HAINBUCH is a leader in clamping, change-over, measuring and automation solutions for milling, turning and grinding operations on machine tools.
Interview with Alexander Klug, Area Manager at HAINBUCH.
A brief description of the company and its activities.
Alexander Klug: We have been manufacturing in Germany since 1951 and are represented worldwide by subsidiaries and agencies.
We love what we do and want to make our customers, we’re talking about fans, a little bit better every day.
What are the main areas of activity of the company?
A.K: As a prominent manufacturer of workholding technology, our portfolio encompasses products tailored to every industry and machining process. This includes chucks, mandrels, stationary clamping devices, quick-change systems, and automation solutions. Our products primarily emphasize precision, optimization of set-up times, and the facilitation of networked and automated production.
We develop products that optimize our customers’ processes. Our solutions are unbeatably easy to use and guarantee maximum process reliability. We also attach great importance to quality and durability. We love the challenges that special solutions entail and work until we have found the perfect solution. There is hardly a workpiece for which we cannot offer a simple and efficient solution.
What are the ranges of products/services?
A.K: We do not see ourselves purely as a hardware supplier, but rather as a solution provider. We create seamlessness in the entire production process. That’s why we can be found in a wide range of industries – from automotive and mechanical engineering to aerospace and medical technology. We have been a valued technology supplier and OEM partner for decades. We guarantee optimum service and advice worldwide through our subsidiaries and agencies.
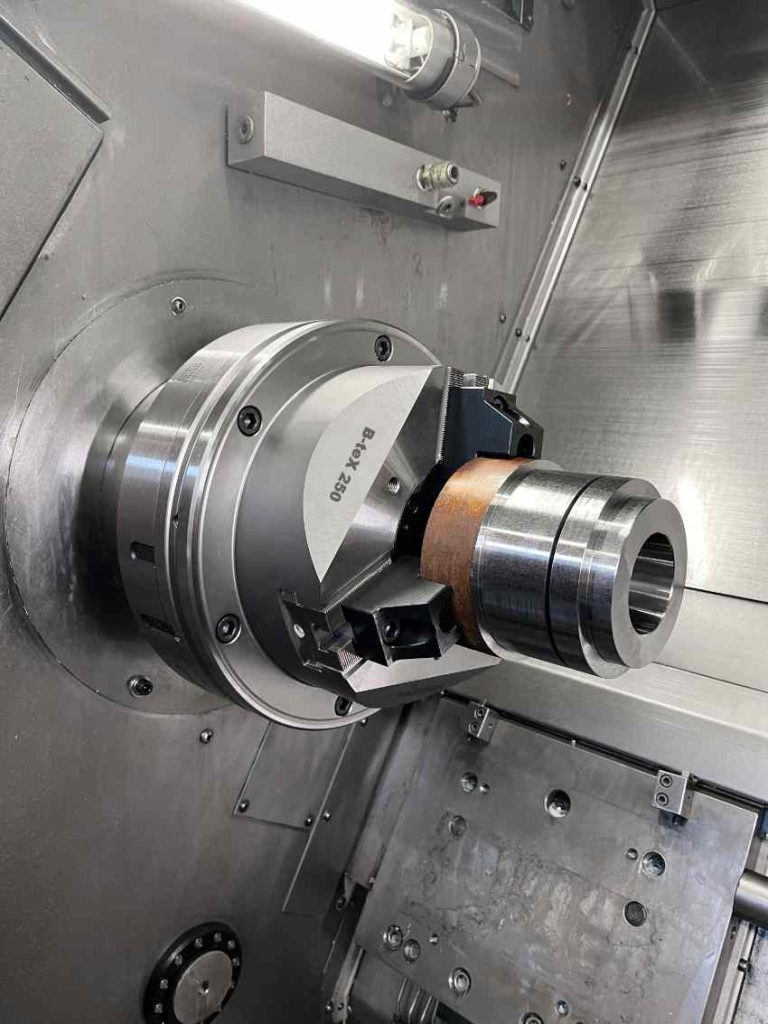
What’s the news about new products/services?
A.K: Reducing set-up times is a key factor in increasing efficiency in production. Hainbuch has been setting new standards for years with the centrotex quick change-over system. The system allows clamping devices to be changed in less than a minute, with consistently high precision. Hainbuch is now presenting the new B-Tex – a jaw chuck addition to the centrotex quick change-over system. This means that the working area for millturn machines can also be optimally utilized in the Z direction. In addition to the Toplus and Spanntop chucks for external clamping, the Maxxos and Mando clamping mandrels and the compensating 4-jaw chuck, the new 3-jaw chuck with a very low installation height completes the range of compatible clamping devices.
The Handling Line introduced in 2024 also supports users of the quick change-over interface when setting up, storing and transporting clamping devices. The set-up hoist, a further development of a mobile crane, is the centerpiece of the Handling Line. It allows clamping devices to be changed over quickly in any production hall, even without a gantry crane. The system is supplemented by a pallet system with clamping device holders, frames and covers. This optimizes upstream and downstream processes such as the storage and transport of clamping devices.
What is the state of the market where you are currently active?
A.K: Change in geopolitical conditions has become a constant and the resulting challenges are immense. It is also a fact that the general conditions for companies in Germany have not exactly improved in recent years (bureaucracy, taxes, shortage of skilled workers, working hours, etc.).
The challenge for us and our customers is to be able to continue manufacturing economically in the future. Our products for the shortest processing and set-up times with high efficiency and precision – and preferably automated – are very much in demand.
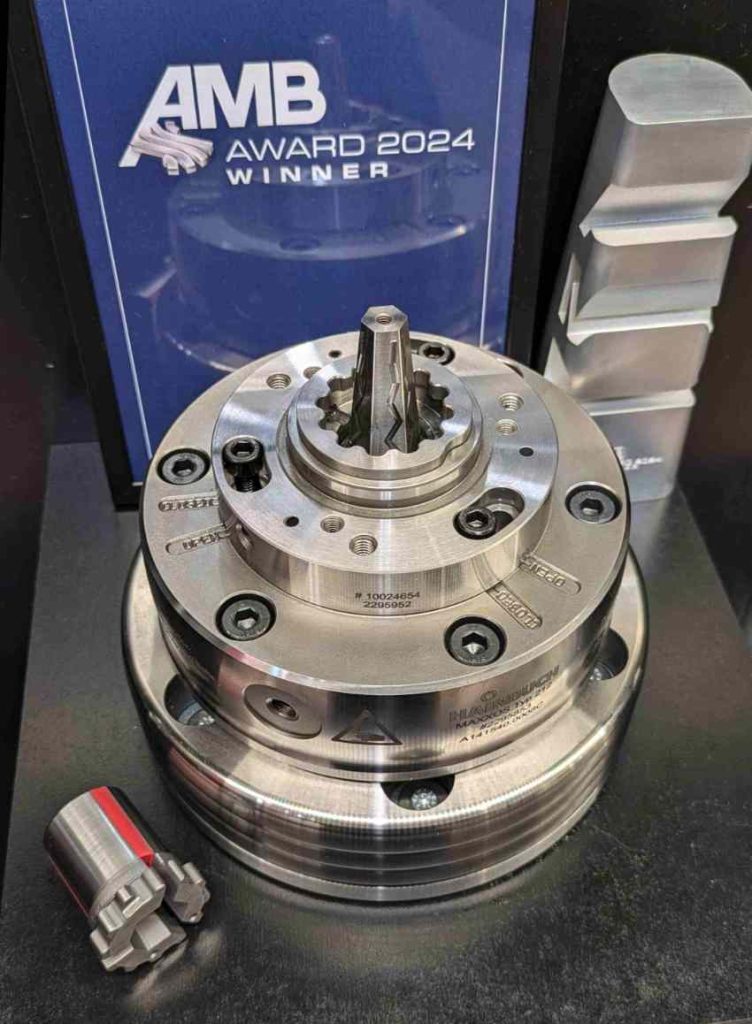
What can you tell us about market trends?
A.K: We are firmly convinced that the starting point of automation should be reliable workholding technology. We offer a starter version in which the clamping head can be changed over with or without the end-stop. This can be extended to changing entire clamping devices such as chucks or mandrels. It is crucial that the workholding technology runs with 100% process reliability. Thanks to our many years of experience, we know where chips and dirt occur and which components need to be checked for correct positioning. And we can even supply complete automated cells for turning and milling processes.
What are the most innovative products/services marketed?
A.K: HAINBUCH just recently won the AMB Award in the precision tools category for the Maxxos T212 mandrel. At AMB 2024, the International Exhibition for Metal Working held in Stuttgart, Germany, the expert jury presented the mandrel with an award in a category with a total of six nominated products. With its hexagonal pyramid shape, the Maxxos mandrel has been developed for maximum accuracy and feed rates. The hexagonal mandrel achieves a significantly higher holding power than the round Mando mandrel and enables up to double the torque transmission and corresponding cutting rates. Hainbuch offers the Maxxos T212 mandrel in 12 sizes for the diameter range 8mm to 200mm. The Maxxos T212 mandrel has no draw bolt. It is therefore ideal for workpieces with blind holes and very short clamping lengths without any loss of clamping length.
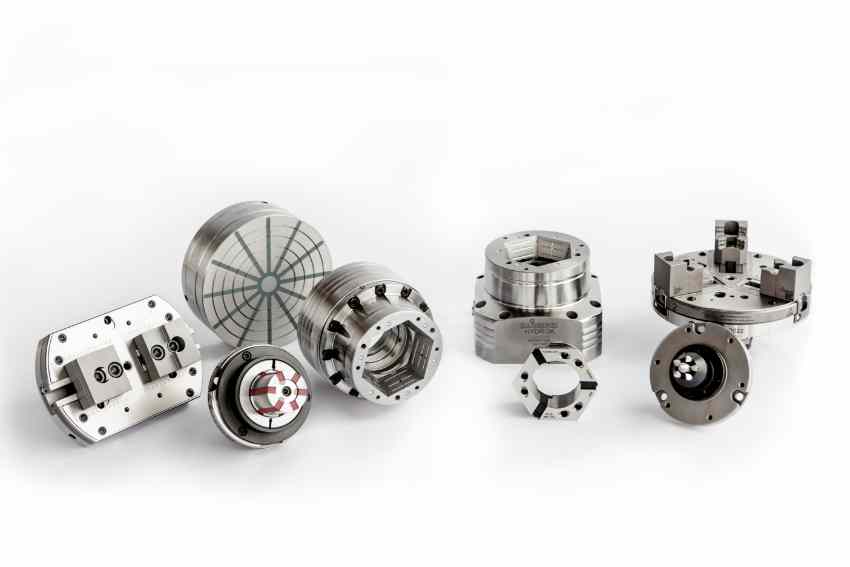
What estimations do you have for the rest of 2024?
A.K: Automation is right at the top of our agenda. We are only at the beginning of this development in our industry. Our products are designed with the future in mind right from the start and make automation possible. Reliable clamping, in-process and post-process measuring, our quick change-over technology and our expertise in automation are the key areas that we will continue to focus on in the long term.
HAINBUCH GMBH
SPANNENDE TECHNIK
Erdmannhäuser Straße 57
71672 Marbach