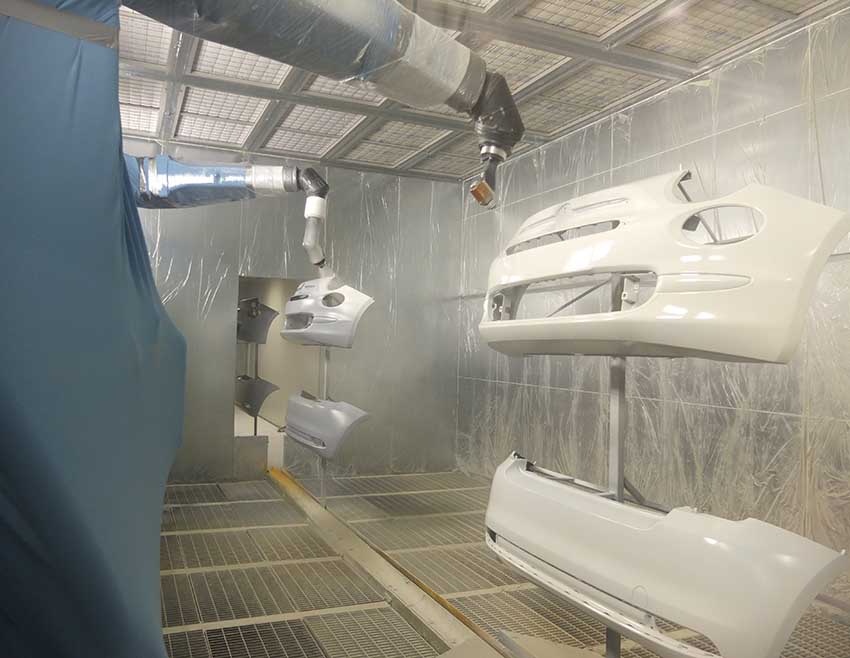
The on-board fluidized bed technology neutralizes problems of fluctuation in powder flow rate due to the important excursions of the application devices in vertical powder coating of profiles.
That’s why the tallest vertical powder line in the world, capable to coat profiles up to 12 meters long, is equipped with OFB disks.
The latest release of OFB disk is equipped with two separate air circuits, one for feeding the fluidised bed, while the other is an auxiliary circuit for continuous electrode cleansing and for supporting air/powder mixture emission. The most important innovation consists of the new solution adopted for the ionisation systems which, thanks to the particular geometry of the electrodes, allows the homogenization and maximising of the powder’s charge effect an instant before it is sent through the slots of the disk.
Recently, Trasmetal research department has developed a new patented application technology device, which we call “FINGER” which is in advance testing stage, that, among other substantial advantages, will raise the maximum production capacity of verticals beyond the limits known to date.
Regarding the pre-treatment phase, Trasmetal has just installed a vertical modular tunnel in Portugal, which consists of a special tunnel architecture that maximises accessibility and ergonomics. We expect that, given its clear practical (and aesthetic) superiority, it will become a global benchmark.
Moreover, the Tower booth, a type of booth that we are further developing to be able to offer two distinct models (U Tower – currently being installed in Portugal and S Tower, two being installed in Israel and one in UAE). The main feature is that in it the electrostatic equipment, instead of being moved on a full stroke (up and down from top to bottom as the profiles pass through) by a conventional reciprocator, is distributed on (divided among) overlapping trolleys that move on a partial stroke. Each carriage has its own independent drive. All carriages move on a single rack. During colour changes and/or maintenance, all trolleys are gathered at the base of the booth to facilitate operations. This architecture makes it possible to minimise the floor space of the booths (speeding up colour change times) and to increase the number of electrostatic equipment that can be placed there.
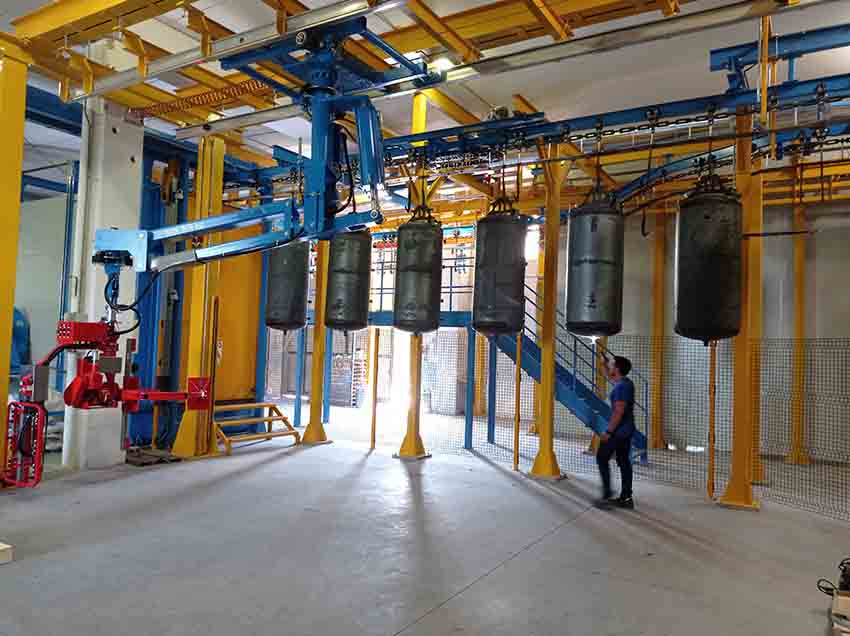
E.E: What are the ranges of products?
L.M: By joining forces with Varnish Tech, Trasmetal became a company capable of having in-house core activities such as engineering, carpentry, software, electrical panelling, robotics integration and paint plants. These services are crucial because today a plant is a set of structural calculations, hydraulics, electronics, fluid dynamics, aeraulic, robotics. The aim is to provide a complete service to the customer and guarantee the best value for money of the investment of a taylor-made plant. Our portfolio includes: powder and wet painting lines, dipping painting lines, enamelling lines, aluminium profiles painting lines vertical & horizontal, plastic painting lines, glass and plastic thermal and UV curing, robotics and automation of the painting process and paint kitchen. Trasmetal has a massive presence in the West with important installations, but with an eye on all areas of the world where there is demand for plants, from highly industrialised countries to emerging or developing countries that need more advanced solutions.
E.E: At what stage is the market where you are currently active?
L.M: All sectors of our market are showing growth trends, with the exception of the automotive sector, which is heavily penalised by the difficulty of finding raw materials. The market is also increasingly focused on green issues, both for a question of environmental sustainability and for a reduction in energy costs. Thanks to our technologies we are able to guarantee an adequate response to these new needs, which are not just a trend, but a new reality with which every sector must deal. For example, Trasmetal can provide the clients with a technology thought and realized with the aim to give benefits to the environment and save energy: on our plants provided of robotized painting booths we can install a recirculation air system, with a reduction of spray booths heating and cooling costs between 80 and 90%.
E.E: What can you tell us about market trends?
L.M: The market increasingly demands plants that are customised to meet the needs of small series or highly fragmented production runs. The various productions, even if small series, have painting cycles with a high complexity: they range from simple single-layer to cycles of primer, colour base and clearcoat; primer and enamel, both fired on fired and wet on wet; very often mixed cycles are applied, e.g. terracotta basecoat, subsequent sanding, and then application of colour base more transparent, and so on. Regarding specific products, we estimate an increase demand in enamelling boilers.
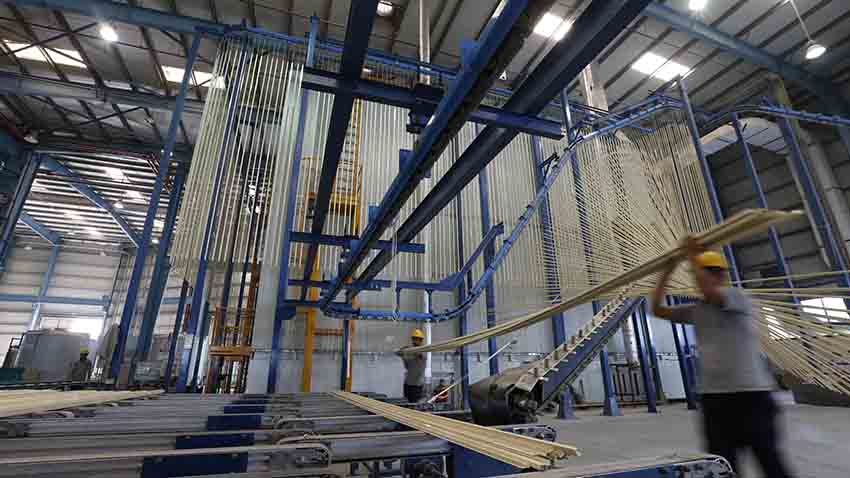
Still, we see an increase in installations for painting electric car accessories and components. On a different level, customers now also require strong corporate structure capable of responding to several requirements, including not only mechanical and plant engineering, but also documentation (e.g. performance level, regulatory compliance, manuals, logistics, etc.).
E.E: What are the most innovative products marketed?
L.M: As an innovation trend we must mention the transition from wet to dry systems, which may be cabins, washing, pre-treatment, etc.
E.E: What estimations do you have for 2023?
L.M: For 2023 we estimate a level of orders equal to that of 2022 and to increase our high level of assistance. We think Trasmetal has a high potential and we have all the know-how, experience and aspiration to meet the demand of both our historical as well as new customers.